The world of manufacturing has witnessed a dramatic evolution over recent years, propelled by technological breakthroughs and increased demand for tailored solutions. In the pipe manufacturing sector, the need for customization has become increasingly vital, particularly as industries require precision, efficiency, and versatility in their operations. Enter the realm of pipe making machine customization solutions — a transformative approach designed to optimize production processes and meet the unique requirements of diverse applications.
Pipe making machines play a crucial role in producing pipes for various industries, including construction, plumbing, automotive, and oil and gas. The traditional manufacturing process, however, often falls short in addressing the specific needs of different projects. This is where customization comes into play. By modifying and tailoring the machinery, manufacturers can enhance operational efficiency and adapt to evolving market demands.
Understanding Pipe Making Machine Customization Solutions
Customization solutions for pipe making machines encompass a range of modifications and enhancements that can be tailored to a manufacturer’s specific requirements. These alterations can involve changes in design, function, and even technology used in the manufacturing process. Here are some of the key customization solutions available:
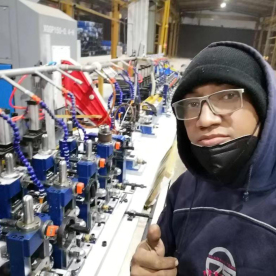
Innovative Pipe Making Machine Customization Solutions: Tailored Equipment for Enhanced Efficiency and Productivity in Pipe Manufacturing
1. **Machine Design Alterations**: Depending on the materials and types of pipes being produced, the design of a pipe making machine can be altered. This includes changing the size, shape, and configuration of components to accommodate different pipe diameters, wall thicknesses, and material types. For instance, custom roller dies and forming tools can be designed to create pipes with intricate profiles, enabling manufacturers to expand their product offerings.
2. **Integration of Advanced Technologies**: Modern pipe making machines can now be integrated with cutting-edge technologies such as automation, robotics, and IoT (Internet of Things). Customization solutions may include the installation of sensors for real-time monitoring and quality assurance, AI-driven analytics for predictive maintenance, and robotic arms for enhanced precision and speed during the manufacturing process. Such technologies not only improve operational efficiency but also reduce downtime and manufacturing costs.
3. **Flexibility for Multi-Product Manufacturing**: Industries dealing with varying products can benefit from customized solutions that allow for multi-product manufacturing capabilities. With the capability to switch between different pipe sizes, materials, or even production methods swiftly, manufacturers can respond quickly to market trends and customer demands without significant downtime. This adaptability is essential in today’s fast-paced market.
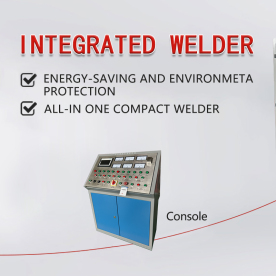
Innovative Pipe Making Machine Customization Solutions: Tailored Equipment for Enhanced Efficiency and Productivity in Pipe Manufacturing
4. **Enhanced Safety Features**: Customized pipe making machines can incorporate advanced safety measures tailored to the specific risks associated with the materials and processes involved. This might include improved guarding systems, automated shutdown features, and enhanced training programs that adapt to the new machinery configurations, ensuring a safer work environment for operators.
5. **Production Line Optimization**: Experts can analyze existing production lines to identify areas where customized pipe making machines can effectively integrate with other equipment. By streamlining workflows and reducing bottlenecks, manufacturers can significantly enhance productivity and overall throughput. This holistic approach ensures that every aspect of the production process is finely tuned for optimal performance.
The Benefits of Customized Solutions
Implementing pipe making machine customization solutions can yield numerous benefits for manufacturers:
– **Increased Efficiency**: Customizing machines to reflect the specific needs of the production process can lead to significant efficiency gains, reducing waste and minimizing energy consumption. – **Higher Product Quality**: Tailored machinery can enhance precision and consistency in pipe manufacturing, resulting in superior product quality that meets or exceeds industry standards. – **Cost-Effectiveness**: Though there may be initial investment costs, customized machines can ultimately reduce operational costs by improving efficiency and minimizing downtime. – **Competitive Advantage**: Customization allows manufacturers to differentiate their offerings in a crowded market, responding quickly to new trends and maintaining a competitive edge.
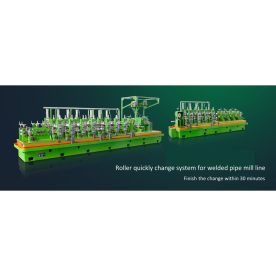
Innovative Pipe Making Machine Customization Solutions: Tailored Equipment for Enhanced Efficiency and Productivity in Pipe Manufacturing
Conclusion
The landscape of pipe manufacturing is rapidly changing, and customization solutions for pipe making machines are at the forefront of this transformation. By adapting machinery to meet specific operational needs, manufacturers can significantly improve efficiency, product quality, and overall competitiveness. As industries continue to evolve, those willing to invest in customization will likely find themselves leading the way in innovation and success in the pipe manufacturing market.Industrial All-in-one High Frequency Welder