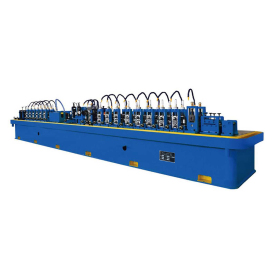
Exploring the Advancements in Tube Manufacturing: How Advanced Tube Making Machinery is Revolutionizing the Industry
In an era defined by rapid technological advancements, industries are continually evolving to meet the demands of a dynamic marketplace. One area that has seen significant innovation is tube manufacturing, a critical component in numerous applications, from aerospace to construction. At the forefront of this evolution is advanced tube making machinery, which is transforming the way manufacturers produce high-quality tubes and pipes. This article delves into the various technologies and techniques that underpin advanced tube making machinery, the benefits this machinery offers, and its impact on the manufacturing landscape.
The tube manufacturing sector has traditionally relied on steep learning curves, manual labor, and outdated machinery, which often culminated in inefficiencies and higher production costs. However, the advent of advanced tube making machinery has ushered in a new era of efficiency and precision. With integrated automation, enhanced control systems, and cutting-edge materials, this machinery is capable of producing a wide array of tubes, from standard to highly customized designs, with remarkable speed and accuracy.
One of the most significant advancements in tube manufacturing is the incorporation of computer numerical control (CNC) technology. CNC machines enable precise manipulation of the tube forming process, allowing for intricate shapes and specifications to be met with consistent excellence. This level of automation not only reduces the likelihood of human error but also significantly enhances production speed. With the ability to program complex designs directly into the machinery, manufacturers can easily switch between different tube specifications without extensive downtime, leading to a leaner manufacturing process.
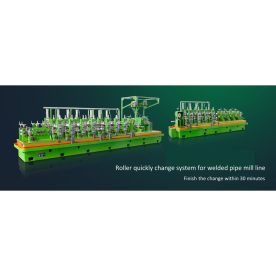
Exploring the Advancements in Tube Manufacturing: How Advanced Tube Making Machinery is Revolutionizing the Industry
Another pivotal development in advanced tube making machinery is the emergence of laser cutting and welding technologies. Laser systems offer unparalleled precision when it comes to cutting tubes to exact specifications. Traditional cutting methods often result in burrs and deformations that compromise the integrity of the tube. In contrast, laser cutting minimizes waste and dramatically enhances the overall quality of the finished product. Furthermore, these systems can seamlessly integrate with advanced welding technologies, ensuring perfect joins with minimal heat input, which is crucial for maintaining the strength and stability of the tubes.

Exploring the Advancements in Tube Manufacturing: How Advanced Tube Making Machinery is Revolutionizing the Industry
The role of material advancements cannot be overlooked in the evolution of tube manufacturing. Modern advanced tube making machinery is designed to work with various materials such as high-strength alloys, lightweight composites, and other specialized metals. These materials often require bespoke handling and processing techniques, which advanced machinery is equipped to manage. Consequently, manufacturers are not only able to produce traditional steel tubes but can also explore innovative materials that meet specific performance criteria in industries such as oil and gas, automotive, and construction.
Moreover, the push for sustainability in manufacturing practices is gaining momentum, and advanced tube making machinery plays a vital role in this movement. Manufacturers increasingly turn to machinery that optimizes energy consumption and minimizes waste. Many advanced systems incorporate energy-efficient components that lower the overall carbon footprint of the production process. Additionally, with the ability to recycle leftover materials more effectively, manufacturers can significantly reduce scrap waste, aligning their operations with global sustainability goals.
Quality control is another area significantly enhanced by advanced tube making machinery. Many modern systems are integrated with sophisticated monitoring technology that continually assesses product quality throughout the manufacturing process. This real-time feedback loop allows manufacturers to rectify any defects as they arise, ensuring that the final products meet stringent standards.
In conclusion, advanced tube making machinery is revolutionizing the tube manufacturing industry in myriad ways. From CNC technology and laser cutting to breakthroughs in materials and sustainability, these systems are redefining efficiency and quality standards. As manufacturers continue to embrace these technologies, the future of tube production is not only promising in terms of innovation and capability but is also poised to meet the growing demands of a global market that increasingly values precision, adaptability, and sustainability. As the industry evolves, those who harness the power of advanced tube making machinery will undoubtedly secure a competitive edge in an ever-changing landscape.Cold Cutting Saw Machine Replacement Parts