****
In the modern manufacturing landscape, tube mills play a crucial role in producing various types of steel tubes and pipes, which are integral for numerous industries ranging from construction to automotive. As with any complex machinery, tube mills are susceptible to wear and tear over time, necessitating a reliable inventory of spare parts to maintain their efficiency and longevity. This article explores the importance and types of spare parts needed for tube mills, the challenges in sourcing these parts, and best practices for inventory management.
Importance of Spare Parts in Tube Mills
Tube mills operate under continuous stress, which can lead to equipment failure if not properly maintained. Having a well-stocked inventory of spare parts is vital for ensuring the smooth operation of these mills. The cost of downtime in a manufacturing environment can be astronomical, with lost production, delayed orders, and potential damage to other machinery. Therefore, investing in spare parts not only mitigates the risk of operational halts but also extends the lifespan of the equipment.
Moreover, spare parts can have a direct impact on the quality of the finished product. Deterioration of components such as rollers, bearings, and seals can result in product defects, leading to scrapped tubes and financial loss. To produce high-quality tubes consistently, maintaining the integrity of the tube mill with high-quality spare parts is non-negotiable.
Types of Spare Parts for Tube Mills
Understanding the various components that comprise a tube mill is essential when discussing spare parts. Here’s a breakdown of some critical spare parts commonly found in tube mills:
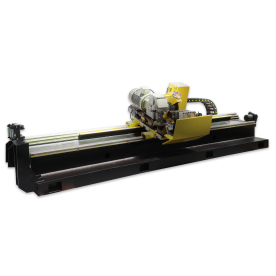
Essential Guide to Spare Parts for Tube Mill: Ensuring Operational Efficiency and Longevity in Manufacturing
1. **Rollers and Stands**: Rollers are subjected to intense pressure and abrasion, leading to wear over time. They must be replaced promptly to maintain the mill’s shape control and dimensional accuracy. Stands also experience wear due to their pivotal role in maintaining the alignment of the rollers.
2. **Bearings**: Bearings ensure smooth rotation of rollers and other moving parts. Regular inspections should be conducted to identify signs of wear. High-performance bearings can help in reducing friction, ultimately resulting in energy savings and increased operational efficiency.
3. **Seals**: Seals are crucial for preventing contamination from external particles and preserving lubrication inside the machinery. Failing seals can lead to increased wear and tear on internal components, necessitating frequent replacements and resulting in unplanned downtime.
4. **Gearboxes**: Gearboxes are vital for the transmission of power within the tube mill. Gear failure can halt operations entirely, making it essential to keep spare gearboxes or critical components such as gears and shafts readily available.
5. **Electrical Components**: Issues with electrical components, including capacitors, switches, and motor drives, can disrupt operations. Having replacements on hand can prevent extended downtime due to electrical failures.
Challenges in Sourcing Spare Parts
One of the main challenges manufacturers face is sourcing high-quality spare parts promptly. Due to the specialized nature of tube mills, off-the-shelf solutions are often inadequate. Manufacturers must either partner with original equipment manufacturers (OEMs) or reliable after-market suppliers that can provide suitable components. In addition, the variability in supply chain logistics can lead to delays in receiving critical parts, exacerbating downtime.
Furthermore, counterfeit parts present another significant risk. Using substandard components can lead to safety hazards, equipment failure, and, ultimately, costly repairs. It’s crucial to establish relationships with reputable suppliers and verify the authenticity of the parts to avoid these pitfalls.
Best Practices for Inventory Management
To effectively manage spare parts for tube mills, manufacturers should implement the following best practices:
1. **Conduct Regular Audits**: Regular audits of spare parts inventory can help identify fast-moving components that need replenishment, as well as slow-moving items that may no longer be necessary.
2. **Maintain Usage Records**: Keeping track of the usage patterns of spare parts allows for better forecasting and helps determine optimal reorder levels.
3. **Invest in Technology**: Utilizing inventory management software can streamline the process of tracking parts, managing stock levels, and forecasting future needs.
4. **Train Staff**: Ensuring that the staff responsible for maintenance understands the critical components of the tube mill will encourage proactive management of spare parts.
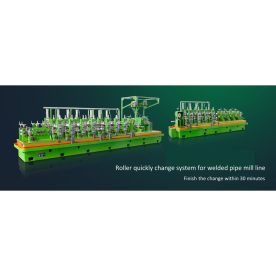
Essential Guide to Spare Parts for Tube Mill: Ensuring Operational Efficiency and Longevity in Manufacturing
5. **Establish Supplier Relationships**: Building solid relationships with suppliers can facilitate quicker turnaround times and ensure access to high-quality spare parts.

Essential Guide to Spare Parts for Tube Mill: Ensuring Operational Efficiency and Longevity in Manufacturing
Conclusion
Investing in spare parts for tube mills is not merely a logistical task but a strategic move that can significantly impact the efficiency and quality of manufacturing processes. By acknowledging the importance of these components, understanding the challenges involved in sourcing them, and adopting best practices for their management, manufacturers can ensure their equipment remains reliable and efficient. Through careful planning and execution, businesses can minimize downtime, enhance product quality, and ultimately drive greater profitability in their operations.Customized Flying Saw Machine