In today’s rapidly evolving manufacturing environment, efficiency and versatility are paramount. A significant innovation in the field of welding technology is the High-Efficiency All-in-One Welding System. This advanced system amalgamates several welding methods into one compact unit, allowing welders to perform various tasks with enhanced productivity and precision. This article explores the features, benefits, and applications of this remarkable system that is reshaping the landscape of metal fabrication and welding.
Understanding the High-Efficiency All-in-One Welding System
The High-Efficiency All-in-One Welding System is designed to provide users with multiple welding functionalities, including MIG, TIG, and Stick welding, all within a single device. This versatility ensures that fabricators can tackle a wide range of projects without the need for multiple machines, saving both time and space in the workshop.
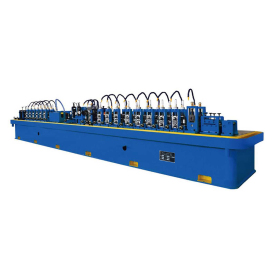
Revolutionizing Metal Fabrication: Insights into the High-Efficiency All-in-One Welding System for Modern Welding Applications
Modern systems are often equipped with advanced digital interfaces that allow for easy adjustments and real-time monitoring. This not only simplifies the welding process but also enhances operator precision and quality control. Equipped with powerful inverter technology, these systems ensure that energy consumption is minimized while maintaining high output levels, thus achieving greater efficiency.
Key Features
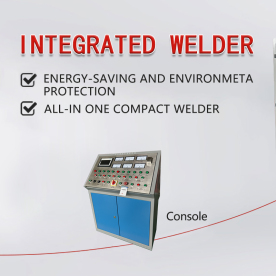
Revolutionizing Metal Fabrication: Insights into the High-Efficiency All-in-One Welding System for Modern Welding Applications
1. **Versatility**: The ability to perform different welding processes on a single machine is a game-changer. Whether it’s thin sheet metal or thicker materials, the High-Efficiency All-in-One Welding System can adapt to the task at hand, allowing for seamless transitions between different types of welding.
2. **User-Friendly Digital Controls**: Many high-efficiency models come with intuitive digital interfaces that make it easy for users to set welding parameters. This feature significantly reduces the learning curve for new users and ensures that seasoned professionals can quickly switch settings based on their project needs.
3. **Mobility and Portability**: Given its all-in-one design, these systems are often more compact and portable than traditional setups. This is especially advantageous for on-site jobs, where transporting multiple machines can be cumbersome.
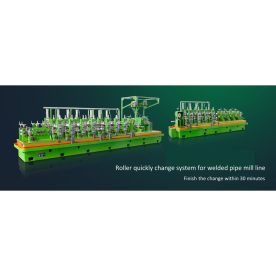
Revolutionizing Metal Fabrication: Insights into the High-Efficiency All-in-One Welding System for Modern Welding Applications
4. **Energy Efficiency**: Equipped with inverter technology, these welding systems are designed to operate efficiently, consuming less electricity without sacrificing performance. This not only reduces operational costs but also contributes to a more sustainable working environment.
5. **Advanced Safety Features**: Safety is vital in welding operations, and modern all-in-one systems are designed with this in mind. Features such as thermal overload protection, gas safety shut-off, and protective casings help ensure a safe working environment for operators.
Benefits of Using a High-Efficiency All-in-One Welding System
1. **Cost-Effectiveness**: Investing in a single multipurpose welding system can be significantly more cost-effective than purchasing multiple separate machines. This not only saves initial capital expenditure but also reduces long-term maintenance and repair costs.
2. **Space Saving**: Workshops often face constraints in space, and having a single machine that serves multiple functions can free up valuable room for other essential tools and equipment.
3. **Increased Productivity**: By reducing setup time and enabling quick changes between different welding processes, operators can complete projects more rapidly. This efficiency translates into faster turnaround times and increased output, which is crucial for meeting project deadlines.
4. **Skill Development**: The integrated nature of the system allows new welders to gain proficiency in multiple techniques simultaneously, making them more versatile and valuable to their employers.
Applications in Various Industries
The High-Efficiency All-in-One Welding System has applications across multiple sectors, including automotive, construction, manufacturing, and repair. It is particularly advantageous in environments where workpieces vary in size and material composition. For example, in automotive repair, technicians can swiftly switch between processes to handle different types of metals without changing machines.
In manufacturing settings, these systems enhance assembly line operations by allowing for quick adaptations to changing project needs. Their portability and ease of use also make them ideal for onsite construction and maintenance, where space and time constraints are significant.
Conclusion
The High-Efficiency All-in-One Welding System is a transformative technology in the welding industry, offering unparalleled efficiency, versatility, and safety. As industries continue to seek ways to enhance productivity while minimizing costs, these advanced systems stand out as vital tools for achieving operational excellence. By embracing this innovative technology, welders of all experience levels will be better equipped to meet the challenges of modern fabrication tasks, paving the way for a more efficient and productive future in the welding field.Replacement Moulds for Tube Mills