In the rapidly evolving world of manufacturing, precision and quality play pivotal roles in meeting the demands of modern industries. One of the remarkable innovations in this realm is the high-precision tube making machine, a sophisticated piece of equipment designed to produce tubes with exceptional accuracy and uniformity. This article delves into the workings of high-precision tube making machines, their advantages, applications across various sectors, and their impact on the future of manufacturing.
High-precision tube making machines are engineered to create tubes and pipes from a variety of materials, including metals, plastics, and composites. These machines utilize advanced technologies such as CNC (computer numerical control), laser cutting, and automated forming techniques to ensure that the final products meet strict dimensional tolerances and quality standards. Unlike traditional tube fabrication methods, high-precision machines can achieve intricate designs and specifications, enabling manufacturers to cater to a wider range of customer requirements.
One of the primary advantages of using high-precision tube making machines is the significant reduction in production time. With the incorporation of automation and advanced software systems, these machines can operate continuously with minimal human intervention, ensuring a consistent output while reducing the likelihood of human error. This efficiency not only cuts down on lead times but also lowers production costs, making businesses more competitive in the market.
Furthermore, high-precision tube making machines offer unparalleled flexibility in design. Manufacturers can easily switch between different tube sizes, materials, and shapes without extensive downtime or the need for retooling. This adaptability is particularly beneficial for industries that require customized or small-batch production, such as automotive, aerospace, medical, and construction sectors. By allowing for quick adjustments, these machines empower manufacturers to be more responsive to changes in market demands and customer preferences.
The precise production capabilities of these machines also contribute to enhanced product quality. High-precision tube making machines are equipped with advanced monitoring systems that continuously assess product dimensions throughout the manufacturing process. This real-time feedback enables manufacturers to identify and rectify any discrepancies immediately, ensuring that each tube adheres to the specified criteria. As a result, companies can deliver products that significantly reduce the risk of defects and failures in critical applications.
Applications of high-precision tube making machines span various industries. In the aerospace sector, for example, lightweight and high-strength tubes are essential for aircraft structures and components. These tubes must meet strict safety and performance standards, making the precision provided by high-precision machines critical. Similarly, in the automotive industry, high-quality tubes are used in exhaust systems, fuel lines, and structural components. The need for durability and performance in these applications makes high-precision tube making machines indispensable.
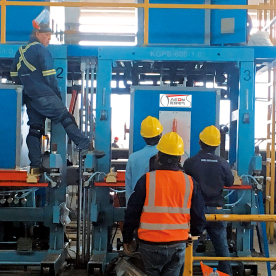
Innovative Advances in Manufacturing: Exploring the Benefits and Applications of High-Precision Tube Making Machines in Various Industries
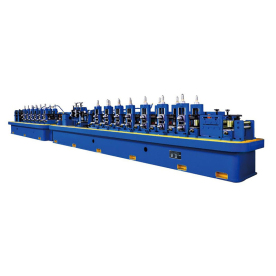
Innovative Advances in Manufacturing: Exploring the Benefits and Applications of High-Precision Tube Making Machines in Various Industries
In the medical field, both the quality and precision of tubing can directly impact patient safety. High-precision tube making machines enable the production of medical-grade tubes used in devices such as catheters and IV lines that meet stringent regulatory requirements. Their ability to produce precise sizes and fittings ensures that these critical devices function as intended without complications.

Innovative Advances in Manufacturing: Exploring the Benefits and Applications of High-Precision Tube Making Machines in Various Industries
As technology continues to advance, the future of high-precision tube making machines looks promising. Industries are increasingly adopting smart manufacturing practices, which integrate the Internet of Things (IoT), artificial intelligence (AI), and machine learning into production processes. These innovations can further enhance the capabilities of tube making machines, allowing for predictive maintenance, optimized production schedules, and better overall efficiency.
In conclusion, high-precision tube making machines represent a significant leap forward in the manufacturing sector. Their ability to produce custom tubes with exceptional precision at reduced costs has profound implications across various industries. As technology continues to evolve, the potential for high-precision tube making machines to transform manufacturing practices and enhance product quality will only increase, paving the way for a new era of innovation and efficiency. Businesses that embrace these advancements will undoubtedly find themselves at the forefront of their respective markets, ready to meet the challenges and opportunities that lie ahead.Reliable Annealing Machine Replacement Components