In the modern manufacturing landscape, efficiency and innovation are pivotal for success. One of the significant advancements in this realm is the development of pipe mill production lines with integrated welding and cutting functions. These advanced systems have revolutionized how pipes are produced, processed, and finished, yielding numerous benefits to manufacturers across various industries. This article delves into the critical features, advantages, and future possibilities of these sophisticated production lines.
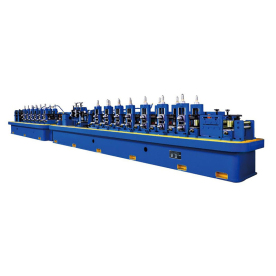
Exploring the Advancements in Pipe Mill Production Lines with Integrated Welding and Cutting Functions for Enhanced Manufacturing Efficiency
Understanding Pipe Mill Production Lines
Pipe mill production lines are specialized systems designed for the continuous production of pipes made from various materials, including steel, aluminum, and plastic. The process typically involves forming a flat strip of metal into a cylindrical shape, welding the seam, and then cutting the finished product to required lengths. However, traditional methods often required separate machines for each production step, resulting in inefficiencies and increased production costs.
The integration of welding and cutting functions within a single production line addresses these shortcomings. By streamlining the manufacturing process, manufacturers can enhance productivity, minimize labor costs, and reduce machinery maintenance and operational complexities.
Key Components of Integrated Production Lines
The modern pipe mill production line comprises several essential components blended into a single system. The primary stages include:
1. **Material Preparation**: The process begins with loading raw materials onto the line. This may involve uncoiling flat steel strips or feeding other material formats into the system.
2. **Forming**: Once the materials are in place, they are shaped into a pipe configuration. This step may utilize various methods, such as roll forming, which precisely molds the strips as they pass through a series of rollers.
3. **Welding**: After the forming stage, the edges of the pipe are joined using welding techniques. Depending on the material and specifications, manufacturers may utilize high-frequency electric resistance welding (HF ERW) or submerged arc welding (SAW). These welding methods provide strong, durable joints that ensure the integrity of the final product.
4. **Cutting**: Once welded, the pipes are cut to the desired lengths. Integrated cutting functions enable precise measurements and can adjust quickly to varying lengths, reducing waste and ensuring uniformity across products.
5. **Finishing**: After cutting, additional finishing processes may be applied, including surface treatments and inspections before the pipes are packaged for shipment.
Benefits of Integrated Welding and Cutting Functions
1. **Increased Efficiency**: By consolidating multiple functions into one line, manufacturers can significantly reduce production times. This seamless process minimizes material handling and transportation times, accelerating overall output.
2. **Reduction in Production Costs**: Fewer machines mean lower operational costs, including reduced energy usage, maintenance requirements, and labor costs. Manufacturers can allocate resources more effectively while maximizing return on investment.
3. **Enhanced Product Quality**: With integrated systems, welding and cutting processes can be closely monitored and optimized, ensuring consistent quality throughout production. This level of precision translates to fewer defects and higher satisfaction among end users.
4. **Flexibility and Customization**: Modern production lines offer adaptability, allowing manufacturers to quickly switch between different product specifications. This flexibility is vital in today’s fast-paced market, as it enables companies to respond promptly to changing customer demands.
5. **Environmental Benefits**: Streamlined production processes through integrated systems often lead to improved resource utilization, decreased waste generation, and lower energy consumption, contributing to more sustainable manufacturing practices.
Future Prospects and Innovations
As technology continues to evolve, the future of pipe mill production lines with integrated welding and cutting functions holds immense potential. Advancements like automation, artificial intelligence, and machine learning are paving the way for smarter production lines that can self-monitor and adjust processes in real time, further improving efficiency and reducing human error.
Moreover, the rise of Industry 4.0 emphasizes connectivity, where production lines communicate with inventory systems and supply chains to optimize operations fully. This connectivity ensures that manufacturers can forecast demand, control stock levels, and adjust production schedules dynamically, enhancing overall operational efficiency.
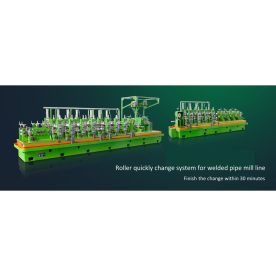
Exploring the Advancements in Pipe Mill Production Lines with Integrated Welding and Cutting Functions for Enhanced Manufacturing Efficiency

Exploring the Advancements in Pipe Mill Production Lines with Integrated Welding and Cutting Functions for Enhanced Manufacturing Efficiency
In conclusion, pipe mill production lines with integrated welding and cutting functions are redefining the manufacturing landscape. With their capacity to enhance efficiency, reduce costs, and improve product quality, these advanced systems position manufacturers for success in an increasingly competitive environment. As technology continues to advance, the potential for these production lines to evolve further offers exciting possibilities for the future of manufacturing.Cost-effective ERW tube mill options