****
In the ever-evolving landscape of manufacturing and industrial processes, the demand for innovative technologies that can elevate efficiency, precision, and sustainability is at an all-time high. One such technology that has proven its worth is induction heating. As more companies recognize the benefits of customized induction heating equipment, industries ranging from automotive to electronics are witnessing impressive advancements. This article delves into the benefits and applications of customized induction heating equipment, shedding light on its role in enhancing production processes.
Understanding Induction Heating
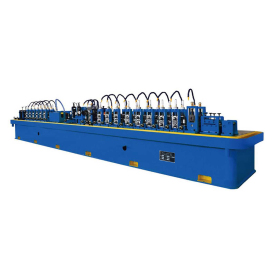
The Advantages of Customized Induction Heating Equipment for Enhanced Efficiency and Precision in Modern Manufacturing Processes
Induction heating is a process that utilizes electromagnetic induction to heat electrically conductive materials. When an alternating current passes through a coil, it generates a magnetic field. This magnetic field induces a current in the metal object placed within the coil, resulting in rapid heating of that object. Unlike traditional heating methods that rely on flames or external heat sources, induction heating provides a more efficient and targeted heating solution, minimizing energy waste and extending the lifespan of equipment.
The Need for Customization
While induction heating technology itself is robust, the needs of different industries can vary considerably. Factors such as the type of material being heated, the desired temperature, the heating duration, and the application method all influence how induction heating equipment should be designed. This is where customized induction heating equipment comes into play. Tailored solutions can address specific challenges faced by different manufacturing processes, ultimately resulting in improved productivity and cost savings.
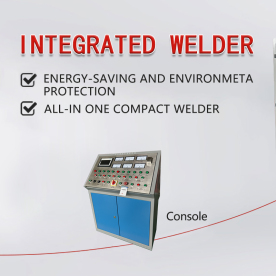
The Advantages of Customized Induction Heating Equipment for Enhanced Efficiency and Precision in Modern Manufacturing Processes
Benefits of Customized Induction Heating Equipment
1. **Enhanced Efficiency**: Customized induction heating solutions negate the need for trial-and-error processes often required with generalized equipment. When machines are designed to meet specific operational needs, they operate more efficiently, reducing energy consumption and operational costs.
2. **Improved Precision**: Custom induction systems can be engineered to deliver precise heating profiles tailored to the requirements of specific materials and processes. This precision minimizes the risk of overheating or underheating materials, which can lead to defects in the finished products.
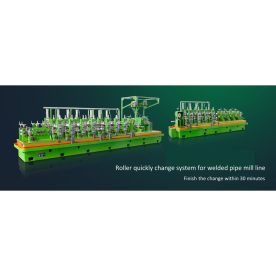
The Advantages of Customized Induction Heating Equipment for Enhanced Efficiency and Precision in Modern Manufacturing Processes
3. **Scalability**: As manufacturing needs change, the ability to scale production is crucial. Customized induction heating equipment can be designed with scalability in mind, allowing companies to adapt quickly to changing market demands or production volumes without a significant overhaul of their heating systems.
4. **Versatility**: Industries today require flexible solutions that can accommodate various materials and applications. Customized systems can be designed to handle different metals, such as aluminum, copper, or steel, and can be adapted for diverse applications, including brazing, annealing, and hardening.
5. **Reduced Operating Costs**: By optimizing the heating process and reducing energy consumption, customized induction heating equipment can lead to substantial reductions in operating costs. Furthermore, fewer defective products translate to lower waste and rework expenses.
6. **Integration with Existing Systems**: Customized induction heating equipment can be designed to seamlessly integrate with existing manufacturing systems. This adaptability allows industries to leverage modern technology without requiring a complete overhaul of their infrastructure.
Applications Across Industries
The versatility of customized induction heating equipment makes it useful across various industries. In the automotive sector, it can be used for processes such as hardening gears and bearings. The electronics industry benefits from induction heating for soldering components, ensuring perfect joints without damaging sensitive parts. In the medical field, customized induction heating systems can provide precise sterilization processes for surgical instruments.
Conclusion
The importance of customized induction heating equipment in modern manufacturing cannot be overstated. It represents a convergence of technology and innovation, driving improvements in efficiency, precision, and adaptability. As industries continue to face challenges related to energy consumption, production demands, and quality assurance, investing in customized solutions becomes an imperative. By embracing this technology, manufacturers can not only enhance their operational capabilities but also gain a competitive edge in an increasingly dynamic market. As the industry moves forward, it is clear that the future lies in tailored solutions that meet the specific needs of each application, paving the way for more effective and sustainable manufacturing practices.Customized Flying Saw Machine