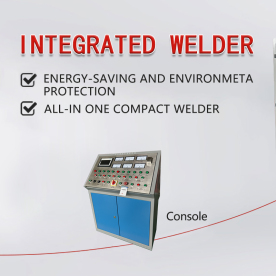
Exploring the Advantages and Innovations of Integrated Pipe Mill Production Line Systems in Modern Manufacturing
****
The manufacturing industry has been on a continuous journey of innovation and efficiency improvement, and one of the areas significantly benefiting from technological advancements is the pipe production sector. Integrated pipe mill production line systems have emerged as a revolutionary solution, optimizing the way pipes are manufactured. This article delves into the advantages and innovations that these systems bring to modern manufacturing, examining how they contribute to increased productivity, reduced costs, and enhanced product quality.
At the heart of an integrated pipe mill production line system is its ability to combine various stages of pipe manufacturing into a single, cohesive process. Traditional pipe manufacturing often involves several distinct steps, including forming, welding, and finishing, each requiring different machinery and handling systems. This fragmentation can lead to inefficiencies, increased labor costs, and higher rates of material wastage. In contrast, an integrated system streamlines the entire operation, reducing the need for multiple setups and minimizing the time required to transition between different production phases.
One of the major benefits of an integrated pipe mill production line system is the significant boost in production capacity. By automating and synchronizing various processes, manufacturers can achieve a higher output in a shorter time frame. This automation minimizes human error, ensures consistent quality, and enhances the overall reliability of the manufacturing process. For instance, advanced technologies such as computer numerical control (CNC) machines and robotics allow for precise control over production parameters, leading to a higher-quality final product.
In addition to increased efficiency, integrated pipe mill production lines are designed with flexibility in mind. Modern manufacturing often necessitates the ability to produce different types of pipes with varying specifications to meet diverse customer demands. Integrated systems can be easily adjusted to accommodate these changes, enabling manufacturers to quickly switch between products without significant downtime. This adaptability is particularly crucial in a market where customer preferences can shift rapidly, and the ability to respond promptly can offer a competitive edge.
Another crucial aspect of integrated pipe mill production line systems is their contribution to sustainability and waste reduction. With integrated systems, manufacturers can optimize material usage throughout the production process, significantly reducing scrap and offcuts. Improved energy efficiency is also a vital component, as integrated solutions often incorporate modern technologies that minimize power consumption. This eco-friendliness aligns with the growing focus on sustainable manufacturing practices, appealing to environmentally-conscious consumers and industries alike.
Moreover, integrated systems enhance safety within the manufacturing environment. By reducing the number of manual handling operations required in traditional setups, the risks associated with work-related injuries can be significantly lowered. Automation can streamline repetitive tasks, allowing human operators to focus on more complex and strategic aspects of the production process, thus further reducing the likelihood of accidents.
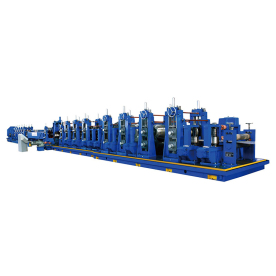
Exploring the Advantages and Innovations of Integrated Pipe Mill Production Line Systems in Modern Manufacturing

Exploring the Advantages and Innovations of Integrated Pipe Mill Production Line Systems in Modern Manufacturing
The role of data in the operation of integrated pipe mill production line systems cannot be understated. These systems often employ sophisticated monitoring and analytics tools, allowing manufacturers to gather real-time data on various aspects of the production process. By analyzing this information, companies can identify areas for improvement, maintain optimal operating conditions, and predict maintenance needs before issues arise. This proactive approach to production management not only enhances efficiency but also contributes to cost savings over time.
In conclusion, integrated pipe mill production line systems represent a significant leap forward in the manufacturing of pipes. The advantages of increased productivity, flexibility, and sustainability, combined with enhanced safety and data-driven decision-making, make these systems essential in meeting the challenges of modern manufacturing. As industries continue to evolve, investing in integrated systems will be crucial for manufacturers looking to improve their operations and remain competitive in an ever-changing market. The future of pipe production is undoubtedly intertwined with the innovations brought by these integrated systems, paving the way for a more efficient, safe, and sustainable approach to manufacturing.Reliable Spare Parts for Cold Cutting Saws