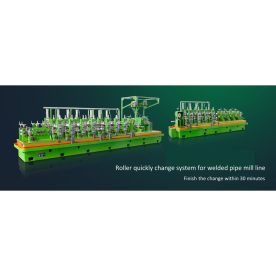
Enhancing Efficiency and Consistency: Understanding Pipe Mill Production Line with Quality Control Measures for Optimal Output
In the manufacturing industry, particularly in pipe production, the quality of the final product is non-negotiable. Pipe mill production lines are designed to efficiently produce various types of pipes, including those made from steel, plastic, and other materials. However, an effective production line is not solely dependent on the machinery or the raw materials used. It is equally reliant on the implementation of stringent quality control measures at every stage of the production process. This article delves into the intricacies of a pipe mill production line while highlighting the critical quality control measures that ensure optimal output and consistency.
Overview of Pipe Mill Production Line
A pipe mill production line consists of numerous processes that transform raw materials into finished pipe products. The primary stages of production include raw material preparation, forming, welding, heat treatment, and finishing. Each of these stages requires different equipment and procedures, and the personnel involved must maintain high levels of skill and attention to detail.
1. **Raw Material Preparation**: The process begins with sourcing high-quality materials. These materials are then inspected to ensure they meet the required specifications. Poor quality raw materials can lead to defects in the final product.
2. **Forming**: During the forming stage, the raw material is shaped into the desired pipe configuration. This can involve several methods such as extrusion, rolling, or stamping. Each method has its own set of parameters that must be adhered to ensure quality.
3. **Welding**: For many applications, especially in producing metal pipes, welding is a critical step. The seam formation should be monitored closely to prevent issues such as leaks or structural weaknesses.

Enhancing Efficiency and Consistency: Understanding Pipe Mill Production Line with Quality Control Measures for Optimal Output
4. **Heat Treatment**: This process alters the physical and sometimes chemical properties of the pipe through controlled heating and cooling, enhancing durability and strength. Quality control during this phase ensures that the heat treatment process does not lead to undesired outcomes, such as warping or weakening of the material.
5. **Finishing**: The final stage involves cleaning, coating, and inspecting the finished product. Proper finishing enhances corrosion resistance and protects the pipeline from environmental factors, thus prolonging its service life.
Quality Control Measures in Pipe Mill Production Line
Quality control in a pipe mill production line is not an afterthought; rather, it is an integral part of the production process. Effective quality control measures must be implemented at every stage of the production line to ensure that the final product meets the necessary industry standards.
1. **Material Inspection**: Quality begins with the selection of materials. A robust incoming inspection should analyze the mechanical properties and chemical composition of the raw materials using advanced testing techniques, such as spectrometry and tensile testing.
2. **Process Monitoring**: Continuous monitoring of the production process can help identify any irregularities. This involves the use of automated systems that track temperature, pressure, and other critical parameters. Deviations from the set standards should trigger immediate corrective actions.
3. **Welding Inspection**: Regular inspections should be conducted during the welding process to assess the integrity of the weld seams. Non-destructive testing methods, such as ultrasonic or radiography tests, can be used to detect internal flaws without damaging the pipes.
4. **Final Inspection**: After the finishing process, a comprehensive final inspection is necessary. This may include visual inspections, dimensional checks, and pressure testing. Each pipe must be tested to validate its conformity to specified standards and to ensure that it will perform satisfactorily in its intended application.
5. **Documentation and Traceability**: Quality control measures should include thorough documentation that tracks the production process from raw materials to finished products. This traceability is essential for accountability and can aid in any future quality investigations or recalls.
6. **Employee Training**: Employees working on the production line must be adequately trained in quality control standards. Consistent training programs help foster a quality-oriented culture within the organization, reinforcing the importance of maintaining high standards of production.
Conclusion
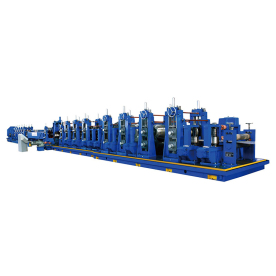
Enhancing Efficiency and Consistency: Understanding Pipe Mill Production Line with Quality Control Measures for Optimal Output
In a world where precision and quality are paramount, the role of quality control measures in a pipe mill production line cannot be understated. Implementing rigorous quality inspection processes and ensuring traceability at every stage not only helps in producing superior pipe products but also builds a reputation for reliability and excellence within the industry. As manufacturers continue to strive for efficiency and output, quality control should remain at the forefront, ensuring that products are not just made but made right.High frequency welder