In today’s fast-paced manufacturing environment, the demand for efficient, reliable, and versatile welding solutions is more crucial than ever. The introduction of the all-in-one high frequency welder machine marks a significant advancement in welding technology. This innovative equipment combines multiple welding processes and functions into a single unit, making it an invaluable asset for various industries, including automotive, construction, and electronics. In this article, we will explore the features, advantages, and applications of all-in-one high frequency welder machines, shedding light on why they are becoming a staple in modern fabrication shops.
Understanding the All-in-One High Frequency Welder Machine
At its core, the all-in-one high frequency welder machine utilizes high-frequency electrical currents to produce welds with superior precision and strength. Unlike conventional welding equipment that typically specializes in one type of welding process, this versatile machine can perform several tasks, including high-frequency induction welding, resistance welding, and even plastic welding. Its multifaceted capabilities enable operators to switch between different welding processes without needing multiple machines, thus saving time and costs associated with equipment maintenance, space, and training.
Key Features of High Frequency Welder Machines
– **Multipurpose Functionality:** As the name suggests, an all-in-one high frequency welder machine can perform various welding operations. This includes joining metals of different types and thicknesses, as well as working with non-metallic materials like plastics, making it suitable for a broad range of applications.
– **High Efficiency and Speed:** High-frequency welding technology allows for rapid heating and cooling cycles, resulting in faster weld times and improved productivity. This is essential for industries with high volume demands, enabling manufacturers to meet tight deadlines without sacrificing quality.
– **Precision and Control:** These machines offer advanced control systems, allowing operators to adjust parameters such as voltage, frequency, and time settings according to the specific requirements of the materials being welded. This level of precision helps ensure strong, reliable welds that can withstand varying conditions.
– **User-Friendly Interface:** Modern all-in-one high frequency welder machines come equipped with intuitive touchscreens and user interfaces that simplify operation and reduce the learning curve for new users. This is particularly beneficial for companies that need to train personnel quickly.
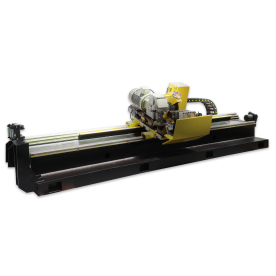
Revolutionizing Industrial Welding Processes: The Versatile Benefits of an All-in-One High Frequency Welder Machine
Advantages of All-in-One High Frequency Welder Machines
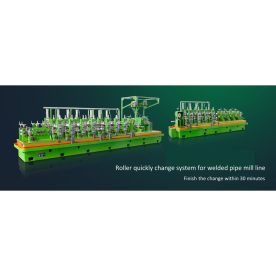
Revolutionizing Industrial Welding Processes: The Versatile Benefits of an All-in-One High Frequency Welder Machine
1. **Cost-Effective Solution:** By eliminating the need for multiple machines, manufacturers can significantly cut down on equipment costs, maintenance expenses, and the footprint of their operations. This economic advantage is particularly appealing for small and medium enterprises.
2. **Versatility:** The ability to switch between different welding processes effortlessly makes these machines ideal for companies that handle diverse projects. Whether it’s fabricating metal components or welding plastic parts, it provides a high degree of versatility.
3. **Enhanced Quality and Reliability:** With the precision control offered by high frequency welding, the resulting welds are often of higher quality compared to traditional methods. This leads to fewer defects, reduced rework, and greater overall reliability in the final products.
4. **Increased Productivity:** Companies can achieve higher output levels due to the speed and efficiency of all-in-one high frequency welder machines. This can lead to improved lead times and greater customer satisfaction.
Applications Across Industries
The all-in-one high frequency welder machine is not confined to a single industry. Its flexibility makes it suitable for a wide array of applications. In the automotive industry, it can be used for creating durable components in vehicles. In electronics, it can seamlessly bond different materials for circuit boards. The construction sector benefits from its ability to join materials such as steel and plastics used in various structural applications. Moreover, the medical industry increasingly relies on high-frequency welding for producing high-quality surgical instruments and devices.

Revolutionizing Industrial Welding Processes: The Versatile Benefits of an All-in-One High Frequency Welder Machine
Conclusion
As industries continue to evolve, embracing innovation is key to maintaining a competitive edge. The all-in-one high frequency welder machine encapsulates this spirit of advancement, providing a powerful tool for manufacturers seeking efficiency, quality, and versatility. By investing in this technology, businesses can unlock the potential for improved operations, reduced costs, and enhanced product reliability. In an era where adaptability is paramount, these machines are set to redefine the standards of welding processes across various sectors, making them a smart choice for forward-thinking enterprises.High-Performance HSS Blade for Precision Cutting