In the realm of industrial manufacturing, the production of pipes is a fundamental process, underpinning countless applications across various sectors, including construction, oil and gas, automotive, and more. The demand for high-quality pipes requires robust production lines that integrate advanced technologies. Among these technologies, a pipe mill production line equipped with sophisticated welding and cutting functions stands out as a game-changer in the industry. This article explores the features, benefits, and innovations of these integrated pipe mill production lines, demonstrating how they enhance productivity and ensure precision in pipe manufacturing.
**Understanding Pipe Mill Production Lines**
A pipe mill production line is a complex system designed for the seamless manufacturing of pipes from raw materials. Traditional pipe production techniques involved several standalone operations that could slow down production and increase costs. However, modern pipe mill production lines incorporate automation and advanced machinery, streamlining the entire process from material handling to finished product.
One of the most significant advancements in these production lines is the integration of welding and cutting functions. This innovation allows for a continuous flow of operations, reducing downtime and increasing overall efficiency.
**The Role of Welding in Pipe Mill Production Lines**
Welding is a crucial process in the production of pipes, as it ensures the integrity and strength of the final product. In a conventional setup, welding operations may require separate machines, leading to inefficiencies and challenges in quality control. With the integrated welding function in modern pipe mill production lines, manufacturers can achieve consistent quality and minimize weld-related defects.
The welding machines used in these production lines employ various techniques, such as MIG (Metal Inert Gas), TIG (Tungsten Inert Gas), and submerged arc welding, depending on the material and specifications of the pipes being produced. The choice of welding technique plays a vital role in achieving optimal joint strength and ensuring that the pipes can withstand high pressure and temperature conditions.
Moreover, advanced monitoring systems are often employed to ensure that the welding process adheres to strict quality standards. Sensors can detect inconsistencies in the welding process, allowing operators to make real-time adjustments and maintain the integrity of the pipes being produced.
**Cutting Functions for Precision and Efficiency**
In addition to welding, cutting functions are integral to the pipe mill production line. The ability to accurately cut pipes to specified lengths is essential for meeting customer demands and minimizing waste. Integrated cutting systems in modern production lines utilize precision saws and laser cutting technology, offering unparalleled accuracy in pipe dimensions.
Laser cutting, in particular, has gained popularity due to its efficiency and precision. This method uses a focused laser beam to cut through materials, resulting in clean edges and reducing the need for secondary processing. The integration of cutting functions means that pipes can be fabricated to size in a single pass, further enhancing the production line’s efficiency.
**Advantages of an Integrated Pipe Mill Production Line**
1. **Increased Efficiency**: By combining welding and cutting functions into a singular production line, manufacturers can achieve a streamlined workflow. This integrated approach minimizes the time spent on transitions between processes, reducing lead times and increasing output.
2. **Enhanced Quality Control**: With all operations occurring within a unified system, quality control becomes more manageable. Operators can monitor every aspect of the production process, making it easier to identify and rectify any potential issues before they escalate.
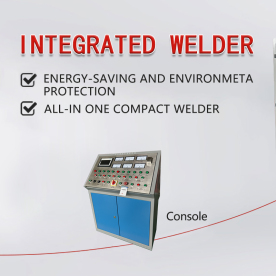
Revolutionizing Pipe Fabrication: The Advanced Pipe Mill Production Line with Integrated Welding and Cutting Functions for Enhanced Efficiency and Precision
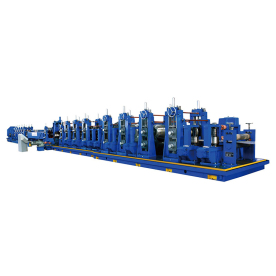
Revolutionizing Pipe Fabrication: The Advanced Pipe Mill Production Line with Integrated Welding and Cutting Functions for Enhanced Efficiency and Precision

Revolutionizing Pipe Fabrication: The Advanced Pipe Mill Production Line with Integrated Welding and Cutting Functions for Enhanced Efficiency and Precision
3. **Cost-Effectiveness**: While the initial investment in advanced machinery may be substantial, the long-term savings from increased efficiency, reduced waste, and improved quality often outweigh the costs. Manufacturers can deliver higher-quality products at competitive prices, bolstering their market position.
4. **Flexibility and Customization**: Many modern pipe mill production lines offer customizable settings that allow manufacturers to produce pipes of various sizes and specifications. This adaptability is vital in responding to changing market demands and customer preferences.
**Conclusion**
The integration of welding and cutting functions into pipe mill production lines represents a significant leap forward in the manufacturing process. With enhanced efficiency, quality control, and cost-effectiveness, these advanced systems are poised to meet the growing demands of modern industries. As technology continues to evolve, we can expect even greater innovations in pipe manufacturing, driving further improvements in productivity and precision. The future of pipe production is undoubtedly bright, powered by the sophisticated and integrated solutions that modern pipe mill production lines offer.Energy-saving and Environmental-friendly All-in-one Welder