In the manufacturing sector, especially in metal processing, the tube mill plays a crucial role in producing high-quality tubular products. This equipment is instrumental in shaping metal strips into seamless or welded tubes. One of the central components of a tube mill is the roller, which significantly impacts the operation’s efficiency and the quality of the final product. Understanding the function and importance of rollers in tube mills can provide insights into their critical role in modern manufacturing processes.
**What is a Tube Mill?**
A tube mill is a machine designed for the production of metal tubing by rolling flat metal strips into cylindrical shapes. This process can be carried out with or without welding. The most common types of tube mills include those for producing precision tubing for automotive, construction, and industrial applications. Given the diverse demands for precision and quality in tube production, the machinery employed must be robust, adaptable, and efficient.
**The Role of Rollers in Tube Mills**
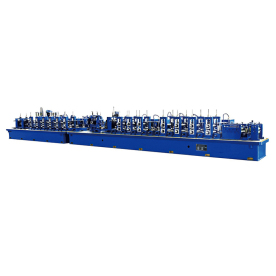
Exploring the Importance and Functionality of Rollers in Tube Mill Operations: Enhancing Efficiency and Product Quality
At the heart of a tube mill’s operation are the rollers. These cylindrical components are strategically positioned throughout the mill and serve multiple vital functions, including forming, shaping, and guiding the metal strip into a tube. Rollers come in various designs and materials, typically made of hardened steel, ensuring durability and longevity under high-pressure conditions.
1. **Shaping the Metal Strip**: The primary function of the roller in a tube mill is to shape the flat metal strip as it passes through. The rollers are configured in a series of stands that apply pressure and guide the strip into the desired cylindrical form. The angle and design of the rollers determine the final dimensions and wall thickness of the tube. Achieving precise control over these parameters is essential for meeting quality standards.
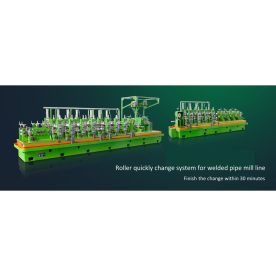
Exploring the Importance and Functionality of Rollers in Tube Mill Operations: Enhancing Efficiency and Product Quality
2. **Alignment and Stability**: Rollers also serve to keep the metal strip aligned as it moves through the tube mill. This alignment is crucial for maintaining consistent wall thickness and ensuring that the finished tubes do not exhibit any defects, such as waviness or unevenness. Proper alignment helps prevent costly rework and material waste, contributing to the overall efficiency of the production process.
3. **Cooling and Lubrication**: High-speed operations in tube mills generate considerable heat. Rollers can be designed to accommodate cooling mechanisms, utilizing water or oil to dissipate heat and lubricate the strip. Effective cooling not only prolongs the life of the rollers but also improves the surface finish of the tube, vital for applications requiring precision engineering.
4. **Enhancing Throughput**: The design and configuration of rollers can significantly impact the tube mill’s throughput. With the right set of rollers, manufacturers can achieve higher speeds in production while still maintaining product quality. This capability translates into enhanced productivity and profitability for businesses in competitive markets.
5. **Customizability and Versatility**: Rollers can be customized to meet the specific needs of different tube dimensions and material types. This adaptability allows manufacturers to produce a wide range of products on a single tube mill, minimizing the need for multiple machines and reducing capital costs.
**Challenges and Innovations in Roller Design**
Despite their importance, the design and maintenance of rollers come with challenges. Rollers are subject to wear and tear, requiring regular inspections and replacements to ensure optimal performance. The introduction of advanced materials and coatings has led to the development of rollers that offer increased resistance to wear and higher thermal fatigue limits, prolonging their operational life.
Innovations in roller design continue to evolve, with computer-aided tools enabling manufacturers to simulate and optimize roller shapes and arrangements before actual production. This capability not only maximizes efficiency but also allows manufacturers to maintain tight tolerances in tube production.
**Conclusion**

Exploring the Importance and Functionality of Rollers in Tube Mill Operations: Enhancing Efficiency and Product Quality
In conclusion, the role of rollers in tube mills is indispensable. They not only shape and align metal strips but also influence the overall efficiency and quality of the tube production process. As industries demand higher precision and efficiency, the innovation surrounding roller design and technology will remain a crucial focus for manufacturers. Through advancements in materials, design, and maintenance, the future of tube mills looks promising, paving the way for enhanced production capabilities and superior product quality. Understanding the intricacies and significance of rollers in tube mills is fundamental for anyone operating or investing in this vital segment of the manufacturing industry.Precision Cold Cutting Saw Machine