Industrial induction heating equipment is revolutionizing the way various manufacturing processes are conducted across a multitude of industries. This technology employs electromagnetic induction to generate heat, allowing for precise heating of materials, primarily metals, without direct contact. As industries continue to seek more efficient, cost-effective, and environmentally friendly solutions, understanding induction heating equipment’s significance and diverse applications is crucial for businesses looking to remain competitive in today’s rapidly advancing market.
At its core, industrial induction heating utilizes the principle of electromagnetic induction. When an alternating current passes through a coil, it generates a magnetic field. When conductive materials enter this magnetic field, eddy currents are induced, which leads to the generation of heat within the material itself. This method of heating is highly efficient, as nearly all thermal energy is generated within the workpiece, minimizing wasted energy and ensuring rapid temperature increases.
One of the most prominent applications of industrial induction heating equipment is in metal hardening. This process involves heating metals, such as steel or aluminum, to a specific temperature to enhance their mechanical properties, followed by rapid quenching. Induction heating allows for precise control over the heating process, resulting in uniform hardening and improved quality of the final product. This capability is particularly beneficial in industries such as automotive manufacturing, aerospace, and heavy machinery, where component durability is essential for safety and performance.
Another application is in the field of brazing and soldering. Induction heating equipment enables manufacturers to join dissimilar metals together efficiently. The ability to focus heat precisely on the joint area reduces the risk of damage to the surrounding materials. This precise control can lead to stronger bonds and better overall product integrity, making it a preferred method in electronics, plumbing, and HVAC applications.
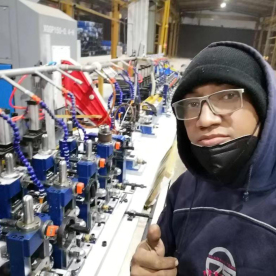
Understanding the Significance and Applications of Industrial Induction Heating Equipment in Modern Manufacturing Processes
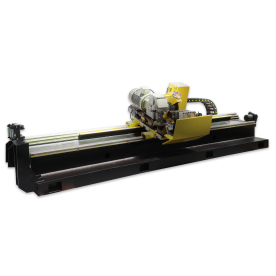
Understanding the Significance and Applications of Industrial Induction Heating Equipment in Modern Manufacturing Processes
Induction heating is also extensively used for melting metals. This process provides rapid heating and reduces contamination risks compared to traditional furnace melting methods. The compact size of induction furnaces makes them perfect for small-scale operations, as they require less space and can be operated easily. Industries like metal recycling, where materials need to be melted down and reformed, are increasingly adopting induction melting for its efficiency and environmental benefits.
The technology extends its benefits to the realm of polymer processing as well. With the advancement of induction heating equipment, industries involved in plastic and rubber production can achieve faster cycle times due to the rapid heating capabilities. Materials can be heated uniformly, allowing for better molding and consistent product quality, crucial in sectors like packaging, automotive components, and consumer goods.
From an operational perspective, industrial induction heating equipment offers numerous advantages. Firstly, it is energy-efficient, as it generates heat directly within the workpiece, minimizing energy loss and reducing costs. Secondly, the system can be automated, integrating seamlessly into modern production lines. This automation enhances productivity and reduces labor costs while ensuring consistent quality.
Moreover, induction heating systems are safer than conventional heating methods. The risk of burns or accidents is lowered since the equipment only heats the target material, leaving the surrounding environment cooler. This reduction in risk contributes to a safer working environment and can lead to lower insurance costs for manufacturers.
Additionally, the environmental impact of induction heating is less than that of traditional heating methods. Induction systems produce fewer emissions, aligning with the global push toward sustainable manufacturing practices. As industries increasingly prioritize eco-friendly solutions, adopting induction heating technology is not only a business decision but also a responsible environmental choice.

Understanding the Significance and Applications of Industrial Induction Heating Equipment in Modern Manufacturing Processes
In conclusion, industrial induction heating equipment plays a pivotal role in modern manufacturing across various sectors. Its ability to provide efficient, precise, and environmentally friendly heating solutions positions it as a key technology in an era that demands higher efficiency and sustainability. As businesses continue to innovate and adapt, those that leverage industrial induction heating will likely experience improved manufacturing processes, reduced costs, and enhanced product quality, securing their place in the competitive landscape of today’s industry.Tailor-Made Spare Parts for Tube Mills