****
In today’s fast-paced manufacturing landscape, efficiency, productivity, and cost-effectiveness are paramount. Among various manufacturing processes, the production of tubular components through tube mills plays a vital role in numerous industries, including automotive, construction, and energy sectors. One critical aspect that significantly impacts the performance and longevity of tube mills is the use of durable moulds. This article delves into the importance of durable mould for tube mills, exploring its benefits, materials, and the innovative approaches that are shaping the future of tube manufacturing.
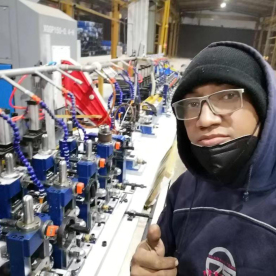
The Advantages of Utilizing Durable Mould for Tube Mills in Modern Manufacturing Processes
Understanding Tube Mills and Their Functionality
Tube mills are specialized machines designed to shape and weld metal strips into tubular forms. These structures are essential for various applications, including plumbing, heating, air conditioning, and structural frameworks. The efficiency and quality of the final product significantly depend on several factors, including the design of the moulds used during production.
The Role of Moulds in Tube Production
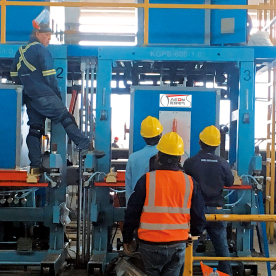
The Advantages of Utilizing Durable Mould for Tube Mills in Modern Manufacturing Processes
Moulds in tube mills guide the metal strips through the shaping process, ensuring they assume the desired diameter, thickness, and profile. The design and material of the mould critically affect the production speed, product quality, and the operational lifespan of the machinery.
Advantages of Using Durable Mould in Tube Mills
1. **Enhanced Longevity**: One of the most significant benefits of durable moulds is their longevity. Traditional moulds may wear out quickly under the high tensions and temperatures typically experienced in tube mills. Durable moulds are constructed from high-grade materials resistant to wear and tear, ensuring they maintain their shape and functionality over an extended period, ultimately reducing downtime and maintenance costs.
2. **Improved Production Efficiency**: Durable moulds facilitate smoother operations within tube mills. Since they maintain their integrity throughout the production process, businesses can achieve a higher throughput. In contrast, lower-quality moulds may lead to interruptions due to frequent failures or the need for adjustments, which directly affect overall productivity.
3. **Consistent Quality of Tubular Products**: The quality of the final product is critical in demanding applications where precision is paramount. Durable moulds ensure that the dimensions are consistent throughout the production run, leading to high-quality tubular products that meet industry standards. This consistency helps manufacturers build a reputation for reliability and excellence.
4. **Cost-Effectiveness**: While the initial investment in durable moulds may be higher than standard options, the long-term savings are significant. Reduced maintenance, lower frequency of replacements, and improved production efficiency all contribute to a favorable return on investment. In the competitive manufacturing sector, such cost-effective solutions can differentiate successful businesses from their rivals.
5. **Customization Capabilities**: Modern manufacturing often calls for customization to meet specific market demands. Durable moulds can be designed or adjusted to accommodate various specifications, allowing manufacturers to produce a diverse range of tubular products while maintaining efficiency. This flexibility is crucial in adapting to changing industry needs without significant downtime.
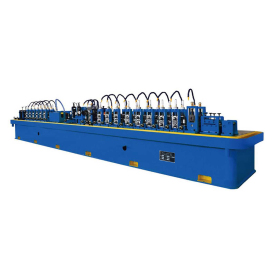
The Advantages of Utilizing Durable Mould for Tube Mills in Modern Manufacturing Processes
Materials Used for Durable Moulds
The construction of durable moulds is pivotal to their performance. Common materials used include:
– **High-Speed Steel (HSS)**: Known for its ability to withstand high temperatures, HSS moulds offer excellent wear resistance.
– **Tool Steels**: These steels are designed for high-stress applications and provide superior durability compared to standard steels.
– **Carbide**: Often used in high-performance applications, carbide moulds can operate under extreme conditions, delivering exceptional longevity.
Innovative Approaches in Mould Design
Advancements in technology have also led to innovations in mould design and production. Techniques such as 3D printing are becoming more prevalent, allowing for complex geometries that were previously difficult to achieve. Furthermore, tailored heat treatment processes enhance the durability of moulds, ensuring they can withstand the rigors of production.
Conclusion
The significance of durable moulds in tube mills cannot be overstated. From enhancing product quality and consistency to improving efficiency and reducing operational costs, investing in high-quality moulds is a strategic decision that can yield substantial returns in the long run. As industries continue to evolve, the adoption of durable moulds will play a crucial role in ensuring manufacturers remain competitive and capable of meeting the challenges of the modern manufacturing environment. By prioritizing durability, businesses can optimize their tube production processes and pave the way for innovation and growth in their respective markets.Spare Parts Kit for Tube Mills