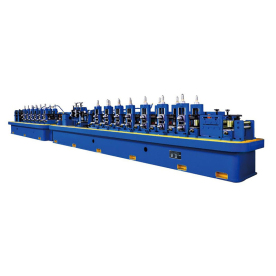
Revolutionizing Metalworking: The Invaluable Role of Precision Induction Heating Equipment in Modern Manufacturing Processes
In the realm of modern manufacturing, the integration of advanced technologies has significantly transformed traditional metalworking processes. One such technological advancement that has garnered attention across various industries is precision induction heating equipment. This innovative apparatus is changing the way metals are heated for forging, hardening, and other essential manufacturing processes. By harnessing the power of electromagnetic induction, these systems provide efficiency, precision, and reliability, making them a game changer in the metalworking landscape.
At the core of precision induction heating technology is the principle of electromagnetic induction, discovered by Michael Faraday in the early 19th century. This principle allows for the direct heating of metal objects through electromagnetic fields, eliminating the need for a direct flame or heating devices that rely on gas or electrical resistance. Instead, induction heating utilizes a coil that generates an alternating magnetic field. When a conductive material, such as iron or steel, enters this field, eddy currents are induced within the material, generating heat internally. This method of heating is not only faster but also provides precise control over the heating process.
One of the most significant advantages of precision induction heating equipment is its efficiency. Traditional heating methods often result in heat loss due to radiation and convection, leading to higher energy consumption and longer heating times. Induction heating, on the other hand, is a highly efficient process, often achieving temperatures of up to 1600°C in a matter of seconds. This rapid heating capability results in shorter cycle times, allowing manufacturers to produce more parts in less time and improve overall productivity.
In addition to efficiency, precision induction heating provides remarkable control over heating parameters. Operators can set precise temperature levels and control the heating profiles to achieve desired metallurgical properties. This is particularly crucial in applications like hardening, where improper heating can result in undesirable material properties or even structural failure. With the use of advanced induction heating equipment, manufacturers can achieve consistent and repeatable results, ensuring quality and performance across batches.
The versatility of precision induction heating equipment further enhances its attractiveness in various applications. Industries such as automotive, aerospace, and tool manufacturing benefit from induction heating for processes such as annealing, tempering, and surface hardening. In the automotive sector, for example, induction heating is used to harden crankshafts and camshafts, improving wear resistance and extending component life. Similarly, in aerospace applications, induction heating is crucial for treating components that demand high-performance specifications, ensuring safety and reliability in critical applications.
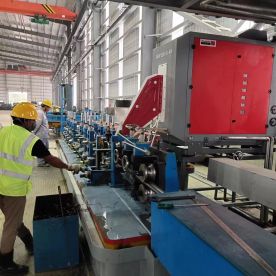
Revolutionizing Metalworking: The Invaluable Role of Precision Induction Heating Equipment in Modern Manufacturing Processes

Revolutionizing Metalworking: The Invaluable Role of Precision Induction Heating Equipment in Modern Manufacturing Processes
Moreover, the environmental impact of precision induction heating equipment cannot be overlooked. Traditional heating methods often rely on fossil fuels, leading to higher carbon emissions and energy waste. Induction heating, being an electrical process, can be powered by renewable energy sources, contributing to a reduction in the overall carbon footprint of manufacturing operations. This alignment with sustainability goals is increasingly important as industries strive to meet regulatory standards and societal expectations for greener practices.
Implementing precision induction heating equipment does come with an initial investment cost, which may deter some manufacturers. However, the long-term benefits outweigh these upfront costs. The energy savings, reduced cycle times, and improved product quality can lead to substantial financial returns over time. Additionally, many manufacturers find that the reduced labor requirements and lower reject rates further enhance cost-effectiveness.
In conclusion, precision induction heating equipment is setting new standards in the metalworking industry, offering a unique blend of efficiency, precision, and versatility. As manufacturers strive to remain competitive in an increasingly demanding marketplace, embracing this technology can give them a distinct advantage. With its capacity for rapid heating, excellent control over processes, and positive environmental impact, precision induction heating is not just a technological advancement; it is a vital component of the future of manufacturing. As industries evolve and adopt more sophisticated production methods, precision induction heating will undoubtedly continue to play a central role in redefining possibilities within the sector.Customized HSS Cutting Blade