****
Automatic induction heating equipment has revolutionized the way industries perform heating processes, providing efficient solutions that enhance not only productivity but also safety and energy consumption. This technique utilizes electromagnetic induction to generate heat directly within the material, making it a preferable choice for various applications across diverse sectors. In this article, we’ll explore the fundamental working principle of automatic induction heating equipment, its advantages, and the numerous applications that are driving its adoption in modern industries.
The Principle of Induction Heating
Induction heating is based on the principle of electromagnetic induction. When an alternating current flows through a coil, it creates a magnetic field, which in turn induces an electric current in nearby conductive materials. This induced current produces heat due to the material’s electrical resistance. The result is a highly efficient heating process that can quickly raise the temperature of metals and other conductive materials without needing to heat the surrounding medium.
Automatic induction heating equipment is designed to operate autonomously, utilizing advanced controls to maintain precise temperature settings and heating times. This automation enables manufacturers to optimize processes, reduce human error, and improve the overall quality of their products.
Advantages of Automatic Induction Heating Equipment
1. **Efficiency**: One of the most significant advantages of automatic induction heating equipment is its efficiency. Traditional heating methods often waste energy by heating the surrounding environment or require long preheating times. In contrast, induction heating focuses energy directly on the workpiece, minimizing energy loss and reducing heating times significantly.
2. **Precision and Control**: The ability to control the heating process with great precision is another benefit of automatic induction heating systems. These systems come equipped with sophisticated temperature and process monitoring, allowing for repeatable results in critical heating applications. This is particularly vital in industries where the properties of materials must be controlled tightly during processing.
3. **Safety**: Automatic induction heating equipment enhances safety in the workplace. Since the heating occurs directly within the metal, there is less risk of exposure to open flames or hot surfaces, which can lead to burns and other injuries. Moreover, many modern systems include safety features that help prevent overheating, ensuring secure operating conditions.
4. **Versatility**: Induction heating equipment is incredibly versatile and can be used for different applications such as hardening, annealing, brazing, forging, and melting. This adaptability allows manufacturers to streamline operations, utilizing a single type of equipment for multiple heating needs.
5. **Environmental Benefits**: With growing emphasis on sustainability, automatic induction heating equipment offers environmental advantages as well. As induction systems typically consume less energy and produce fewer emissions compared to traditional heating methods, they contribute to a lower carbon footprint, making them an eco-friendly option for industries.
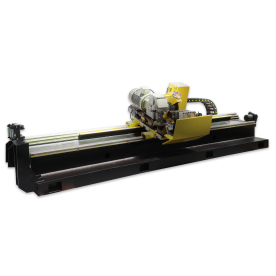
Understanding the Advantages and Applications of Automatic Induction Heating Equipment in Modern Industries
Applications Across Industries
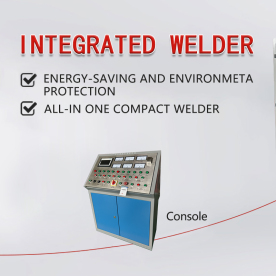
Understanding the Advantages and Applications of Automatic Induction Heating Equipment in Modern Industries
The applications of automatic induction heating equipment are vast and varied, impacting several sectors, including:
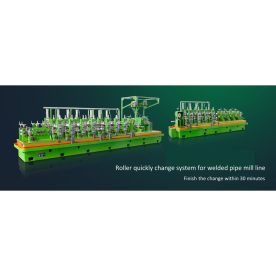
Understanding the Advantages and Applications of Automatic Induction Heating Equipment in Modern Industries
– **Automotive**: In the automotive industry, induction heating is widely used for processes such as hardening shafts, crankshafts, and gears. The precision and speed of induction heating help ensure that components meet strict performance requirements.
– **Manufacturing**: Various manufacturing processes utilize induction heating for assembling parts, such as in the production of metal parts and pipes. By using induction heating, manufacturers can reduce production cycles, thus increasing overall efficiency and output.
– **Electronics**: The electronics sector applies induction heating for processes like soldering and metal joining. The controlled heating capabilities allow for high-quality results, essential in guaranteeing the reliability and performance of electronic devices.
– **Jewelry Making**: In the jewelry industry, automatic induction heating equipment is used for soldering, casting, and melting metals. The quick and precise heating reduces the risk of damaging delicate pieces, allowing artisans to create intricate designs without compromising quality.
– **Aerospace**: In aerospace, precision heating can be critical. Induction heating equipment is employed for metal treatment and surface hardening of components subject to high stress, thereby enhancing performance and safety.
Conclusion
As industries continue evolving and demand for efficiency grows, automatic induction heating equipment stands out as a transformative solution. Its energy-efficient design, safety features, and capability for precision make it an essential tool across various sectors, enhancing productivity and maintaining high standards of quality. Whether in automotive production, electronics assembly, or artisan jewelry making, the role of automatic induction heating equipment is more crucial than ever, proving that the future of heating technology is not just about heat but about smart heat.Automatic Flying Saw Machine