****
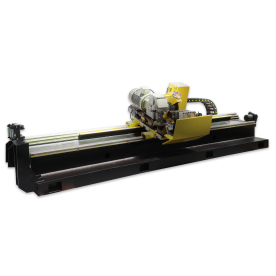
Revolutionizing Manufacturing: Understanding the Benefits of Tube Making Machines with Cutting Function in Modern Industry
In the fast-paced world of manufacturing, the quest for efficiency, precision, and versatility has never been more critical. One of the most significant advancements in this field is the development of tube making machines equipped with cutting functions. These innovative machines are transforming how various industries produce tubular products, offering advantages that significantly enhance productivity, reduce waste, and improve overall product quality. In this article, we will explore the features and benefits of tube making machines with cutting functions, analyzing their impact on modern manufacturing processes.
Understanding Tube Making Machines
A tube making machine is a specialized piece of equipment designed for the production of metal or plastic tubes and pipes. These machines operate by taking raw materials, such as coils or sheets, and shaping them into cylindrical forms through processes like rolling, bending, or welding. Traditionally, tube making machines were separate from cutting equipment, requiring additional tools and processes to achieve finished products. This separation often led to inefficiencies, increased labor costs, and a greater risk of errors.
Benefits of Integrated Cutting Functions
The integration of cutting functions into tube making machines has revolutionized the industry by streamlining the manufacturing process. Here are some of the key benefits:
1. **Increased Efficiency**: With the cutting function built into the tube making machine, manufacturers can significantly reduce the time taken to produce finished products. Instead of producing long tubes that require secondary cutting processes, these machines can create accurately sized tubes in a single operation. This integration leads to shorter production cycles and faster turnaround times, which are critical in today’s competitive market.
2. **Enhanced Precision**: Tube making machines with cutting functions are equipped with advanced technology that ensures high levels of precision in both the shaping and cutting processes. Automated cutting systems can be programmed to deliver exact lengths and tolerances, minimizing the need for manual adjustments and reducing the potential for errors. This level of accuracy is particularly important in industries where specifications are stringent, such as aerospace, automotive, and medical manufacturing.
3. **Reduced Waste**: Traditional methods often involved cutting excess material after tube formation, leading to a significant amount of waste. Integrated cutting functions help to minimize this problem by producing tubes that are the correct length from the outset. This reduction in scrap material not only contributes to cost savings but also aligns with the increasing focus on sustainable manufacturing practices.
4. **Versatility**: Modern tube making machines with cutting functions can handle a variety of materials, including stainless steel, aluminum, plastic, and other composites. This versatility allows manufacturers to adapt to changing market demands without investing in multiple specialized machines. Additionally, these machines can be programmed to produce tubes of various diameters and wall thicknesses, further expanding their range of applications.
5. **Labor Savings**: By automating the tube making and cutting processes, manufacturers can reduce their labor requirements. Fewer operators are needed to monitor the machines as they work efficiently and consistently. This reduction in labor not only cuts costs but also allows skilled workers to focus on more valuable tasks within the production environment.
6. **Improved Safety**: With fewer manual handling processes and automated cutting systems, the risks associated with workplace injuries during tube production are significantly lowered. Integrated systems can be equipped with safety features such as emergency stops, light curtains, and protective enclosures, creating a safer working environment.
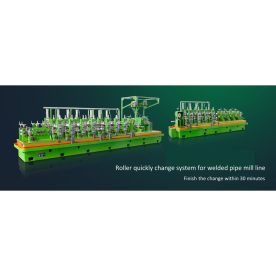
Revolutionizing Manufacturing: Understanding the Benefits of Tube Making Machines with Cutting Function in Modern Industry
Conclusion

Revolutionizing Manufacturing: Understanding the Benefits of Tube Making Machines with Cutting Function in Modern Industry
As industries continue to evolve, the demand for more efficient, accurate, and sustainable manufacturing processes will only grow. Tube making machines with cutting functions represent a significant leap forward, offering remarkable benefits that enhance productivity and quality while reducing costs. By embracing this technology, manufacturers can stay ahead of the curve, meeting the complexities of modern production demands with confidence and ease.
Investing in tube making machines with cutting functions is an investment in the future of manufacturing, one that ensures companies remain competitive in an ever-changing landscape. As the industry continues to innovate, it is clear that these machines will play a pivotal role in driving advancements and shaping the future of production processes.ERW tube mill