Induction heating is a powerful and efficient method of heating electrically conductive materials, which has gained significant traction in various industries due to its ability to provide fast, precise, and controlled heating. This technology operates based on electromagnetic induction, where an alternating current produces a magnetic field that induces currents within a conductive object, generating heat. With its growing relevance in the world of manufacturing and metal processing, induction heating stands out for its numerous benefits and applications.
One of the most notable advantages of induction heating is its efficiency. Unlike conventional heating methods that often utilize flames or resistive heating, which can waste energy and require significant time to reach desired temperatures, induction heating directly heats the workpiece without affecting the surrounding environment. This targeted approach minimizes heat loss, resulting in rapid temperature raises and reduced energy consumption. Industries are increasingly turning to induction heating systems, as they offer a viable solution for cost savings while being environmentally friendly.
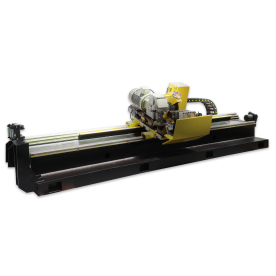
Exploring the Innovative Applications and Benefits of Induction Heating in Modern Manufacturing and Metal Processing Industries
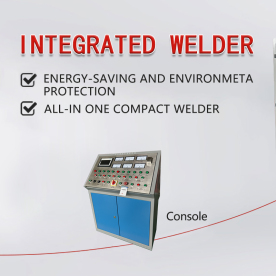
Exploring the Innovative Applications and Benefits of Induction Heating in Modern Manufacturing and Metal Processing Industries
The precision that induction heating provides is another significant benefit. In many manufacturing processes, including hardening, brazing, soldering, and annealing, exact control over temperature and heating time is crucial. Induction heating systems allow for real-time monitoring and adjustments, ensuring that the specific requirements for each process are met consistently. This level of control diminishes the risk of overheating or damaging the component, thereby enhancing the quality and integrity of the finished product.
In the automotive industry, for example, induction heating is employed extensively for tasks such as hardening steel components, which are critical for durability and performance. By using induction coils designed specifically for a part’s shape and size, manufacturers can achieve targeted heating that enhances the material properties of automotive components, prolonging their operational lifespan.
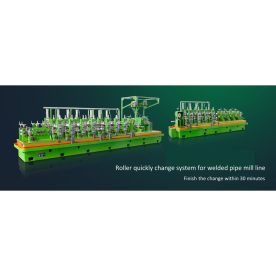
Exploring the Innovative Applications and Benefits of Induction Heating in Modern Manufacturing and Metal Processing Industries
Induction heating’s versatility is also worth noting. The technology can be adapted for a broad spectrum of applications across various sectors. In metal processing, induction heating is used for applications like forging, melting, and casting metals, ensuring that manufacturers can meet diverse production demands effectively. Furthermore, induction is not limited to metals; it is increasingly being harnessed for other materials, such as plastics and composites, expanding its utility in different manufacturing scenarios.
The compact nature of induction heating equipment enhances its appeal, especially in space-constrained environments. Unlike traditional furnaces that may require significant floor space and infrastructure, induction heating units can often be integrated seamlessly into existing manufacturing setups. This space efficiency combined with the reduction in energy costs and time enhances operational efficiency and productivity, making induction heating an attractive option for modernization in various manufacturing sectors.
Another area in which induction heating excels is safety. Since the heat is generated within the material itself, there are reduced risks of burns and accidents associated with open flames or heated surfaces. This characteristic makes workplaces safer for operators and aligns with modern safety standards and regulations. Furthermore, induction heating systems can be designed with advanced safety features, including automatic shut-offs and precise temperature controls, providing peace of mind for manufacturers.
Looking forward, the future of induction heating appears promising. The increasing demand for energy-efficient and environmentally sustainable production methods continues to drive innovation in induction heating technologies. Ongoing research and development efforts focus on enhanced coil designs, advanced power supply systems, and integration with automation technologies like robotics and smart manufacturing systems. With the rise of Industry 4.0, induction heating is set to play a pivotal role in driving efficiency and innovation in manufacturing processes.
In conclusion, induction heating presents a multitude of benefits, including efficiency, precision, versatility, space savings, and enhanced safety. Its applications span various industries, particularly in metal processing and manufacturing where high-quality heating is essential. As technology continues to evolve, induction heating’s role is poised to expand even further, solidifying it as a key player in modern industrial landscapes. And as companies increasingly prioritize sustainable practices, induction heating not only meets current manufacturing demands but stands as a forward-thinking solution for the future.Woodworking Flying Saw Machine