****
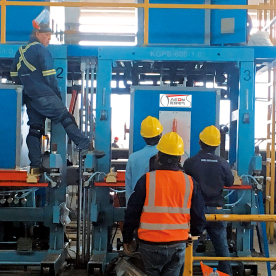
Understanding the Stainless Steel Pipe Mill Production Line: A Comprehensive Guide to the Manufacturing Process and Equipment
The stainless steel pipe mill production line is a sophisticated system designed for the efficient manufacturing of stainless steel pipes widely used in various industries, including construction, automotive, and food processing. This production line involves multiple stages, each critical to ensuring the final product’s quality, durability, and compliance with industry standards. In this article, we will explore the components, processes, and significance of stainless steel pipe mill production lines in modern manufacturing.
Components of a Stainless Steel Pipe Mill Production Line
A typical stainless steel pipe mill production line contains several essential components that work synergistically to produce high-quality pipes. These components include:
1. **Raw Material Input System**: The process begins with the sourcing of raw stainless steel strips or sheets. The selection of high-grade stainless steel is crucial, as it affects the finished product’s strength, corrosion resistance, and overall quality. The raw materials are typically delivered in coils and must be properly unwound before entering the production line.
2. **Slitting Machine**: Next, a slitting machine is used to cut the stainless steel coils into narrower strips. This step is necessary to prepare the material for subsequent processes, ensuring that the width corresponds to the specifications of the desired pipe dimensions.
3. **Forming Mill**: The forming mill is a pivotal component of the production line where the slitted strips are shaped into pipes. This is achieved through a series of rollers that gradually bend the material into a cylindrical form. Different types of mills, such as high-frequency induction welding mills, may be utilized depending on the requirements of the pipes being produced.
4. **Welding Station**: After the strips are formed into a tube shape, they undergo welding, commonly through high-frequency induction welding or TIG (Tungsten Inert Gas) welding. This process fuses the edges of the strips together to create a continuous pipe. The welding parameters must be meticulously controlled to ensure a strong and reliable weld seam without compromising the material’s integrity.
5. **Sizing and Calibration Equipment**: Once welded, the pipes must be sized accurately to meet specific dimensions. Sizing equipment, such as sizing mills and calipers, is employed to ensure that the outer diameter and wall thickness are consistent throughout the length of the pipe.
6. **Cooling System**: The welded pipes then pass through a cooling system, where they are rapidly cooled to ensure proper material properties and relieve any stress introduced during the welding process. This step is essential to enhance the structural integrity of the final product.
7. **Finishing Machinery**: Finally, the pipes undergo finishing processes, which may include cutting to length, surface polishing, and application of protective coatings. These finishing touches are crucial for aesthetics and further corrosion resistance, enhancing the product’s market appeal.
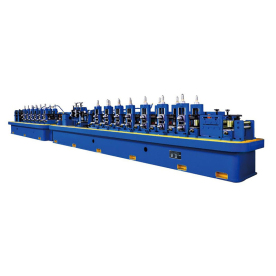
Understanding the Stainless Steel Pipe Mill Production Line: A Comprehensive Guide to the Manufacturing Process and Equipment
Importance of Stainless Steel Pipe Mill Production Lines
The efficient operation of stainless steel pipe mill production lines is paramount for several reasons:
1. **Quality Control**: Modern production lines are equipped with advanced monitoring systems that help maintain stringent quality control throughout the manufacturing process. This ensures that every pipe produced meets industry standards and customer requirements.
2. **Cost Efficiency**: By automating various stages of production, manufacturers can reduce labor costs and increase throughput. This leads to enhanced profit margins and the ability to offer competitive pricing to customers.
3. **Versatility**: The ability to produce a wide range of pipe sizes and types makes stainless steel pipe mill production lines incredibly versatile. Manufacturers can cater to diverse market needs, from small-diameter pipes used in plumbing applications to large-diameter pipes utilized in industrial and structural contexts.
4. **Sustainability**: Stainless steel is a highly recyclable material, and using a dedicated production line can promote sustainability within the manufacturing process. By optimizing the use of raw materials and focusing on reducing waste, manufacturers can contribute positively to the environment.
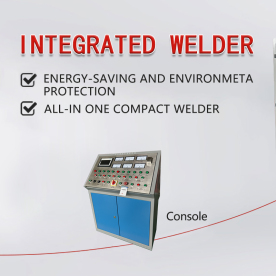
Understanding the Stainless Steel Pipe Mill Production Line: A Comprehensive Guide to the Manufacturing Process and Equipment
5. **Innovation and Advancement**: Continuous advancements in technology, such as automation and digital monitoring, allow for innovative enhancements to stainless steel pipe mill production lines. Manufacturers are constantly seeking new ways to improve efficiency, quality, and output.
Conclusion
In summary, the stainless steel pipe mill production line is a complex yet efficient system critical to producing high-quality stainless steel pipes. Each component of the production line plays a vital role in ensuring that the finished products meet stringent quality standards and customer expectations. With the growing demand for stainless steel pipes across various industries, understanding the intricacies of these production lines is essential for manufacturers and stakeholders alike. Embracing advancements in technology and sustainability will not only enhance production efficiency but also contribute to a more sustainable future in manufacturing.Durable HSS Blade for Metalworking