Induction heating is rapidly emerging as one of the most effective and efficient methods for heating metals and other conductive materials in various industrial applications. Precision induction heating equipment is at the forefront of this transformative technology, providing manufacturers with the ability to enhance productivity, minimize energy consumption, and improve product quality. This article aims to explore the key features, advantages, and diverse applications of precision induction heating equipment in modern manufacturing processes.
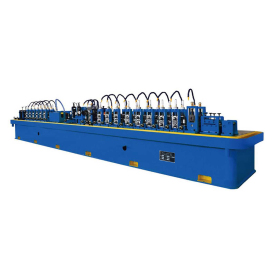
Understanding the Benefits and Applications of Precision Induction Heating Equipment for Modern Manufacturing Processes
At its core, precision induction heating relies on electromagnetic induction to generate heat in a workpiece without direct contact. This process occurs when an alternating current flows through a coil, creating a magnetic field that induces eddy currents in the material. The resistance of the workpiece to these currents produces heat, allowing for targeted and rapid heating. The level of precision and control offered by this technology has made it a favored choice in many sectors, including automotive, aerospace, electronics, and metalworking.
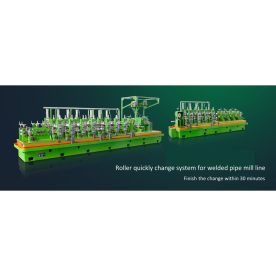
Understanding the Benefits and Applications of Precision Induction Heating Equipment for Modern Manufacturing Processes
One of the primary advantages of precision induction heating equipment is its ability to deliver heat in a controlled manner. Unlike traditional heating methods, which can result in uneven heating and overheating of materials, precision induction equipment allows for exact temperature control. This precision is crucial in processes like hardening, where achieving specific temperatures is essential for ensuring desired material properties. Notably, the speed and rate of heating can significantly affect the mechanical properties of metals, making precision control indispensable.
Efficiency is another significant benefit of induction heating. Manufacturers are under constant pressure to reduce energy costs and improve sustainability. Traditional heating methods often result in considerable energy loss and longer heating times. Precision induction heating equipment, however, provides a highly efficient method of heating. Most of the energy used is converted directly into heat in the workpiece, which leads to shorter cycle times and reduced energy consumption. This efficiency not only lowers operational costs but also contributes to a smaller carbon footprint, helping businesses meet environmental regulations and sustainability goals.
In addition to its efficiency and precision, precision induction heating equipment is also highly versatile. It can be applied to a wide range of processes, including but not limited to hardening, annealing, brazing, soldering, and melting. This versatility makes it an attractive option for manufacturers looking to streamline their operations. With suitable induction heating equipment, facilities can switch between various applications without needing substantial changes to their setup. This adaptability is especially beneficial in the current manufacturing climate, which often demands agile production processes.
The integration of advanced technologies further enhances the capabilities of precision induction heating equipment. Many systems now come equipped with state-of-the-art control and monitoring systems that provide real-time feedback on various parameters, including temperature, power, and coil performance. These features enable manufacturers to optimize their processes, track performance, and respond quickly to any irregularities. Furthermore, the digital transformation of manufacturing involves data collection and analysis, helping facilities implement predictive maintenance strategies and further improve reliability.
Safety is also a critical consideration in any manufacturing setting, and induction heating equipment excels in this area. Because the heat is generated within the workpiece, the external equipment remains cool to the touch. This characteristic reduces the risk of burns and minimizes heat-related workplace accidents, creating a safer environment for operators. Additionally, enclosed systems can further protect users from exposure to high temperatures or other hazards associated with heating processes.
As industries continue to evolve and technology advances, precision induction heating equipment will undoubtedly play a pivotal role in the future of manufacturing. The demand for high-quality products, combined with cost pressures and sustainability goals, makes efficient and effective heating solutions more essential than ever. For manufacturers seeking to stay competitive in an ever-changing market, investing in precision induction heating technology is not merely an option; it is a strategic necessity.

Understanding the Benefits and Applications of Precision Induction Heating Equipment for Modern Manufacturing Processes
In conclusion, precision induction heating equipment represents a paradigm shift in how materials are heated in manufacturing processes. Its precision, efficiency, versatility, and safety features offer distinct advantages that align with the needs of modern industries. As the manufacturing landscape becomes ever more demanding, the integration of such advanced heating solutions will continue to drive innovation and productivity across various sectors.Cost-Effective Spare Parts for Cold Cutting Saws