In today’s rapidly evolving industrial landscape, the manufacturing of steel pipes has become integral to numerous sectors, including construction, automotive, oil and gas, and plumbing. The efficiency and capability of pipe making machines for steel play a pivotal role in meeting the rising demand for quality steel products. This article explores the significance, functionality, and advancements in pipe making machines, highlighting their impact on steel manufacturing and various industries.
**Evolution of Pipe Making Machines**
Over the years, pipe making machines have undergone significant transformations. The early models were primarily manual, relying heavily on human labor and requiring extensive skill to operate effectively. However, with the advent of technology, these machines have evolved into highly sophisticated, automated systems that can produce pipes with minimal human intervention.
Modern pipe making machines are equipped with advanced features such as computer numerical control (CNC) systems, which allow for precise measurements and cuts. This automation not only increases production rates but also enhances the quality of the finished products. Manufacturers are now able to produce steel pipes of varying sizes, shapes, and specifications, catering to the diverse needs of their clients.
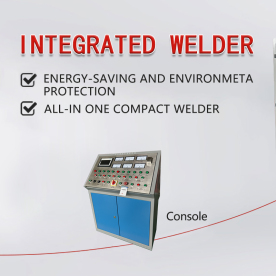
The Importance of Advancements in Pipe Making Machines for Steel Manufacturing in the Modern Industry
**Types of Pipe Making Machines**
Various types of pipe making machines are utilized in the steel industry. Some of the most common include:
1. **ERW Pipe Making Machines**: These machines use electric resistance welding technology to produce longitudinally welded pipes. They are known for their efficiency and are widely used in the production of various steel pipe grades.
2. **Spiral Pipe Making Machines**: These machines generate pipes by spiraling the steel strip, which is then welded together. Spiral pipes are particularly useful for large diameters and are popular in construction and infrastructure projects.
3. **Seamless Pipe Making Machines**: Unlike welded pipes, seamless pipes are manufactured without joints, offering higher strength and durability. The production process involves the use of a solid round billet that is heated and then pierced to create a hollow tube.
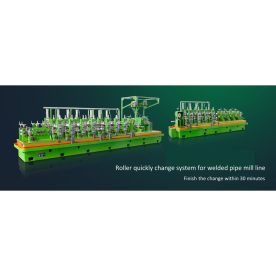
The Importance of Advancements in Pipe Making Machines for Steel Manufacturing in the Modern Industry
Each type of pipe making machine serves a specific purpose and is chosen based on the requirements of the application.
**Benefits of Modern Pipe Making Machines**
The adoption of modern pipe making machines in steel manufacturing comes with numerous benefits:
1. **Improved Production Efficiency**: Automated machines can operate at high speeds, significantly increasing the output of steel pipes. This efficiency translates to lower production costs and shorter delivery times for clients.
2. **Enhanced Quality Control**: Advanced technologies integrated into these machines ensure that each pipe produced meets strict quality standards. Automated inspection systems can detect flaws or inconsistencies in real time, reducing the likelihood of defective products making it to the market.
3. **Flexibility and Customization**: Modern machines offer a degree of flexibility that allows manufacturers to produce custom sizes and shapes according to specific client requirements. This adaptability is crucial in meeting the demands of various industries, from aerospace to construction.
4. **Reduced Labor Costs**: With automation, the reliance on skilled labor is minimized, reducing labor costs and allowing employees to focus on more complex tasks that add value to the manufacturing process.
5. **Sustainability**: Many modern pipe making machines are designed with energy efficiency in mind, contributing to the overall sustainability of the manufacturing process. By reducing waste and energy consumption, these machines help companies lower their carbon footprint.

The Importance of Advancements in Pipe Making Machines for Steel Manufacturing in the Modern Industry
**Conclusion**
The advancements in pipe making machines for steel are transforming the manufacturing landscape, offering enhanced efficiency, quality, and customization. As the global demand for steel pipes continues to rise, manufacturers must leverage these innovations to remain competitive and meet the strategic needs of industries worldwide.
The future of pipe manufacturing looks promising, with continuous improvements in technology pointing toward even greater advancements. As industries strive for higher productivity and sustainability, the role of state-of-the-art pipe making machines will only become more critical in the years to come. Embracing these changes not only benefits manufacturers but also sets the foundation for more robust infrastructures and sustainable practices across various sectors.Precision Solid state HF welder