In the ever-evolving landscape of manufacturing technology, the demand for precise, efficient, and versatile machinery has never been higher. One standout piece of equipment that has significantly transformed the tube manufacturing process is the tube making machine with cutting function. This advanced machine not only streamlines operations but also ensures accuracy and consistency across a wide range of applications. In this article, we will delve into the importance of tube making machines equipped with cutting functions, their operational features, advantages, and how they are shaping modern manufacturing practices.
Understanding Tube Making Machines
Tube making machines are specialized equipment designed to create tubes and pipes from various materials, including metal, plastic, and composite materials. These machines play a vital role in numerous industries, such as automotive, construction, electronics, and furniture. The primary process involved in tube manufacturing includes shaping raw materials into tube forms through methods like extrusion, welding, or rolling, followed by cutting to the required lengths.
The Role of Cutting Functionality
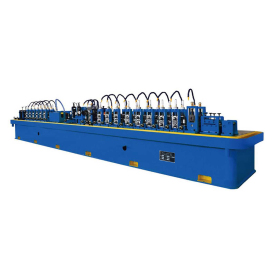
Exploring the Innovations and Benefits of Tube Making Machines with Cutting Function for Enhanced Manufacturing Efficiency
The cutting function in a tube making machine is a crucial feature that enhances its versatility and efficiency. This function allows manufacturers to produce tubes of various lengths and specifications, catering to different industry requirements. Typically, this cutting feature can be integrated into the tube making machine in several ways, including guillotine-style cuts, rotary cutting, or laser cutting technology, depending on the material being processed.
Key Features of Tube Making Machines with Cutting Function
1. **Precision Engineering**: Tube making machines with cutting functions are designed to ensure high precision. Advanced control systems and sensors maintain the correct length for each tube, reducing waste and increasing production yield.
2. **Speed and Efficiency**: These machines are engineered for high-speed operations, allowing manufacturers to increase output without sacrificing quality. The integrated cutting function further streamlines the workflow by performing multiple operations in a single pass.
3. **Flexibility in Production**: Modern tube making machines are highly adaptable, enabling manufacturers to switch between various sizes and types of tubes quickly. This flexibility is essential for businesses looking to meet diverse customer needs without incurring significant downtime.
4. **Automation**: Many tube making machines are now equipped with automation capabilities, enabling minimal operator intervention. This automation leads to reduced labor costs and further enhances production efficiency.
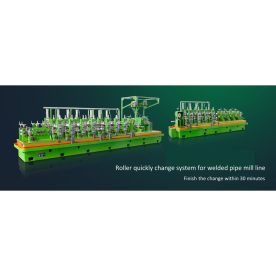
Exploring the Innovations and Benefits of Tube Making Machines with Cutting Function for Enhanced Manufacturing Efficiency
5. **Integration with Digital Technologies**: The rise of Industry 4.0 has seen many tube making machines incorporate IoT and data analytics. This connectivity allows manufacturers to monitor production, manage maintenance schedules, and optimize performance in real-time.
Benefits to Manufacturers
Investing in a tube making machine with a cutting function presents numerous advantages for manufacturing businesses:
– **Cost Reduction**: By minimizing material waste and improving production efficiency, manufacturers can significantly reduce their operating costs. The precision cutting ensures that only the necessary lengths are produced, minimizing offcuts.
– **Improved Quality Control**: Consistency in tube dimensions is vital, particularly in industries requiring precise specifications. The cutting function helps maintain quality standards, ensuring that the end products meet industry regulations and client expectations.
– **Enhanced Productivity**: With the ability to produce various tube lengths and types in a single machine, manufacturers can respond rapidly to market demands, thus enhancing overall productivity.
– **Reduced Lead Times**: Faster setup and production times mean companies can fulfill orders more quickly, giving them a competitive edge in the marketplace.

Exploring the Innovations and Benefits of Tube Making Machines with Cutting Function for Enhanced Manufacturing Efficiency
Conclusion
In conclusion, the tube making machine with cutting function is an essential tool for modern manufacturing, offering enhanced precision, efficiency, and flexibility. As technology continues to advance, these machines are likely to incorporate even more innovative features, further solidifying their role in the production process. For manufacturers looking to stay competitive in an ever-changing market, investing in a state-of-the-art tube making machine with cutting capability is a prudent decision that can lead to significant operational benefits and improved product quality. The future of tube manufacturing lies in embracing such advancements, ensuring sustainability, and meeting the diverse needs of a growing industry.High frequency welder