****
In the ever-evolving landscape of manufacturing, achieving efficiency and precision is paramount. One of the innovations that have dramatically transformed industrial heating processes is automatic induction heating equipment. This technology utilizes electromagnetic induction to heat conductive materials, offering numerous advantages over traditional heating methods. In this article, we delve into the features, benefits, applications, and future of automatic induction heating equipment, highlighting its significance in modern production environments.
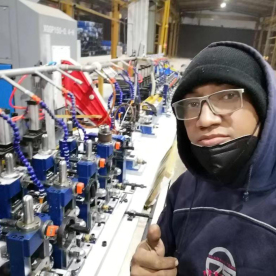
Exploring the Efficiency and Benefits of Automatic Induction Heating Equipment in Modern Manufacturing Processes
Understanding Automatic Induction Heating
Induction heating is a process that heats electrically conductive materials through electromagnetic induction. When an alternating current passes through a coil, it generates a magnetic field that induces electrical currents within the material, causing it to heat up. Automatic induction heating equipment typically includes a power supply, induction coils, and control systems that adjust heating parameters based on the application’s specific requirements.
Key Features of Automatic Induction Heating Equipment
1. **Precision Control**: One of the most notable features of automatic induction heating equipment is its ability to provide precise temperature control. Manufacturers can set specific parameters, ensuring that materials reach desired temperatures with minimal deviation. This level of control is crucial in applications requiring consistent results.
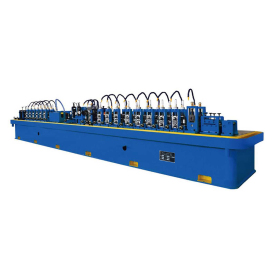
Exploring the Efficiency and Benefits of Automatic Induction Heating Equipment in Modern Manufacturing Processes
2. **Energy Efficiency**: Compared to traditional heating methods, induction heating is highly energy-efficient. The process focuses heat directly where it’s needed, reducing heat loss and lowering energy consumption. This not only minimizes operational costs but also contributes to environmentally sustainable practices.
3. **Speed and Productivity**: Automatic induction heating equipment can significantly reduce processing times. The quick heating response allows for faster production cycles, which is particularly advantageous in high-volume manufacturing environments. This speed translates into increased productivity and the ability to meet tight deadlines.
4. **Safety Features**: Modern automatic induction heating systems come equipped with various safety features that protect operators and equipment. These include over-temperature protection, automatic shut-off mechanisms, and sensors that monitor the heating process, ensuring safe operation at all times.
Benefits of Automatic Induction Heating Equipment
The adoption of automatic induction heating equipment offers several benefits to manufacturers, enhancing both operational efficiency and product quality:
1. **Reduced Production Costs**: The energy efficiency of induction heating, combined with its fast processing capabilities, leads to reduced production costs. Manufacturers can save on energy bills and equipment wear and tear, ultimately improving profit margins.
2. **Improved Quality Control**: The precision offered by automatic induction heating means that manufacturers can achieve consistent heating of materials, resulting in improved quality control. This is especially important in industries where material properties are critical, such as aerospace and automotive.
3. **Diverse Applications**: Automatic induction heating equipment is versatile and can be used in various applications, including metal hardening, brazing, soldering, and tempering. Its adaptability makes it suitable for a wide range of industries, from manufacturing to metallurgy.
4. **Reduction of Emissions**: As industries increasingly focus on sustainability, the reduced energy consumption associated with induction heating helps lower greenhouse gas emissions. By utilizing this technology, companies can align their processes with environmental regulations and corporate sustainability goals.
Applications of Automatic Induction Heating Equipment
Automatic induction heating equipment has a wide range of applications across various industries:
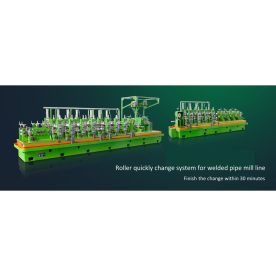
Exploring the Efficiency and Benefits of Automatic Induction Heating Equipment in Modern Manufacturing Processes
– **Automotive Industry**: Used for hardening steel components, induction heating enhances the durability and performance of critical automotive parts. – **Aerospace Sector**: In aerospace manufacturing, it plays a crucial role in processes like heat treating, which is essential for ensuring material integrity. – **Metal Fabrication**: Induction heating is employed for tasks such as brazing and soldering, providing strong joints without the need for excessive heat. – **Electronics**: In electronics manufacturing, induction heating is used for soldering components and other applications where precision is key.
The Future of Automatic Induction Heating Equipment
As industries continue to seek ways to optimize efficiency and sustainability, the role of automatic induction heating equipment is expected to grow. Continued advancements in technology, such as the integration of IoT and AI, will enhance the capabilities of these systems, enabling even more precise control and data-driven decision-making.
Moreover, as manufacturers become increasingly aware of their environmental impact, the demand for energy-efficient and cost-effective heating solutions will drive the adoption of automatic induction heating equipment. Investing in this technology not only positions companies for improved operational efficiency but also helps them meet regulatory requirements and address customer preferences for sustainable practices.
Conclusion
In conclusion, automatic induction heating equipment stands at the forefront of modern manufacturing, offering unmatched efficiency, precision, and versatility. Its ability to reduce costs while improving product quality makes it a vital component in the manufacturing processes of today and tomorrow. As industries continue to innovate and evolve, the role of induction heating will undoubtedly expand, paving the way for a more efficient and sustainable future in manufacturing.High frequency welder machine