In the manufacturing sector, particularly in industries involved in tube production, the quality of the moulds used plays a pivotal role in determining the efficiency and the overall integrity of the products. Among the various advancements in production technology, the introduction of durable mould for tube mills is noteworthy. This innovative approach not only streamlines the production process but also ensures that the end products meet high standards of quality and durability. In this article, we will delve into the benefits of using durable moulds in tube mills and how they contribute to enhanced manufacturing performance.
Understanding Tube Mills and Their Importance
Tube mills serve as essential machinery used for producing welded and seamless tubes, which are widely utilized in various applications, including construction, automotive, and aerospace sectors. The processes employed in tube mills require precise engineering and high-quality materials to ensure that the products deliver optimal performance. Therefore, the decision to invest in durable moulds becomes critical in this context.
The Role of Durable Mould in Tube Production
Durable moulds are crafted from high-strength materials designed to withstand the incessant pressures of the manufacturing process. These moulds are intricately designed to create tubes with specific outer diameters, wall thicknesses, and lengths that adhere to stringent industry standards. By utilizing durable moulds, manufacturers can achieve better dimensional accuracy and consistency in their products, reducing the likelihood of defects and rejections.
Furthermore, the durability of the moulds translates to lower maintenance costs and less frequent replacements. Tube mills often operate at high speeds and under significant pressure, which can wear out traditional moulds relatively quickly. With durable moulds, the longevity of the equipment is enhanced, which not only offers cost savings through reduced downtime and less frequent purchases but also increases overall production efficiency.
Reducing Production Costs and Time
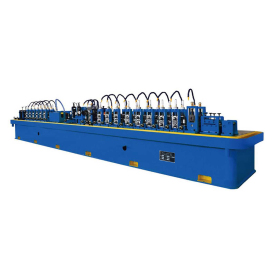
The Advantages of Utilizing Durable Mould for Tube Mills: Enhancing Efficiency and Production Quality
One of the significant advantages of employing durable mould for tube mills lies in its potential for reducing production costs and time. Durable moulds facilitate a smoother manufacturing process by promoting higher output levels and minimizing defects that would otherwise necessitate rework. The improved efficiency and higher production rates ensure that manufacturers can meet market demands promptly while keeping operational costs in check.
In high-demand environments, the ability to produce more tubes in a shorter timeframe equates to improved profitability. Additionally, the consistent quality ensured by durable moulds can lead to greater customer satisfaction and repeat business, further solidifying a company’s position in the market.
Enhancing Product Quality and Performance
The quality of the end product is another critical aspect that manufacturers must consider. Durable moulds contribute significantly to the overall performance of tubes produced. They enable the production of uniform thickness and structural integrity, essential characteristics for tubes used in high-stress applications. By maintaining precise tolerances, these moulds enhance the mechanical properties of the tubes, such as tensile strength and resistance to fatigue.
Moreover, the surface finish of the tubes is paramount for certain applications. Durable moulds can impart better surface quality, reducing the need for further finishing processes. This means that the products can be ready for use straight from the tube mill, decreasing lead times and improving the supply chain.
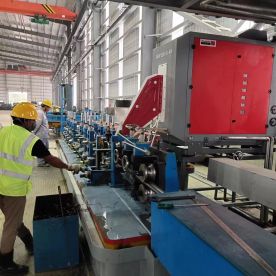
The Advantages of Utilizing Durable Mould for Tube Mills: Enhancing Efficiency and Production Quality
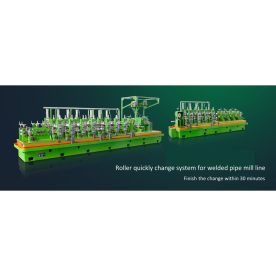
The Advantages of Utilizing Durable Mould for Tube Mills: Enhancing Efficiency and Production Quality
Conclusion
In conclusion, the integration of durable mould for tube mills represents a significant advancement in manufacturing technology. These moulds not only boost production efficiency and reduce costs but also ensure the production of high-quality tubes that meet or exceed industry standards. As manufacturers continue to seek ways to enhance their operational processes, the adoption of durable moulds stands out as a crucial strategy for achieving long-term success in the competitive marketplace. Investing in durable moulds ultimately leads to higher productivity, substantial savings, and improved customer satisfaction, making them an indispensable asset in the realm of tube manufacturing.Precision-Ground HSS Blade