In today’s competitive manufacturing landscape, efficiency, precision, and product quality are paramount for success. Leveraging advanced technology and innovative solutions, manufacturers are constantly seeking ways to optimize their production processes. One critical piece of equipment that plays a central role in this quest for excellence is the pipe making machine. With the rise of diverse industries requiring specialized pipes, the demand for customized pipe making machine solutions has surged. This article explores the various customization options available for pipe making machines and how they can significantly enhance manufacturing capabilities.
**Understanding Pipe Making Machines**
Pipe making machines are sturdy, complex systems designed to produce pipes of varying sizes, materials, and specifications. These machines can manufacture pipes used in various applications, including plumbing, construction, and automotive industries. Traditionally, these machines were limited to producing standard sizes and designs. However, as the market has evolved, so too has the need for more versatile and customizable options.
**Customization Solutions: Meeting Diverse Industry Needs**
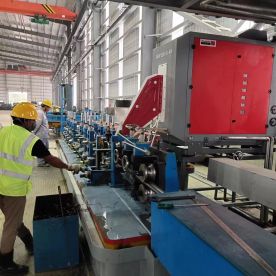
Innovative Pipe Making Machine Customization Solutions: Transforming Production Efficiency and Enhancing Product Quality for Modern Manufacturers
1. **Tailored Design Specifications**
One of the foremost customization solutions for pipe making machines is the ability to modify design specifications to meet individual customer needs. Different industries require pipes with unique dimensions, thicknesses, and material compositions. By collaborating with manufacturers, industry stakeholders can define specifications that align with their specific requirements. Modern pipe making machines can be equipped with adjustable molds and templates that allow for the seamless production of custom pipe sizes.
2. **Material Flexibility**
Advancements in materials science have introduced a variety of new materials that manufacturers might want to utilize for their pipe production. A customizable pipe making machine can be designed to handle different materials, including PVC, HDPE, metal alloys, and more. The inclusion of specialized feeding systems and temperature controls ensures the optimal processing of these materials, leading to enhanced product quality and durability.
3. **Integration of Advanced Technology**
Today’s manufacturers are increasingly incorporating smart technologies into their production processes. Customization solutions for pipe making machines can include integrating Internet of Things (IoT) capabilities, allowing for real-time monitoring and data analysis. This integration enhances efficiency, as it enables manufacturers to track production metrics, identify potential issues, and optimize operations proactively.
4. **Automated Production Features**
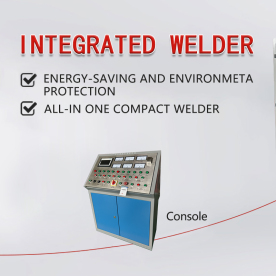
Innovative Pipe Making Machine Customization Solutions: Transforming Production Efficiency and Enhancing Product Quality for Modern Manufacturers
Automation is a game-changer in manufacturing, and incorporating automated features into pipe making machines can significantly boost productivity. Custom solutions can include robotic arms for handling operations, automatic feeding systems, and intelligent quality control mechanisms. These features not only minimize labor costs but also reduce human error, ensuring a more consistent quality of the produced pipes.
5. **Flexible Production Capabilities**
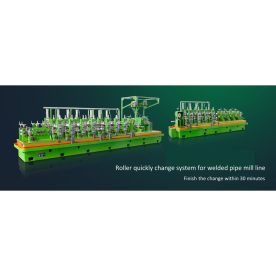
Innovative Pipe Making Machine Customization Solutions: Transforming Production Efficiency and Enhancing Product Quality for Modern Manufacturers
The demand for smaller production runs and increased variety has made flexible manufacturing essential. Customization solutions that enable manufacturers to switch between different pipe types and sizes effortlessly can greatly enhance productivity. Modular machine designs that allow for easy adjustments help meet fluctuating market demands without incurring substantial downtime.
6. **Environmentally Friendly Options**
As sustainability becomes increasingly crucial, manufacturers are urged to adopt eco-friendly practices. Customization solutions for pipe making machines can include the implementation of energy-efficient systems and waste-reducing technologies. Incorporating recyclable materials into the production process, along with implementing energy-saving modes during operation, aligns with global sustainability efforts while meeting consumer expectations.
7. **Enhanced Training and Support Services**
Finally, providing robust training and support services as part of the customization solution can make a significant difference. Manufacturers should ensure their staff is well-trained to operate and maintain the customized machines efficiently. Ongoing technical support can help troubleshoot issues and ensure that the machines operate at peak performance throughout their lifecycle.
**Conclusion**
In summary, the demand for customized pipe making machine solutions is on the rise as manufacturers seek to improve efficiency, enhance product quality, and remain competitive in a rapidly changing market. By investing in tailored designs, material flexibility, advanced technologies, automation, and sustainability options, manufacturers can transform their production processes and meet the diverse needs of their industries. Ultimately, the future of pipe manufacturing lies in innovation and customization, paving the way for a more efficient and quality-driven production environment.Automatic Solid state HF welder