****
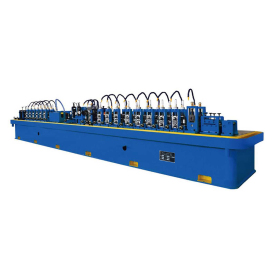
Customized Pipe Mill Production Line Solutions: Tailoring Manufacturing Processes to Meet Diverse Industry Demands
In today’s highly competitive industrial landscape, manufacturers are continually seeking ways to optimize their processes, enhance product quality, and reduce operational costs. One of the most effective strategies to achieve these goals is the implementation of customized pipe mill production line solutions. These tailored approaches not only improve efficiency but also allow manufacturers to cater to the specific needs of their clients, ensuring they remain ahead in their respective markets.
**Understanding Customized Pipe Mill Production Lines**
At its core, a pipe mill production line is a series of interconnected processes that enable the manufacturing of pipes, which are essential components in a myriad of industries, including construction, automotive, oil and gas, and plumbing. However, the requirements for pipe production can vary significantly based on the materials used, dimensions required, and end-use applications. Customized production lines are designed to address these variations, providing flexibility and tailor-made solutions that standard production lines cannot offer.
A customized pipe mill production line typically involves several stages, including material preparation, forming, welding, and finishing. Each stage can be modified or optimized based on the specific requirements of the production process, ensuring a streamlined operation that maximizes efficiency.
**Key Components of Customized Solutions**
1. **Material Selection and Preparation**: The type of raw materials used in pipe production directly affects the quality and performance of the final product. Customized solutions can include advanced material handling systems that ensure the correct materials are used in precise quantities, minimizing waste and ensuring optimal characteristics for the pipes being produced.
2. **Forming Technology**: The forming process is crucial in determining the shape and dimensions of the pipes. Custom solutions may involve specialized machinery capable of producing a diverse range of pipe diameters and wall thicknesses. This flexibility is particularly beneficial for manufacturers looking to expand their product offerings or those catering to niche markets.
3. **Welding Techniques**: Welding is another critical component that can be tailored in a customized pipe mill production line. Different welding methods, such as high-frequency induction welding, submerged arc welding, or laser welding, can be employed based on the material type and intended application. These methods can affect the overall strength, durability, and corrosion resistance of the pipes, making it essential to select the right welding technique for each production scenario.
4. **Quality Control Systems**: Quality assurance is central to meeting industry standards and customer expectations. Advanced monitoring and quality control systems can be integrated into customized solutions, allowing for real-time data analysis and process adjustments. This proactive approach minimizes defects and rework, ultimately saving time and resources.
5. **Automation and Control**: With the rise of Industry 4.0, automation has become a central element in modern manufacturing. Customized pipe mill production lines can incorporate automated controls and robotics to enhance operational efficiency and reduce human error. These technologies facilitate seamless interactions between processes, optimizing production flow and maximizing output.
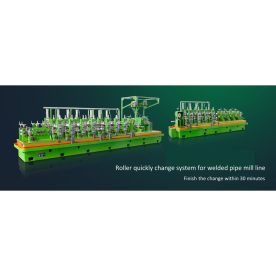
Customized Pipe Mill Production Line Solutions: Tailoring Manufacturing Processes to Meet Diverse Industry Demands
**Benefits of Customized Pipe Mill Production Lines**
1. **Enhanced Flexibility**: As market demands shift, manufacturers need to adapt quickly. Customized production lines provide this flexibility, allowing for rapid reconfiguration and scalability, enabling businesses to respond swiftly to changes in consumer needs.

Customized Pipe Mill Production Line Solutions: Tailoring Manufacturing Processes to Meet Diverse Industry Demands
2. **Improved Product Quality**: Tailored solutions ensure that every aspect of the production process is optimized, leading to higher quality pipes that meet or exceed industry standards. This focus on quality enhances brand reputation and customer satisfaction.
3. **Cost Efficiency**: By minimizing waste and maximizing productivity, customized pipe mill production lines can lead to significant cost savings. Efficient operations reduce labor costs, energy consumption, and raw material waste, improving overall profitability.
4. **Competitive Advantage**: Businesses that invest in customized solutions position themselves as leaders in their respective markets. They can offer unique products and services that stand out from competitors, attracting a broader customer base.
**Conclusion**
Customized pipe mill production line solutions represent a forward-thinking approach in the manufacturing sector. By tailoring production processes to meet specific industry demands, businesses can enhance efficiency, improve product quality, and achieve significant cost savings. As the industrial landscape continues to evolve, companies that prioritize customization will be well-equipped to navigate future challenges and capitalize on new opportunities, thereby securing their competitive edge in the market.Tube making machine for industrial applications