In today’s rapidly evolving industrial landscape, the efficiency and productivity of manufacturing processes are paramount. Among the numerous innovations spurring this change, the Integrated Pipe Mill Production Line System stands out as a game-changer. This comprehensive system is designed to streamline and enhance the production of pipes, facilitating a more integrated approach to manufacturing that ultimately benefits both producers and consumers. In this article, we will delve into the significance of Integrated Pipe Mill Production Line Systems, how they operate, and the advantages they offer to manufacturers navigating the complexities of modern industrial requirements.
Understanding Integrated Pipe Mill Production Line Systems
An Integrated Pipe Mill Production Line System refers to a technologically advanced setup that encompasses various stages of pipe manufacturing, from raw material processing to the final product output. These systems are characterized by their seamless integration of processes, allowing for a continuous flow of production without the need for separate stages to stop and start. This integration includes stages such as piercing, elongation, forming, welding, and finishing, all orchestrated within a singular, cohesive unit.
Unlike traditional pipe manufacturing setups, which often rely on multiple independent machines and processes that can lead to inefficiencies and higher operational costs, the Integrated Pipe Mill Production Line System ensures that every component functions in harmony. This cohesive approach not only increases production speed but also enhances the precision and quality of the final product.
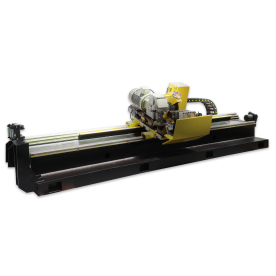
Revolutionizing Manufacturing: The Significance and Advantages of Integrated Pipe Mill Production Line Systems in Modern Industry
Key Components of Integrated Pipe Mill Production Line Systems
An Integrated Pipe Mill Production Line System is composed of several key components that work in unison to optimize the manufacturing process:
1. **Raw Material Preparation**: The system begins with efficient raw material handling to ensure consistency in the inputs, which can include various types of steel or other materials suitable for pipe manufacturing.
2. **Piercing Mill**: This component is responsible for creating an initial hole in the raw material, enabling the subsequent elongation process. Modern piercing mills are designed for high-speed operations and can handle a variety of material shapes and sizes.
3. **Elongation and Forming Units**: These units transform the pierced material into a tubular shape. Advanced technology allows for precise control over dimensions and wall thickness, meeting specific industrial requirements.
4. **Welding Process**: One of the most critical phases in pipe manufacturing, the welding units are integrated to ensure high-quality, leak-proof joints. Depending on the type of pipe being produced, various welding techniques, such as high-frequency induction welding or submerged arc welding, can be employed.
5. **Finishing Units**: After welding, pipes undergo several finishing processes, including trimming, coating, and quality testing. This ensures that the final products meet industry standards and customer specifications.
Advantages of Integrated Pipe Mill Production Line Systems
1. **Increased Efficiency**: The primary advantage of the Integrated Pipe Mill Production Line System is its ability to enhance operational efficiency. By minimizing manual handling and streamlining processes, manufacturers can achieve higher output levels without a corresponding increase in labor costs.
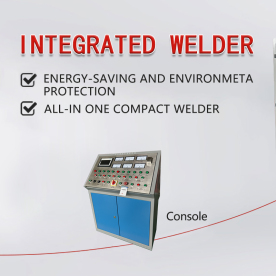
Revolutionizing Manufacturing: The Significance and Advantages of Integrated Pipe Mill Production Line Systems in Modern Industry
2. **Cost-Effectiveness**: Through greater efficiency, these integrated systems often lead to reduced production costs. The ability to produce higher volumes with less waste translates directly into savings, benefiting manufacturers’ bottom lines.
3. **Improved Quality Control**: Integration allows for better oversight of the production process, leading to more consistent quality. Automated systems can monitor various parameters in real time, ensuring that any deviations are swiftly corrected before they impact the final product.
4. **Flexibility and Customization**: Integrated systems can be designed to handle a wide variety of products, allowing manufacturers to quickly adapt to changing market demands and customize products according to client specifications. This flexibility is essential in an environment where customization is increasingly valued.
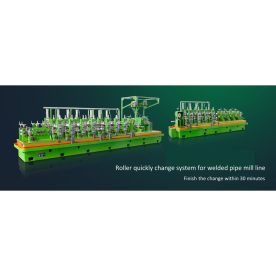
Revolutionizing Manufacturing: The Significance and Advantages of Integrated Pipe Mill Production Line Systems in Modern Industry
5. **Enhanced Safety**: By automating many of the processes involved in pipe manufacturing, Integrated Pipe Mill Production Line Systems reduce the risks associated with manual labor, thereby enhancing workplace safety for operators.
Conclusion
The Integrated Pipe Mill Production Line System represents a significant advancement in the industrial manufacturing sector, particularly in the production of pipes. By harnessing the power of technology and integration, manufacturers can produce high-quality products at lower costs and with improved efficiency. As industries continue to demand faster, more reliable, and cost-effective solutions, the adoption of Integrated Pipe Mill Production Line Systems is likely to grow, shaping the future of pipe manufacturing and setting new standards for what is possible in the manufacturing world.High frequency welder equipment