****
In today’s rapidly evolving industrial landscape, the demand for advanced welding technologies continues to rise. Among these innovations, solid state HF welders with remote control systems have emerged as a game-changer in various manufacturing processes. These versatile machines not only provide superior welding quality but also enhance operational efficiency and worker safety in a multitude of applications. In this article, we will dive deep into the key features, benefits, and applications of solid state HF welders equipped with remote control interfaces.
**Understanding Solid State HF Welding Technology**
High-frequency (HF) welding is a process commonly used to join thermoplastic materials through the application of high-frequency electromagnetic fields. Solid state HF welders utilize modern semiconductor technology to generate the necessary frequencies for achieving effective welds. Unlike traditional tube-based systems, solid state devices offer greater efficiency, reduced maintenance needs, and increased reliability.
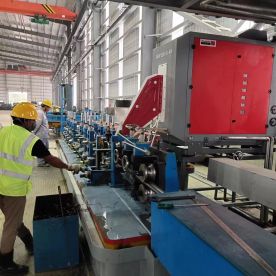
Exploring the Advantages of Solid State HF Welders with Remote Control for Enhanced Efficiency in Industrial Applications
With the ability to control power levels and frequencies with precision, solid state HF welders provide improved thermal management during the welding process. This translates to better control over the weld quality, minimizing defects and enhancing the strength of the final product.
**The Role of Remote Control Systems**
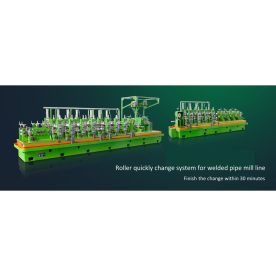
Exploring the Advantages of Solid State HF Welders with Remote Control for Enhanced Efficiency in Industrial Applications
One of the standout features of modern solid state HF welders is the integration of remote control systems. This innovation allows operators to monitor and adjust welding parameters from a distance, thus improving workflow and reducing the need for constant physical presence at the machine. Remote control interfaces can be accessed through various devices such as tablets, laptops, or specific custom remote units, making the process more versatile and adaptable to different working environments.
The incorporation of remote control capabilities brings several advantages, including:
1. **Increased Safety and Ergonomics**: By allowing operators to adjust settings from a safe distance, remote control reduces the risk of accidents associated with manual adjustments near high-frequency equipment. This aspect is crucial in environments where employees might be exposed to hazardous conditions or moving machinery.
2. **Real-Time Monitoring**: The ability to monitor welding processes in real-time from a remote location enhances oversight and communication among team members. Operators can receive instant alerts for any irregularities during production, enabling timely intervention that can significantly reduce downtime and material waste.
3. **Flexibility and Convenience**: Remote control features provide operators with the freedom to move around the workshop or facility while monitoring the welding process. This flexibility can lead to improved productivity as operators can attend to multiple tasks simultaneously without being tethered to the welder.

Exploring the Advantages of Solid State HF Welders with Remote Control for Enhanced Efficiency in Industrial Applications
4. **Pre-Programmed Settings**: Many solid state HF welders with remote control functionality come equipped with the ability to store pre-programmed settings for specific welding jobs. This allows for quicker changeovers between projects, maintaining consistency in production without having to reconfigure settings each time.
**Applications Across Industries**
Solid state HF welders with remote control systems are utilized across a wide range of industries, including packaging, automotive, textiles, and electrical components. In packaging, these welders are instrumental in securely sealing plastic bags or films, while in automotive production, they are crucial for creating reliable connections in wiring harnesses and other components.
Textile companies also benefit from these welders, using them for seams and hems in synthetic fabrics, while manufacturers of electrical components rely on solid state HF technology to produce durable and efficient connections in electronic devices.
**Conclusion**
The advent of solid state HF welders with remote control capabilities marks a significant advancement in welding technology, offering numerous benefits over traditional systems. From enhanced safety and operational efficiency to real-time monitoring and flexibility in production processes, these machines represent an investment that can yield substantial returns in terms of quality and productivity.
As industries continue to embrace automation and smart technology, it is expected that solid state HF welders with remote control functionality will become even more prevalent, driving innovation and improving manufacturing outcomes across various sectors. By adapting to these modern solutions, businesses can stay competitive and meet the ever-growing demands of the marketplace.Annealing Machine Replacement Parts