In the modern manufacturing landscape, precision and efficiency are paramount. Industries ranging from automotive to aerospace require components that are not only accurate in their dimensions but also produced at a rapid pace. One of the key technologies driving this commitment to quality and efficiency is the **Automatic Cold Cutting Saw Machine**. These machines have transformed the way manufacturers handle metal and other materials, ensuring a perfect cut every time while also optimizing productivity.
Understanding Automatic Cold Cutting Saw Machines
Automatic cold cutting saw machines are designed for cutting various materials, including steel, aluminum, and plastics, using a circular saw blade. Unlike traditional cutting methods, which may involve heat-generating processes such as sawing or grinding, cold cutting sees minimal thermal distortion, leading to better surface quality and the integrity of the material. The non-heated cutting process makes these machines ideal for applications where precision is critical.
The automatic features of these saws often include advanced computer numerical control (CNC) systems, which allow for automated programming, automation of the cutting process, and significantly reduce human intervention. This technology not only increases cutting speed but also enhances accuracy, ensuring that dimensions remain consistent across production runs.
Benefits of Utilizing Automatic Cold Cutting Saw Machines
1. **Precision and Accuracy**: One of the primary benefits of using an automatic cold cutting saw machine is the level of precision it provides. The CNC technology ensures that each cut is exact, reducing the instances of waste materials and rework, which can significantly impact production costs.
2. **Speed and Efficiency**: Automatic cold cutting saw machines are designed for high throughput. They can work continuously without the need for constant manual adjustments, which means manufacturers can scale their production processes and meet increased demand without sacrificing quality.
3. **Material Preservation**: Because these machines operate at lower temperatures, they minimize the thermal deformation often associated with conventional cutting methods. This quality preserves the physical properties of the materials, ensuring that they maintain their strength and structural integrity post-cutting.
4. **Reduced Labor Costs**: Automation reduces the need for a large workforce, as the machines can handle the bulk of the work independently. This shift not only lowers labor costs but also shifts the focus toward skilled oversight rather than manual labor.
5. **Versatility in Applications**: Automatic cold cutting saw machines can be used for a wide range of applications, from machining to automotive parts fabrication. Their adaptability makes them invaluable across various sectors, allowing businesses to diversify their offerings.
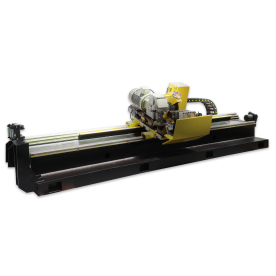
Revolutionizing Precision Cutting in Manufacturing: The Role of Automatic Cold Cutting Saw Machines in Modern Industry
6. **Safety and Ergonomics**: Modern machines come equipped with features that enhance safety, such as guarded blades and automatic shut-off mechanisms. Additionally, as the machines handle the heavy lifting and cutting, it alleviates strain on workers, promoting better ergonomics and reducing workplace injuries.
Integrating Automatic Cold Cutting Saw Machines into Manufacturing
For manufacturers looking to adopt automatic cold cutting saw machines, integration into existing workflows can be streamlined. Here are some steps to consider:
1. **Conduct a Needs Assessment**: Evaluate your current production methods to determine the specific requirements for automated cold cutting. Consider factors such as material types, sizes, and cutting demands.
2. **Select the Right Equipment**: Based on your assessment, research various models and features of cold cutting saw machines. Look for options that provide the necessary precision, speed, and compatibility with your existing machinery.
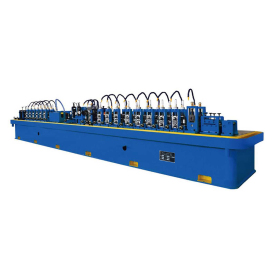
Revolutionizing Precision Cutting in Manufacturing: The Role of Automatic Cold Cutting Saw Machines in Modern Industry
3. **Train Your Workforce**: Investing in technology is a critical step, but it’s equally important to ensure your workforce is well-trained. Staff should understand how to operate the machines safely and maintain them adequately.
4. **Monitor and Optimize Performance**: After installation, continuously monitor the performance of your automatic cold cutting saw machines. Use data analytics to identify areas for improvement, ensuring you are maximizing efficiency and reducing waste.
Conclusion
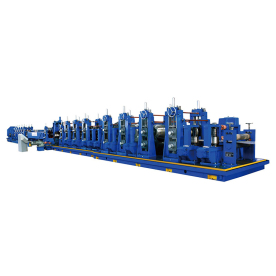
Revolutionizing Precision Cutting in Manufacturing: The Role of Automatic Cold Cutting Saw Machines in Modern Industry
The advent of the **Automatic Cold Cutting Saw Machine** marks a significant advancement in the manufacturing sector. By delivering unmatched precision, speed, and efficiency, these machines are reshaping the standards of production. As industries continue to evolve, embracing this innovative technology will be essential for businesses aiming to remain competitive in an increasingly demanding marketplace. By investing in automatic cold cutting saw machines, manufacturers not only improve their cutting processes but also enhance their overall operational capabilities, paving the way for a more productive and sustainable future.Precision Cold Cutting Saw Machine