****
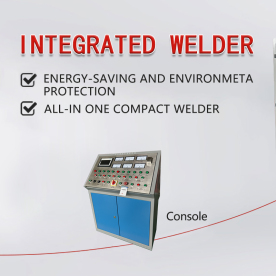
The Essential Guide to Specialized Spare Parts for Solid State HF Welder Maintenance: Ensuring Longevity and Efficiency in Metal Joining Processes
Solid State High Frequency (HF) welders have revolutionized the art of metal joining, offering a more efficient, reliable, and consistent method for producing high-quality welds. However, like any sophisticated piece of machinery, they require regular maintenance to keep operating at optimal performance. One of the most critical aspects of this maintenance lies in the usage of specialized spare parts. In this article, we will delve into the importance of these spare parts, discuss common wear and tear issues, and provide insights on how to manage maintenance schedules efficiently.
The Importance of Specialized Spare Parts
Specialized spare parts are designed specifically for Solid State HF welders, ensuring compatibility and optimal performance. Unlike generic parts, which may fit physically but lack the necessary specifications and quality, specialized parts are engineered to meet the exact demands of these machines. Using such precision-engineered components minimizes the risk of equipment failure, which can lead to production downtimes and increased operational costs.
Moreover, using these specialized spare parts contributes to the quality of the welding process. The welders operate at high frequencies, and any discrepancies in parts can lead to poor weld quality, which can compromise the integrity of the finished product. By investing in high-quality specialized spare parts, companies ensure that they maintain production standards and can deliver reliable results to customers.
Common Wear and Tear Issues
Solid State HF welders are often subjected to continuous operation, which could lead to several wear and tear issues. Understanding these common issues is vital for implementing effective maintenance strategies.
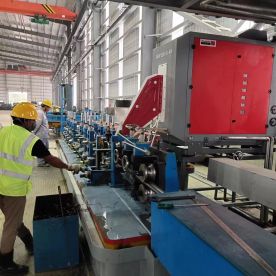
The Essential Guide to Specialized Spare Parts for Solid State HF Welder Maintenance: Ensuring Longevity and Efficiency in Metal Joining Processes
1. **Electrode Wear**: Electrodes often experience significant wear during the welding process due to heat and pressure. Over time, worn electrodes can lead to poor weld quality and increased energy consumption. Regular inspection and replacement of electrodes can help prevent these issues.
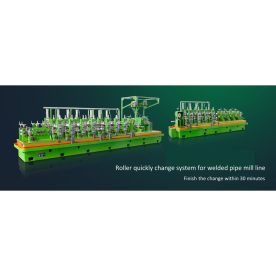
The Essential Guide to Specialized Spare Parts for Solid State HF Welder Maintenance: Ensuring Longevity and Efficiency in Metal Joining Processes
2. **Capacitor Degradation**: Capacitors are essential for energy storage and delivery in solid-state systems. However, they can degrade over time, leading to inconsistencies in the output power generated during welding. Replacing aged capacitors with specialized ones can greatly enhance operational reliability.
3. **Cooling System Failures**: The high-frequency welding processes generate a considerable amount of heat, necessitating efficient cooling systems. If cooling components such as fans or coolant pumps fail, it can lead to overheating and ultimately damage the welder. Having specialized spare parts for these systems on hand is essential.
4. **Transformers**: Transformers play a crucial role in converting electrical energy to the appropriate frequency needed for welding. Any defects in the transformer can result in inefficient power conversion and inadequate welding performance. Regular monitoring and timely replacement of faulty transformers are vital.
Effective Management of Maintenance Schedules
To maximize the lifespan and efficiency of Solid State HF welders through specialized spare parts, it is essential to implement a well-structured maintenance schedule. Here are some steps to follow:
1. **Regular Inspections**: Schedule periodic inspections of the welder to identify any signs of wear or damage early on. This proactive approach can prevent larger issues from arising, which might require more extensive repairs or replacements.
2. **Inventory Management**: Keep a well-stocked inventory of specialized spare parts that are commonly required for maintenance. This ensures that in case of wear or failure, replacements can be made quickly, minimizing downtime.
3. **Professional Training**: Train maintenance personnel on the specific requirements of Solid State HF welders. Knowledge of the system, parts, and potential failure points will enable staff to perform more effective maintenance.
4. **Document Everything**: Keep detailed records of maintenance activities, inspections, parts replacements, and performance metrics. This information will be invaluable for identifying trends in wear and tear and for planning future maintenance tasks.
Conclusion
Specialized spare parts play a vital role in the maintenance and operation of Solid State HF welders. By understanding the importance of these components, recognizing potential wear and tear issues, and implementing an effective maintenance schedule, businesses can enhance the longevity and efficiency of their welding operations. Investing in high-quality specialized spare parts not only ensures consistent production quality but also significantly reduces the risk of unexpected machine failures. As the demand for high-quality welding applications continues to grow, keeping solid-state HF welders in top-notch condition will become increasingly essential for industry success.Pipe mill production line