In the welding industry, technology constantly evolves, leading to more efficient techniques and tools designed to improve the quality and speed of welds. Among these advancements, the shear and butt welder has emerged as a pivotal solution in various applications, ranging from manufacturing to construction. This article delves into the fundamentals of shear and butt welding, its benefits, applications, and future trends in this critical welding technique.
Understanding Shear and Butt Welding
Shear and butt welding is a specialized technique commonly used for joining metal parts. The process focuses on aligning two workpieces end-to-end and applying heat to create a solid bond between them. The shear aspect of this technique refers to the forces acting upon the welded parts during the heating and bonding process. The unique combination of heat application and pressure helps produce strong, uniform welds, crucial for structural integrity in construction and manufacturing.
Butt welding involves bringing the edges of two pieces of similar or dissimilar metals together and applying heat through resistance, making it a widely used technique in various industries, including automotive, aerospace, and construction. This method is particularly valuable in situations where a continuous line of weld is required or when the joint’s geometry demands a flush finish.
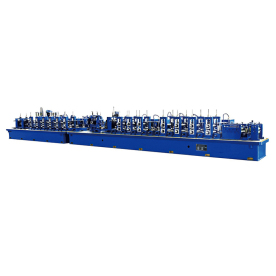
Exploring the Benefits and Applications of Shear & Butt Welders in Modern Welding Techniques for Efficiency and Precision
Advantages of Shear and Butt Welders
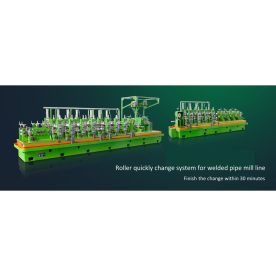
Exploring the Benefits and Applications of Shear & Butt Welders in Modern Welding Techniques for Efficiency and Precision
The shear and butt welder offers several significant advantages over other welding techniques:
1. **High Precision and Quality**: One of the foremost benefits of this welding method is its ability to produce highly precise and clean welds. The alignment of parts is critical, as precision is paramount in industries where safety and reliability are non-negotiable.
2. **Reduced Distortion**: Given the localized heating and quick cooling involved in the shear and butt welding process, there is less distortion compared to traditional welding methods. This is crucial for maintaining the integrity of the workpieces, especially in applications where exact dimensions are necessary.
3. **Versatility**: Shear and butt welders are compatible with a variety of materials, including steel, aluminum, and even some plastics. The versatility makes this technique applicable in numerous fields, facilitating the use of similar or dissimilar metals and materials.
4. **Efficiency and Speed**: With automated shear and butt welding systems, production rates increase significantly. The automation of this process reduces labor requirements and the time necessary to complete welding tasks, leading to cost savings and improved productivity.
5. **Fewer Defects and Waste**: The controlled nature of shear and butt welding minimizes defects and waste material, contributing to more sustainable manufacturing practices. As companies strive for greater environmental responsibility, adopting efficient welding practices is crucial for meeting these goals.
Applications of Shear and Butt Welders

Exploring the Benefits and Applications of Shear & Butt Welders in Modern Welding Techniques for Efficiency and Precision
The versatility of shear and butt welders has made them indispensable in various industries:
– **Automotive**: In the automotive sector, shear and butt welding is often used to join structural components and chassis parts, ensuring strength and safety in vehicle construction.
– **Aerospace**: The aerospace industry requires extremely precise welds for components such as fuel tanks and airframes. The shear and butt welding process caters to this need by providing durable and lightweight joints.
– **Construction**: In structural steel fabrication, shear and butt welding is critical for ensuring that steel beams and columns maintain their integrity and stability under load.
– **Manufacturing**: Various manufacturing processes utilize shear and butt welders for tasks ranging from joining pipelines to fabricating components for machinery, showcasing the technique’s adaptability.
Future Trends in Shear and Butt Welding Technology
As technology continues to progress, the future of shear and butt welders looks promising. Emerging trends include:
– **Automation and Robotics**: Increasing automation through robotics will further enhance the speed and precision of shear and butt welding, making it ideal for high-volume production environments.
– **Advanced Materials**: As more advanced materials are developed, shear and butt welders are expected to evolve to accommodate these substances, broadening the scope of potential applications.
– **Smart Welding Solutions**: The integration of IoT and smart technology in welding systems could lead to real-time monitoring and adjustments during the welding process, ensuring optimal results and even more efficient production.
In conclusion, shear and butt welders play a vital role in modern welding practices, offering superior efficiency, precision, and versatility across various industries. As technology advances, the importance and application of these welders are likely to expand, solidifying their position at the forefront of welding innovation.Portable high frequency welder