****
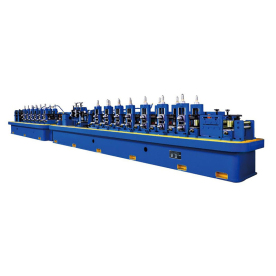
Enhancing Efficiency and Precision in Manufacturing: The Importance of Customized Spare Parts for Cold Cutting Saw Machines
In the ever-evolving world of manufacturing, efficiency, precision, and productivity are paramount. This is particularly true in industries that utilize cold cutting saw machines, which are essential for metalworking, construction, and various engineering applications. To maintain the performance and longevity of these machines, the role of customized spare parts cannot be understated. Customized spare parts are specifically designed to meet the unique needs of individual machines, ensuring they operate at their maximum potential. In this article, we will explore why customized spare parts are crucial for cold cutting saw machines, including their benefits, the design process, and how they can drive overall productivity in manufacturing settings.
Understanding Cold Cutting Saw Machines
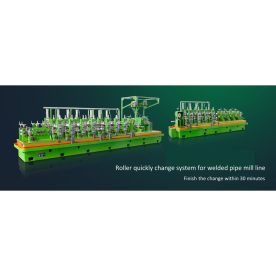
Enhancing Efficiency and Precision in Manufacturing: The Importance of Customized Spare Parts for Cold Cutting Saw Machines

Enhancing Efficiency and Precision in Manufacturing: The Importance of Customized Spare Parts for Cold Cutting Saw Machines
Cold cutting saw machines are designed to cut through various materials—primarily metals—without generating significant heat that could compromise the integrity of the material. These machines use specialized saw blades that make clean, precise cuts, which is essential in applications such as metal fabrication, automotive component manufacturing, and construction. Given the demands placed on these machines, regular maintenance and the use of high-quality spare parts become vital for ensuring continued operational success.
The Need for Customized Spare Parts
Every cold cutting saw machine is engineered differently, often tailored to specific tasks, materials, or operational conditions. Generic spare parts may not fit well or operate efficiently in these machines, leading to potential downtimes and increased production costs. Customized spare parts address this issue by providing components that are specifically manufactured to align with the exact specifications and performance requirements of a given machine.
Benefits of Customized Spare Parts
1. **Enhanced Performance**: Customized parts can significantly improve the performance of cold cutting saw machines. When parts are designed to fit perfectly and function optimally with the existing machine components, it enhances precision cutting capabilities and ensures smoother operations.
2. **Durability and Longevity**: High-quality customized spare parts are often made from superior materials that are engineered to withstand the specific operational stresses of cold cutting applications. This contributes to the longevity of the machinery, reducing the frequency of breakdowns and the need for replacements.
3. **Cost-effectiveness**: Although the initial investment in customized spare parts may be higher than generic alternatives, they often prove to be more cost-effective in the long run. By reducing machine downtime and the frequency of repairs, manufacturers can save significantly on operational costs.
4. **Increased Productivity**: Customized spare parts can help reduce the time taken for machine repairs and maintenance. With machines functioning at their optimal levels, manufacturers can achieve higher output rates, resulting in increased productivity.
5. **Improved Safety**: Cold cutting saw machines operate under significant stress and demand precise performance. Customized spare parts can prevent unexpected failures that could lead to hazardous situations, thereby promoting a safer working environment.
The Design and Production Process
Creating customized spare parts involves a detailed process. First, manufacturers assess the specific needs and operational conditions of the cold cutting saw machines in question. This may involve analyzing the wear patterns on current components, evaluating the machine’s operational environment, and understanding material requirements.
Once the assessment is complete, engineers and designers enter the design phase, employing CAD (computer-aided design) tools to create models of the spare parts. Prototyping follows, where initial models are tested for fit and functionality. Feedback from these tests leads to modifications, ensuring that the final product meets all necessary performance specifications.
Manufacturers frequently choose advanced techniques such as CNC machining, 3D printing, and advanced materials engineering to produce these specialized components. Such technology allows for high precision and the ability to tailor parts to the exact dimensions required for optimal performance.
Conclusion
In the competitive landscape of modern manufacturing, the role of customized spare parts for cold cutting saw machines cannot be overlooked. They enhance performance, ensure durability, improve safety, and contribute significantly to overall productivity. As industries continue to demand higher efficiency and quality, investing in tailored solutions for machinery maintenance is a strategic approach that can lead to success. By prioritizing customized spare parts, businesses can ensure that their cold cutting saw machines operate at peak performance, thereby meeting production goals and maintaining a competitive edge in the market.Automatic high frequency welder