The stainless steel pipe mill production line is an intricate system designed to manufacture high-quality stainless steel pipes for various industrial applications. With the growing demand for stainless steel products across multiple sectors, including construction, automotive, and manufacturing, understanding the workings of this production line has become increasingly vital. This article delves into the components, processes, and advanced technologies that define a modern stainless steel pipe mill production line.
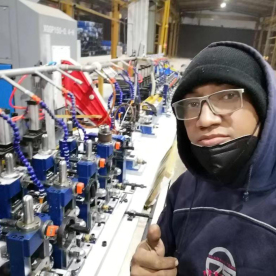
Exploring the Innovations and Processes Behind the Stainless Steel Pipe Mill Production Line: A Comprehensive Overview
Overview of the Stainless Steel Pipe Mill Production Line
At its core, a stainless steel pipe mill production line comprises several stages that transform raw stainless steel materials into finished pipes. The primary process involves casting, forming, welding, and finishing the stainless steel to meet specific size, dimension, and quality requirements. Each phase contributes to the consistency, strength, and durability essential for pipes used in challenging environments.
Raw Material Preparation
The production process begins with the selection of raw materials, primarily stainless steel coils or strips. These materials undergo careful inspection to ensure their composition and quality align with industry standards. Stainless steel is favored for its corrosion resistance, strength, and aesthetic appeal, making it an ideal choice for various applications.
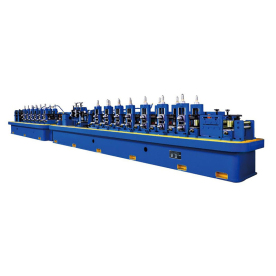
Exploring the Innovations and Processes Behind the Stainless Steel Pipe Mill Production Line: A Comprehensive Overview
Once the raw material passes inspection, it is cut into manageable lengths that will feed into the mill. This step is crucial, as consistent lengths help maintain uniformity throughout the production process.
Forming Process
After preparation, the raw stainless steel strips enter the forming stage. Here, advanced machinery rolls and shapes the material into a cylindrical form. The forming process can vary depending on the type of stainless steel pipe being produced. Common methods include:
– **Seamless Pipe Production**: This method involves piercing the heated billet to create a hollow tube, which is further elongated and shaped through a series of rolling processes. Seamless pipes are often preferred in high-pressure applications due to their structural integrity. – **Welded Pipe Production**: In this method, flat stainless steel strips are rolled into a shape and then welded at the seam. Advanced welding techniques, such as TIG (Tungsten Inert Gas) and MIG (Metal Inert Gas), are commonly employed to ensure a strong and consistent bond.
Welding and Heat Treatment
Welding is one of the most critical steps in stainless steel pipe manufacturing. For welded pipes, the seam must be meticulously fused to ensure that it can withstand internal pressures and other mechanical stresses. Quality control is paramount during this stage, and non-destructive testing methods, such as ultrasonic or eddy current inspections, are often utilized to check for flaws or weaknesses in the welds.
Following welding, heat treatment is implemented to relieve any stresses inflicted during the forming and welding processes. Heat treatment can enhance the mechanical properties of the stainless steel, ensuring it meets specific industry requirements, such as hardness and ductility.
Finishing Processes
Once the pipes have been welded and heat-treated, they proceed to the finishing stage, where they undergo several processes to achieve the desired surface quality and appearance. This phase often includes:
– **Pickling**: A chemical treatment that removes oxides and scale from the surface of the pipes, ensuring a clean and shiny finish that is vital for corrosion resistance.
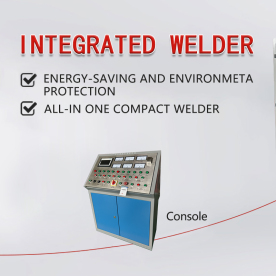
Exploring the Innovations and Processes Behind the Stainless Steel Pipe Mill Production Line: A Comprehensive Overview
– **Passivation**: This process enhances the natural oxide layer of the stainless steel, further improving its resistance to rust and corrosion.
– **Polishing**: Pipes can be polished to achieve various finishes, from rough to mirror-like surfaces, depending on customer specifications.
Quality Assurance
A comprehensive quality assurance program is crucial throughout the entire stainless steel pipe mill production line. Inspections at every stage ensure adherence to stringent standards set forth by organizations such as ASTM (American Society for Testing and Materials) and ISO (International Organization for Standardization). Ideal production lines are equipped with modern testing and measurement technologies, allowing for precise monitoring of dimensions, weight, and material properties.
Conclusion
The stainless steel pipe mill production line exemplifies the intersection of innovative technology and essential manufacturing processes. As industries continue to evolve and demand higher standards of quality and efficiency, the importance of advanced production lines becomes increasingly clear. Continuous advancements in automation, material science, and quality control are indispensable for producers looking to remain competitive in a dynamic market. Understanding the complexities of stainless steel pipe manufacturing not only underscores the processes involved but also highlights the role these products play in our daily lives and the global economy.Integrated pipe mill production line system