In the realm of metalworking, the efficiency and performance of machinery play a crucial role in determining the quality of the finished product. Cold cutting saw machines, renowned for their precision and ability to create clean cuts without generating excess heat, are indispensable in various industries including manufacturing, construction, and automotive. To maintain optimal performance, it is essential to regularly inspect and, if necessary, replace various components within these machines, referred to as replacement parts. This article delves into the importance of cold cutting saw machine replacement parts, the most common components that require replacement, and how to ensure a seamless process to enhance productivity and longevity.
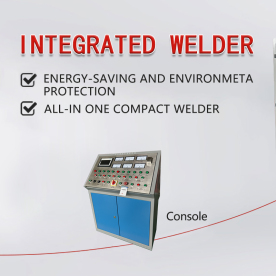
Essential Guide to Cold Cutting Saw Machine Replacement Parts: Ensuring Efficiency and Longevity in Metalworking Operations
Understanding Cold Cutting Saw Machines
Cold cutting saw machines utilize a high-speed rotating blade to cut through metal, plastic, and other materials without producing significant heat. Unlike traditional sawing methods that create friction and heat, cold cutting minimizes thermal distortion and warping, which is critical for applications requiring precision. As industries place a premium on accuracy and repeatability, these machines have become standard in many settings. However, like all machines, they are subject to wear and tear over time, necessitating an understanding of their replacement parts.
Importance of Replacement Parts
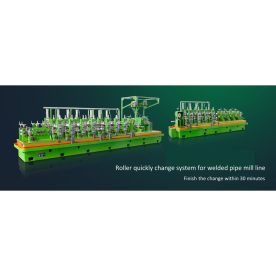
Essential Guide to Cold Cutting Saw Machine Replacement Parts: Ensuring Efficiency and Longevity in Metalworking Operations
The longevity of a cold cutting saw machine depends significantly on the condition of its parts. Regular replacement of worn components not only prolongs machine life but also ensures that production remains uninterrupted and efficient. Using sub-par or damaged components can lead to inaccuracies in cuts, increased waste, and even equipment failure, which can result in costly downtime and repairs. Therefore, investing in high-quality replacement parts is essential for optimal performance and safety in any metalworking operation.
Common Replacement Parts for Cold Cutting Saw Machines
1. **Blades**: The most critical component of a cold cutting saw machine is undoubtedly the blade. Over time, blades can experience dulling, chipping, or cracking. It is vital to replace the blade once its cutting efficiency starts to decline, as this can significantly impact the quality of the cuts and the speed of operation. Selection should be based on the material being cut and the desired finish.
2. **Drive Belts**: Drive belts are responsible for transferring power from the motor to the blade. Over time, these belts can wear out or become damaged, leading to a loss of power and efficiency. Inspecting and replacing drive belts regularly ensures a smooth operation, maximizing the machine’s performance.
3. **Bearings**: Bearings allow smooth rotation of the blade and are critical for maintaining precision cuts. Worn-out bearings can lead to vibrations and inaccuracies, significantly affecting the quality of work. Regular inspection and timely replacement of bearings can prevent costly downstream issues.
4. **Hydraulic Components**: For cold cutting saws that utilize hydraulic systems to assist in blade movement, it is crucial to monitor the performance of hydraulic components. Cylinders, hoses, and pumps can wear out or develop leaks over time, which can hinder the efficiency of cutting operations. Replacing these parts as needed will ensure consistent performance and reliability.

Essential Guide to Cold Cutting Saw Machine Replacement Parts: Ensuring Efficiency and Longevity in Metalworking Operations
5. **Electrical Components**: Cold cutting saw machines often include various electrical components, such as motors and sensors. As with mechanical parts, electrical components can fail due to age, overheating, or wear. Regular maintenance checks can identify faulty parts, allowing for prompt replacement before they cause significant disruption to operations.
Best Practices for Replacement Parts Maintenance
1. **Scheduled Inspections**: Establish a routine maintenance schedule to inspect all components regularly. This proactive approach helps identify wear and tear before they result in failure.
2. **Use OEM Parts**: When replacing components, always opt for Original Equipment Manufacturer (OEM) parts. OEM parts guarantee compatibility and reliability, ensuring the longevity of your cold cutting saw machine.
3. **Proper Training**: Ensure that your team is properly trained in the maintenance and operation of cold cutting saw machines. Knowledgeable staff can perform regular checks and recognize early signs of wear.
4. **Keep Records**: Maintain detailed records of maintenance activities and replacements. This information can provide insights into recurring issues and help plan for future replacements.
Conclusion
Cold cutting saw machines are powerful tools that, when maintained properly, can deliver exceptional precision and efficiency in metalworking. Understanding the importance of cold cutting saw machine replacement parts and adhering to best practices in maintenance can significantly impact productivity and machine longevity. By investing in high-quality replacement components and nurturing a culture of regular inspections and training, businesses can ensure their cold cutting saw machines remain in top working condition, ultimately contributing to greater operational success.Stainless Steel Pipe making machine