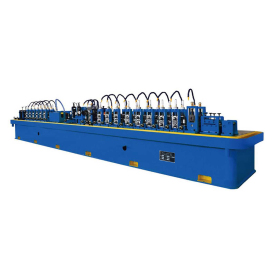
Discover the Benefits of the High-efficiency All-in-one Welding System: Streamlining Your Welding Projects with Advanced Technology
Welding is a critical component in various industries, including automotive, construction, and manufacturing. As technology continues to advance, traditional welding methods are being replaced by more efficient and integrated solutions. One such innovation is the High-efficiency All-in-one Welding System, which brings together multiple welding processes into a singular, easy-to-use unit. This article explores the features, advantages, and applications of this cutting-edge welding solution, emphasizing how it can revolutionize your approach to welding projects.
What is a High-efficiency All-in-one Welding System?
A High-efficiency All-in-one Welding System is designed to streamline the welding process by combining various welding methods into a single, compact machine. Traditionally, welders had to invest in multiple pieces of equipment, each dedicated to a specific welding technique (MIG, TIG, Stick, etc.). The all-in-one system consolidates these methods, allowing users to switch between them with ease, without sacrificing power, performance, or precision.
Typically, these machines feature advanced digital controls that enable precise adjustments to voltage, wire feed speed, and amperage settings, facilitating improved weld quality. Furthermore, they often include a robust cooling system, making them suitable for intensive tasks over extended periods.
Advantages of the High-efficiency All-in-one Welding System
1. Versatility
The most significant advantage of an all-in-one welding system is its versatility. Whether you’re working with thin sheet metals or heavy-duty structural components, this system can easily adapt to various welding methods. Users can tackle a wide range of materials—including stainless steel, aluminum, and mild steel—without needing to switch machines or setup configurations.
2. Space and Cost Savings
With traditional welding setups, the need for multiple machines can quickly consume valuable shop space and financial resources. An all-in-one system alleviates these issues, freeing up workspace and requiring only one machine to handle the job of many. This reduction in equipment not only saves money on the initial investment but also on maintenance costs over time.
3. Increased Productivity
An all-in-one welding system can significantly enhance productivity in the workshop. The ability to switch between welding processes quickly means that operators can complete various jobs without the downtime associated with setup changes. Additionally, modern all-in-one systems often come equipped with fast and efficient cooling mechanisms to accommodate higher workloads, reducing the time spent waiting between tasks.
4. Enhanced Weld Quality
The incorporation of digital controls allows for precise adjustments, which contribute to improved weld quality. Many systems are designed to provide consistent and repeatable results, which is particularly invaluable for production environments where uniformity is key. This feature minimizes errors and rework costs, ensuring a higher quality of finished products.
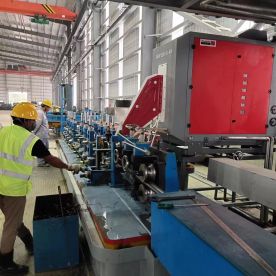
Discover the Benefits of the High-efficiency All-in-one Welding System: Streamlining Your Welding Projects with Advanced Technology
5. User-friendly Interfaces
Most high-efficiency all-in-one welding systems come with intuitive interfaces that simplify operation, making them accessible even to less experienced welders. Many models feature digital displays that provide real-time feedback on settings, enabling users to make informed decisions quickly. For businesses, this translation into easier training processes can be especially beneficial.
Applications for the High-efficiency All-in-one Welding System
The applications of a High-efficiency All-in-one Welding System are vast and varied. Industries ranging from automotive repair shops to large-scale manufacturing facilities can utilize this technology to enhance their operations. Small businesses and hobbyists also benefit from its versatility and compact size, enabling them to undertake diverse projects without needing extensive equipment investment.
Automotive Industry
In the automotive sector, where various metals and welding processes are frequently used, this welding system allows for quick transitions between different kinds of welds. It’s ideal for tasks like frame repairs, custom fabrications, and exhaust system installations.
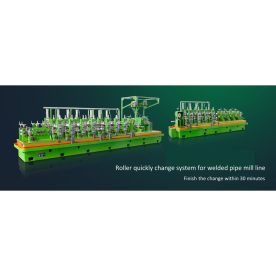
Discover the Benefits of the High-efficiency All-in-one Welding System: Streamlining Your Welding Projects with Advanced Technology
Construction and Fabrication
For construction and metal fabrication, a high-efficiency all-in-one system provides the flexibility to work on-site or in the workshop. Its ability to handle different materials means that welders can adapt to varying job requirements, whether they are erecting steel structures or creating intricate metal designs.
Home Projects and Artisans
DIY enthusiasts and artisans find great joy in the capabilities of all-in-one welding systems. From crafting metal art pieces to building personal projects, these machines offer the flexibility and performance needed to bring creative visions to life.
Conclusion
The introduction of the High-efficiency All-in-one Welding System marks a significant advancement in welding technology. Its versatility, cost-effectiveness, and ability to enhance productivity make it a valuable tool for professionals across multiple industries. Whether you’re a seasoned welder or a newcomer to the craft, investing in an all-in-one system can elevate your capabilities while simplifying your workflow. With the right equipment at your disposal, you can tackle any welding project with confidence and precision.Industrial-grade induction heating equipment