In the rapidly evolving landscape of manufacturing, the growing demand for efficient and high-quality production has spurred innovation in various sectors. One area that has seen significant advancements is the pipe manufacturing industry. Central to this evolution is the pipe making machine, a vital piece of equipment that has transformed the way pipes are produced across diverse applications. This article delves into the innovations surrounding pipe making machines, their varied applications, and their impact on manufacturing efficiency and sustainability.
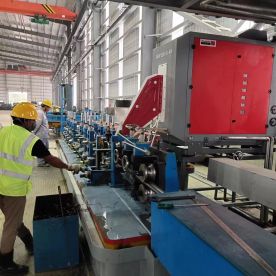
Exploring the Innovations and Applications of Pipe Making Machines in Modern Manufacturing Processes

Exploring the Innovations and Applications of Pipe Making Machines in Modern Manufacturing Processes
Pipe making machines are specialized devices designed to create pipes from various materials, including metals, polymers, and composites. These machines utilize advanced technologies to streamline the production process, enabling manufacturers to produce pipes with precise dimensions, consistent quality, and reduced waste. With the constant push for enhanced performance and durability, modern pipe making machines are equipped with sophisticated controls and automation features that allow for real-time monitoring and adjustments during the manufacturing process.
One of the primary innovations in pipe making machines is the integration of computer numerical control (CNC) systems. CNC technology allows for the automation of machine operations, significantly increasing production speeds while maintaining high precision. This capability is particularly beneficial in industries that require a large volume of pipes with specific properties, such as the oil and gas, construction, and automotive sectors. The automation also reduces the risk of human error, ensuring that the final products meet the required specifications consistently.

Exploring the Innovations and Applications of Pipe Making Machines in Modern Manufacturing Processes
The versatility of pipe making machines is another noteworthy aspect of their design. Modern machines can produce a wide variety of pipes, including seamless, welded, and composite pipes, catering to different industry requirements. For instance, seamless pipes, which are often used in high-pressure applications, are manufactured using a process that reduces weaknesses associated with welds. Conversely, welded pipes, which are more cost-effective and easier to produce, can be tailored for applications requiring lower pressure tolerances. This flexibility allows manufacturers to respond rapidly to market demands and customize products to meet specific customer needs.
Moreover, environmental concerns have necessitated innovations within pipe making machines. Many manufacturers are now focused on creating machines that minimize energy consumption and waste generation throughout the production process. For example, modern machines often incorporate eco-friendly materials and utilize energy-efficient motors, reducing their carbon footprint. Additionally, waste material generated during the pipe manufacturing process can be recycled and reintroduced into production, contributing to more sustainable manufacturing practices.
The applications of pipe making machines extend far and wide, impacting numerous industries. In the construction sector, pipes are essential for plumbing and drainage systems. Pipes produced using advanced machines are critical for ensuring safe and reliable water supply, as well as for efficient waste management. The oil and gas industry, too, relies heavily on high-quality pipes for drilling operations, transport of hydrocarbons, and safety systems. With the increasing focus on offshore drilling and exploration of unexplored areas, the demand for specialized pipe making machines capable of producing robust pipes is at an all-time high.
Additionally, in the automotive industry, pipes serve various purposes, from exhaust systems to internal fluid conveyance. As vehicles become more sophisticated and fuel-efficient, the demand for lightweight yet durable pipes continues to grow. Manufacturers are turning to composite materials that combine strength with reduced weight, necessitating the use of advanced pipe making machines that can cater to these innovative materials and designs.
In conclusion, the evolution of pipe making machines reflects broader trends in manufacturing aimed at enhancing efficiency, sustainability, and adaptability. The incorporation of technologies like CNC automation, the ability to produce various types of pipes, and a focus on environmentally friendly practices have made these machines indispensable in countless industries. As the demand for high-quality pipes continues to rise, the innovations in pipe making machines will undoubtedly play a crucial role in shaping the future of manufacturing. The ongoing investment in research and development in this area promises an exciting future for pipe production, with new technologies on the horizon set to further enhance capabilities and efficiency in the industry.Spare Parts Kit for Tube Mills