In the ever-evolving landscape of metal processing and fabrication, the introduction of advanced technologies has played a crucial role in enhancing productivity and precision. One such innovation is the All-in-One High Frequency Welder for Metal Processing, which has cemented its place as an invaluable tool for professionals in the industry. This sophisticated equipment not only streamlines welding operations but also significantly improves the quality and durability of welds, making it a pivotal asset in various applications.
High frequency welding, a technique that utilizes electromagnetic induction to create heat, eliminates the need for traditional methods that require significant manual intervention and time. With the all-in-one high frequency welder, manufacturers can achieve consistent and high-quality welds across a range of metal types, including steel, aluminum, and copper. The ability to work with multiple materials makes this welder an incredibly versatile option for any fabrication shop or manufacturing plant.
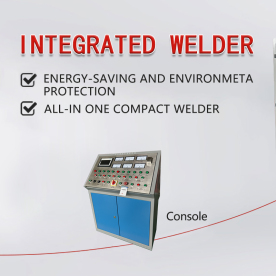
Revolutionizing Metal Fabrication: The All-in-One High Frequency Welder for Metal Processing Offers Unmatched Efficiency and Versatility
One of the most compelling features of the All-in-One High Frequency Welder is its compact design, which allows for ease of use in tight spaces without sacrificing power or performance. Traditionally, welding equipment has been cumbersome, requiring extensive layout planning and large workspaces. The all-in-one model, however, integrates various functions, such as welding, cutting, and surface treatment, into a single unit, drastically reducing the need for multiple machines and freeing up valuable floor space.
The advanced technology embedded in modern high frequency welders allows for precise control over welding parameters, including time, frequency, and pressure. This capability is crucial because it ensures that the welding process is tailored to the specific metal being used, which translates to reduced material waste and increased efficiency. Furthermore, the welder’s automated features help in minimizing human error, ensuring that each weld meets strict quality standards without the need for extensive rework.
Safety is a paramount concern in any welding operation. The All-in-One High Frequency Welder incorporates several safety mechanisms designed to protect both the operator and the equipment. These include overload protection, cooling system safeguards, and easy-to-access emergency shut-off options. By minimizing risks associated with high voltage and heat production, operators can focus on their work with confidence, ultimately contributing to a safer working environment.
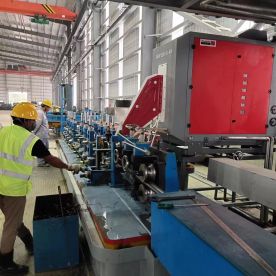
Revolutionizing Metal Fabrication: The All-in-One High Frequency Welder for Metal Processing Offers Unmatched Efficiency and Versatility
Another advantage of using an all-in-one high frequency welder is the speed with which it operates. With traditional welding methods, the setup and execution can be time-consuming, leading to bottlenecks in production. The efficiency of high frequency welding allows for faster processing times, significantly enhancing throughput. This is particularly beneficial for industries that demand high-volume production and rapid turnaround times, such as automotive and aerospace.
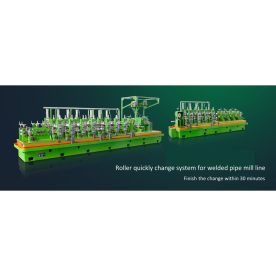
Revolutionizing Metal Fabrication: The All-in-One High Frequency Welder for Metal Processing Offers Unmatched Efficiency and Versatility
The impact of the All-in-One High Frequency Welder extends beyond operational efficiency; it also contributes to cost savings. By consolidating multiple welding and cutting processes into one machine, businesses can reduce equipment acquisition costs and maintenance expenses over time. Moreover, the reduction in material waste as a result of superior welding quality means that companies can significantly lower their operational costs while maintaining output.
Investing in an All-in-One High Frequency Welder for Metal Processing not only empowers manufacturers to improve their quality of work but also positions them competitively within their respective industries. The combination of efficiency, versatility, and safety makes this modern welding solution an essential addition to any fabrication environment.
In conclusion, the All-in-One High Frequency Welder for Metal Processing represents a significant leap forward in welding technology. With its ability to enhance productivity and create high-quality welds across various materials, this advanced equipment is revolutionizing the metal processing industry. As manufacturers continue to seek improvements in efficiency and cost-effectiveness, incorporating such innovative tools will undoubtedly play a pivotal role in shaping the future of metal fabrication. Embracing this technology is more than a step toward modernization; it is a commitment to excellence in workmanship and customer satisfaction.Specialized Spare Parts for Large-Scale Tube Mills