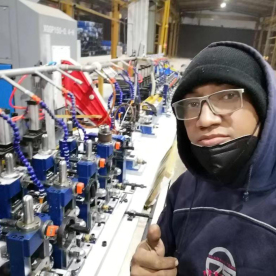
Revolutionizing Manufacturing: The Impact of Energy-efficient Pipe Mill Production Line on Cost Reduction and Sustainability in the Pipe Industry
In an era where sustainability and efficiency have become paramount in manufacturing, the introduction of energy-efficient pipe mill production lines has revolutionized the pipe manufacturing industry. With the increased demand for high-quality pipes in sectors such as construction, oil and gas, and water supply, manufacturers face the dual challenge of maintaining quality while reducing production costs. This is where energy-efficient technologies come into play, not only enhancing productivity but also contributing significantly to environmental conservation.
Energy-efficient pipe mill production lines integrate advanced technologies that minimize energy consumption and waste generation during the manufacturing process. Traditional pipe production methods often involve high energy use and substantial waste, both of which contribute to higher operational costs and increased carbon footprints. The advent of energy-efficient solutions offers an alternative that aligns with current environmental standards and economic demands.
One of the key features of energy-efficient pipe mill production lines is the use of advanced machinery and automation. Modern pipe mills are equipped with high-speed rolling mills, optimized heating systems, and precision cutting tools that reduce energy consumption significantly. For instance, the use of induction heating technology allows for more uniform heating of materials, resulting in reduced energy usage compared to conventional methods. Moreover, automation helps in synchronizing various processes, reducing downtime, and increasing overall productivity.
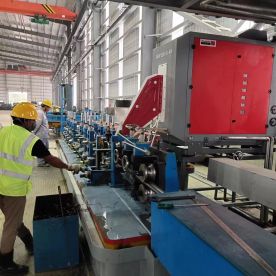
Revolutionizing Manufacturing: The Impact of Energy-efficient Pipe Mill Production Line on Cost Reduction and Sustainability in the Pipe Industry
Another crucial aspect is the implementation of energy management systems that monitor and control energy use in real-time. These systems provide valuable data insights, allowing manufacturers to identify inefficiencies and optimize power consumption across the production line. By understanding patterns of energy use, decisions can be made to adjust processes and machinery settings, leading to further reductions in energy costs.
The transition to energy-efficient production lines does not purely focus on energy consumption; it also emphasizes material efficiency. Advanced manufacturing techniques, including precision welding and computer numerical control (CNC) machining, lead to reduced scrap rates and material wastage during the production process. By maximizing raw material usage and minimizing waste, manufacturers can significantly decrease costs associated with inputs while enhancing overall sustainability.
Cost reduction through energy efficiency in pipe production also extends to long-term financial savings. Although the initial investment in upgrading to an energy-efficient pipe mill production line may be substantial, the cumulative savings on energy bills, maintenance costs, and waste disposal fees can result in a swift return on investment. Furthermore, companies that adopt green technologies often find themselves at a competitive advantage, as environmentally-conscious consumers and businesses increasingly favor sustainable practices.
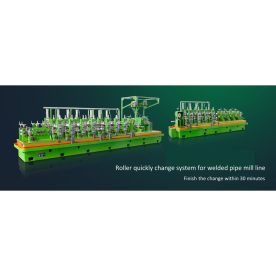
Revolutionizing Manufacturing: The Impact of Energy-efficient Pipe Mill Production Line on Cost Reduction and Sustainability in the Pipe Industry
The environmental benefits of energy-efficient pipe mill production lines are likewise significant. By reducing energy consumption, these systems contribute to lower greenhouse gas emissions, aiding the global effort to combat climate change. Sustainable practices within the manufacturing sector can lead to a more favorable public image and increased brand loyalty. Consumers today are increasingly aware of the origins and production processes of the products they buy and are more likely to support companies that demonstrate a commitment to sustainability.
Moreover, energy-efficient production lines can play an essential role in eco-friendly certifications and compliance with regulations. As governments worldwide impose stricter environmental guidelines, companies that invest in sustainable practices position themselves as leaders in compliance and responsibility. This proactive approach not only mitigates risk but can also open doors to new business opportunities and contracts with government and private projects, which increasingly prioritize sustainability in their procurement standards.
In conclusion, the deployment of energy-efficient pipe mill production lines represents a pivotal development in the manufacturing landscape. By embracing technologies that enhance efficiency, reduce costs, and promote sustainability, manufacturers can not only survive today’s economic challenges but thrive while contributing positively to the environment. As the pipe industry navigates an increasingly competitive and eco-aware market, the importance of adopting energy-efficient practices will only grow, making the transition to modern production lines not just beneficial, but essential for long-term success.Precision ERW tube mill machinery