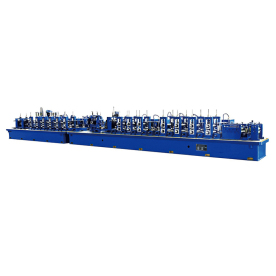
Revolutionizing Production: The Advantages and Applications of the Multi-Functional Tube Making Machine in Modern Manufacturing
In the rapidly evolving world of manufacturing, efficiency, versatility, and precision are paramount for businesses aiming to meet the demands of an ever-growing market. The advent of advanced machinery has led to significant shifts in production capabilities, and one significant innovation in this sphere is the multi-functional tube making machine. This robust machinery redefines the production of tubes, catering to a diverse array of industries, thereby enhancing productivity while reducing costs.
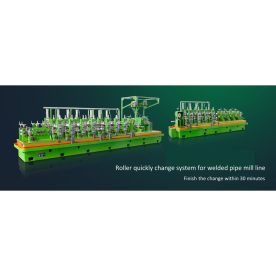
Revolutionizing Production: The Advantages and Applications of the Multi-Functional Tube Making Machine in Modern Manufacturing
A multi-functional tube making machine is engineered to produce tubes with exceptional accuracy and speed. Unlike traditional tube-making methods that often require multiple machines for different processes, this innovative equipment integrates various functions into a single unit. This means that processes such as cutting, bending, welding, and assembling can be carried out in a streamlined manner without the need to switch between different machines. For manufacturers, this translates to considerable time savings and reduced labor costs, as fewer personnel are required to operate the machine.
One of the most compelling features of the multi-functional tube making machine is its versatility. Designed to accommodate various materials—such as metals, plastics, and composites—these machines can produce tubes in differing sizes, shapes, and thicknesses. This flexibility is particularly beneficial for industries that require customized solutions, such as automotive, aerospace, and construction. By simply adjusting the machine settings, manufacturers can efficiently pivot their production lines to meet changing customer preferences, thereby enhancing their competitive edge.
Moreover, the incorporation of advanced technology has significantly improved the precision offered by multi-functional tube making machines. Many models are equipped with computer numerical control (CNC), allowing for highly detailed and repeatable designs. This precision is crucial for industries where tolerances must be within strict specifications to ensure the proper functionality of components. By leveraging CNC capabilities, manufacturers can ensure consistent quality across their product lines, enhancing brand reputation and customer satisfaction.

Revolutionizing Production: The Advantages and Applications of the Multi-Functional Tube Making Machine in Modern Manufacturing
The ability to produce a wide array of tube types is another significant advantage of these machines. From straight tubes to intricate shapes and designs, the multi-functional tube making machine can be configured to produce items such as exhaust pipes, structural supports, and fluid delivery systems. This high level of adaptability makes it an invaluable asset for businesses that service multiple sectors or that often find themselves seeking innovative design solutions.
In addition to manufacturing efficiency and versatility, the multi-functional tube making machine also contributes to sustainability in production. By reducing material waste through precise cutting and efficient use of resources, these machines align with the growing emphasis on environmentally responsible manufacturing practices. Furthermore, the increased efficiency means that production lines can operate at higher speeds while consuming less energy—benefits that not only enhance profitability but also support corporate responsibility goals.
Maintenance and operational ease are additional considerations for manufacturers when investing in a multi-functional tube making machine. Modern machines are often designed with user-friendly interfaces and maintenance protocols that minimize downtime and simplify training for new employees. By reducing the complexity associated with machine operation and upkeep, businesses can quickly adapt to new technologies and maintain optimal productivity levels.
However, adopting a multi-functional tube making machine does come with considerations that businesses must evaluate. The initial investment can be substantial, particularly for high-end models equipped with advanced features. Additionally, training staff to operate these sophisticated machines requires a time commitment and a potential increase in operational costs. Therefore, a detailed cost-benefit analysis is essential to determine whether the long-term efficiencies and savings outweigh the upfront expenditures.
In conclusion, the multi-functional tube making machine stands at the forefront of modern manufacturing, providing significant advantages in efficiency, versatility, precision, and sustainability. As industries continue to evolve, the ability to adapt quickly and reliably to changing demands becomes increasingly critical. By investing in this advanced machinery, manufacturers can not only streamline their production processes but also position themselves as leaders in their respective markets, ready to tackle the challenges of tomorrow. The future of tube manufacturing is bright, with multi-functional technologies paving the way for enhanced productivity and innovation.Pipe making machine with welding function