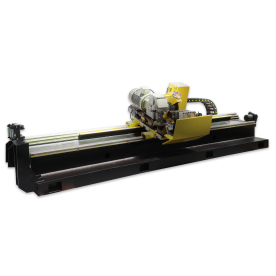
Exploring the Unmatched Versatility and Efficiency of the Automatic All-in-one High Frequency Welder for Modern Manufacturing Applications
****
In an age where technological innovation is paramount in manufacturing, the demand for efficient and reliable welding solutions continues to rise. One of the standout pieces of equipment that has revolutionized the welding industry is the Automatic All-in-one High Frequency Welder. This advanced machinery not only streamlines the welding process but also enhances the quality of welds across various applications. In this article, we will delve into the features, benefits, and various applications of the Automatic All-in-one High Frequency Welder, illustrating why it is becoming an essential component in manufacturing environments.

Exploring the Unmatched Versatility and Efficiency of the Automatic All-in-one High Frequency Welder for Modern Manufacturing Applications
**Understanding High Frequency Welding**
High-frequency welding, also known as dielectric welding, involves the use of high-frequency electromagnetic waves to generate heat in the materials being welded. This method is particularly effective for thermoplastics and certain metals, enabling a strong bond at the molecular level without significantly affecting the surrounding material. The Automatic All-in-one High Frequency Welder is designed to harness these principles, providing manufacturers with a powerful tool for creating precise and durable welds.
**Key Features of the Automatic All-in-one High Frequency Welder**
1. **Versatility:** One of the most compelling features of this welder is its versatility. It can handle a range of materials, including PVC, PU, EVA, and even some metals, making it ideal for a variety of applications. From clothing and accessories to automotive parts and industrial applications, this welder can accommodate numerous needs.
2. **User-Friendly Interface:** The Automatic All-in-one High Frequency Welder comes equipped with an intuitive interface that allows operators to set parameters quickly and efficiently. This feature minimizes training time and maximizes productivity, as users can easily adjust settings for different materials and thicknesses.
3. **High Efficiency:** This machine is engineered for high-speed operation, significantly reducing production time. With the ability to generate heat quickly and consistently, the Automatic All-in-one High Frequency Welder ensures that projects are completed on schedule without compromising on quality.
4. **Energy Savings:** Compared to traditional welding methods, the Automatic All-in-one High Frequency Welder is more energy-efficient. Its design minimizes heat loss, allowing manufacturers to reduce operational costs and make environmentally conscious choices.
5. **Precision Control:** One of the standout characteristics of this welder is its ability to control parameters like pressure, frequency, and time with exceptional precision. This capability ensures consistent weld quality, reducing the chances of defects and rework.
**Benefits of Using the Automatic All-in-one High Frequency Welder**
The advantages of implementing the Automatic All-in-one High Frequency Welder in production lines are numerous. For starters, manufacturers can expect a significant improvement in productivity levels. The speed and efficiency of this equipment allow for more pieces to be welded in less time, leading to enhanced throughput.
Moreover, the consistency and reliability of welds produced by this machine enhance product quality, which, in turn, boosts customer satisfaction and brand reputation. A reliable welding process minimizes defects and ensures that products meet or exceed quality standards, translating to fewer returns and higher profitability.
Another significant benefit is the capacity for process automation. In a time when labor shortages are increasingly common, having a machine capable of performing welding tasks automatically allows manufacturers to maintain productivity without the need for excessive manual labor.
**Applications Across Industries**
The Automatic All-in-one High Frequency Welder is applied in numerous sectors, including:
– **Textile and Leather Goods:** Ideal for welding synthetic textiles, this machine is essential for manufacturing bags, coats, and footwear. – **Automotive:** Used for producing various components, such as airbag systems and vinyl upholstery, it meets the industry’s stringent quality requirements. – **Medical Devices:** It plays a crucial role in assembling high-quality medical bags and other disposable products that demand sterilization and reliability. – **Plastic Manufacturing:** The welder is instrumental in creating specialized plastic components across multiple industries, ensuring strong, consistent bonds.
**Conclusion**
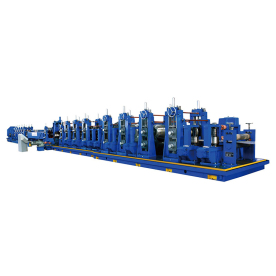
Exploring the Unmatched Versatility and Efficiency of the Automatic All-in-one High Frequency Welder for Modern Manufacturing Applications
In conclusion, the Automatic All-in-one High Frequency Welder stands out as a vital asset in modern manufacturing. By combining versatility, efficiency, and precision, it empowers industries to meet the growing demands for high-quality welded products. As manufacturers continue to seek solutions that optimize productivity while minimizing costs, the Automatic All-in-one High Frequency Welder is undeniably a pivotal tool in achieving these goals. Embracing this technology could very well be the key to fostering innovation and driving growth in today’s competitive market landscape.All-in-one High Frequency Welder with Adjustable Power