**Introduction**
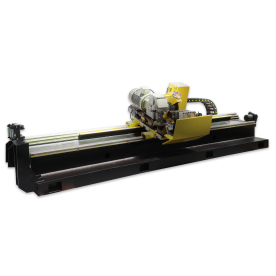
Exploring the Advantages and Innovations of Precision Tube Making Equipment for Modern Manufacturing Industries
In today’s fast-paced manufacturing environment, the need for precision, efficiency, and innovation cannot be overstated. Precision tube making equipment stands at the forefront of this technological revolution, providing industries ranging from automotive to medical with the tools necessary to create high-quality tubular components. This article will explore the various types of precision tube making equipment, their applications, benefits, and recent innovations that have transformed their efficiency and output quality.
**Understanding Precision Tube Making Equipment**
Precision tube making equipment refers to specialized machinery designed to manufacture tubes and pipes with stringent tolerances. The equipment encompasses a variety of processes, including welding, forming, shaping, and finishing. Manufacturers utilize precision tube making equipment to produce tubes that meet specific dimensions, wall thicknesses, and surface finishes, which are essential for various applications.
**Types of Precision Tube Making Equipment**
1. **Tube Mills:** Tube mills are essential for the continuous production of tubes. These machines utilize flat strips or coils of metal that are processed through various stages of forming and welding. The tube mills can operate at high speeds, allowing for large volumes of production with high precision.
2. **Welding Machines:** Welding machines are integral to the precision tube making process. They employ different welding techniques, such as TIG, MIG, or laser welding, to join edges of the metal strips to form a tube. Advanced welding machines are equipped with automation and sensing technology to ensure consistent and reliable welds.
3. **Tube Benders:** Tube benders are used to create precise bends in tubular components. These machines can make complex shapes while maintaining the integrity of the material. Modern CNC tube benders enable manufacturers to program various bend angles and radii, increasing productivity and reducing error.
4. **Cutting and Finishing Machines:** After the tube forming process, cutting and finishing machines come into play to achieve the desired lengths and surface finishes. Options include saws, laser cutting machines, and polishing equipment. These machines enhance the final product’s quality while ensuring it meets stringent industry standards.
5. **Inspection and Testing Equipment:** Quality assurance is paramount in tube manufacturing. Inspection and testing equipment, including non-destructive testing and measurement tools, are implemented to verify that each tube meets the specified tolerances and material properties.
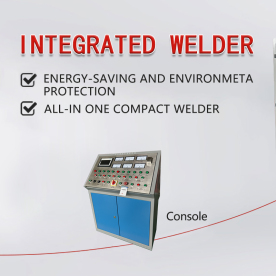
Exploring the Advantages and Innovations of Precision Tube Making Equipment for Modern Manufacturing Industries
**Applications of Precision Tube Making Equipment**
Precision tubes find applications in many industries, including:
– **Automotive Industry:** Used in exhaust systems, fuel lines, and structural components, precision tubes are vital for vehicle performance and safety.
– **Medical Devices:** The medical field requires stainless steel and specialty alloy tubes for applications such as catheters and surgical instruments, where precision is critical.
– **Aerospace:** Aerospace components necessitate high-strength and lightweight tubes, making precision tube manufacturing essential for airframe structures and engine components.
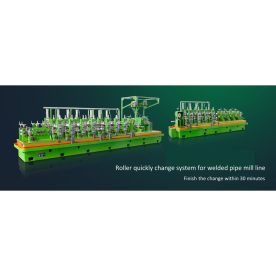
Exploring the Advantages and Innovations of Precision Tube Making Equipment for Modern Manufacturing Industries
– **Energy Sector:** Precision tubes are crucial for critical infrastructure, including pipelines, heat exchangers, and pressure vessels in oil and gas, as well as renewable energy systems.
**Benefits of Precision Tube Making Equipment**
The use of precision tube making equipment offers numerous advantages:
1. **High Precision and Quality:** With advanced technology, manufacturers can achieve tighter tolerances and higher-quality finishes, which are critical in applications where performance is directly linked to component quality.
2. **Increased Efficiency:** Automated precision tube making equipment allows for faster production cycles, reducing lead times and enabling manufacturers to meet growing demands without compromising quality.
3. **Cost-Effective Solutions:** While the initial investment in precision tube making equipment can be substantial, the long-term savings in material waste, energy consumption, and labor make it a cost-effective solution for manufacturers.
4. **Versatility:** Modern precision tube making equipment can accommodate a wide variety of materials, shapes, and sizes, providing manufacturers with the flexibility to adapt to changing market demands.
**Recent Innovations in Precision Tube Making Equipment**
The landscape of precision tube making is continuously evolving with technological advancements. Innovations such as Industry 4.0, IoT integration, and AI-driven analytics have started to play significant roles. These technologies enable real-time monitoring of the production process, predictive maintenance, and improved design capabilities, ensuring optimal performance and minimizing downtime.
**Conclusion**
Precision tube making equipment represents a crucial aspect of modern manufacturing, enabling industries to produce high-quality, reliable tubular components. With ongoing innovations and an increasing emphasis on efficiency and precision, the future of tube manufacturing appears promising. Companies that invest in advanced tube making equipment will be well-positioned to meet the evolving demands of their respective industries, ensuring they remain competitive in an ever-changing market.High-speed Pipe making machinery