****
High frequency welder machines have become increasingly prominent in various sectors, providing efficient and reliable solutions for metal joining and fabrication. With their unique capability to utilize high-frequency electrical currents, these machines ensure strong, precise, and high-quality welds, making them an essential tool in many manufacturing processes. This article will dive into the intricacies of high frequency welder machines, exploring their applications, benefits, and key features that set them apart from conventional welding equipment.
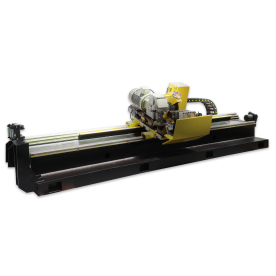
Understanding High Frequency Welder Machines: Their Applications, Benefits, and Key Features in Modern Industries
What is a High Frequency Welder Machine?
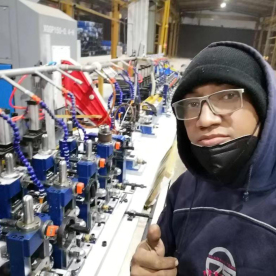
Understanding High Frequency Welder Machines: Their Applications, Benefits, and Key Features in Modern Industries
At its core, a high frequency welder machine uses high-frequency electrical energy to create heat at the welding point. This process typically involves the use of induction heating or dielectric heating, depending on the materials being welded. The machine generates a high-frequency electromagnetic field that induces rapid heating in the workpieces, allowing them to fuse together under pressure without significant melting of the base materials. This innovative approach allows for welds that are not only strong but also retain the integrity of the parent materials.
Applications of High Frequency Welder Machines
High frequency welding machines are versatile and utilized in various industries, including:
1. **Textile and Fabric Manufacturing**: One of the most significant applications of high frequency welders is in the production of textiles, where they are used to bond materials like PVC, PU, and other synthetic fabrics without stitching. This process is vital in creating waterproof seams in products such as outdoor gear and inflatable items. 2. **Automotive Industry**: In the automotive sector, these machines are essential for welding components such as wires, hoses, and even certain body panels. Their ability to deliver fast, consistent welding makes them invaluable in high-volume production settings.
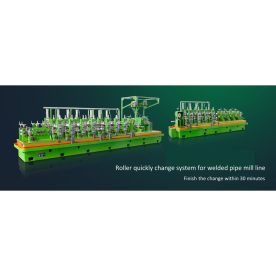
Understanding High Frequency Welder Machines: Their Applications, Benefits, and Key Features in Modern Industries
3. **Packaging Industry**: High frequency welding is commonly utilized in the production of plastic packaging, where it’s crucial to seal materials efficiently to ensure product integrity and freshness.
4. **Medical Devices**: The medical industry employs high frequency welders for assembling equipment and devices that need to maintain strict hygienic standards. The precision and sterility involved in high frequency welding make it a go-to choice for manufacturers.
Key Benefits of High Frequency Welding
1. **Speed and Efficiency**: One of the most significant advantages of high frequency welder machines is their ability to produce welds quickly. The process can be completed in a matter of seconds, allowing for high throughput and optimized production times.
2. **Quality Control**: High frequency welding results in clean and precise welds, which reduces the chances of defects. This is particularly important in industries where quality is paramount, ultimately leading to lower rejection rates and better-quality products.
3. **Cost-Effective**: By reducing the amount of time and labor needed for welding, high frequency welders can help lower overall manufacturing costs. Furthermore, the strong bonds created by these welds enhance product durability and longevity.
4. **Minimal Material Distortion**: Traditional welding methods can lead to warping or distortions due to excessive heat. In contrast, high frequency welding minimizes this issue since the materials involved are heated quickly and uniformly, ensuring that the overall structure remains intact.
Features of High Frequency Welder Machines
High frequency welder machines come with various features designed to enhance operational efficiency:
– **Programmable Controls**: Many modern high frequency welders have programmable interfaces that allow operators to set parameters for different materials and thicknesses, ensuring consistent weld quality. – **Adjustable Frequency Settings**: Different materials may require variations in frequency settings. Advanced machines allow users to adjust the frequency to optimize their specific welding needs.
– **Safety Mechanisms**: High frequency welders are equipped with safety features such as automatic shut-off and protective enclosures to prevent accidents during operation.
– **Portability**: Many high frequency welding machines are designed for ease of transport, allowing for use in multiple locations or job sites as needed.
Conclusion
High frequency welder machines are revolutionizing welding processes across numerous industries by providing faster, higher quality, and more cost-effective solutions. As technology continues to evolve, these machines will likely become even more integral to manufacturing, meeting the demands of modern production environments. For businesses looking to enhance their welding capabilities, investing in a high frequency welder is certainly a move towards greater efficiency and product quality.Tailor-Made Spare Parts for Tube Mills