In an era where precision manufacturing and customization are paramount, industries are increasingly turning towards tailored solutions to improve their production processes. Among these, customized pipe mill production line solutions stand out as a crucial element in meeting the diverse demands of the global market. It’s not merely about creating pipes; it’s about crafting a manufacturing system that aligns perfectly with the specific requirements of your operation. This article explores the essence, benefits, and elements of customized pipe mill production line solutions, highlighting how they contribute to increased efficiency and enhanced product quality.
Understanding Customized Pipe Mill Production Line Solutions
At its core, a pipe mill production line is a set of machinery and processes designed to fabricate pipes from various materials. These systems can produce pipes for a wide array of applications, including but not limited to oil and gas, water supply, and construction. However, a one-size-fits-all approach often falls short in meeting the varied specifications and quality standards required by different industries. This is where customized solutions play a pivotal role.
Customized pipe mill production line solutions consider the unique demands of each client, from the types of materials used to the specific dimensions and properties required for the final product. Such tailored solutions encompass everything from advanced design and engineering to integration and optimization of production processes.
Benefits of Customized Pipe Mill Production Line Solutions
1. **Enhanced Flexibility**: One of the primary advantages of customized production lines is their ability to adapt to changing market demands. Businesses can scale their production up or down based on the current requirements without overhauling the entire system. This flexibility is essential in today’s fast-paced manufacturing environment.
2. **Improved Efficiency**: Tailored systems are designed to minimize waste and maximize output. By optimizing each stage of the production process, companies can significantly reduce manufacturing times and costs. Custom solutions allow manufacturers to implement advanced technologies such as automation, which further enhances production efficiency.
3. **Increased Quality Control**: Implementation of customized solutions ensures that each production line meets the highest quality standards specific to the industry. Tailored machinery and processes can be designed to incorporate quality checks at each stage of production, ensuring that the final product meets or exceeds customer expectations.
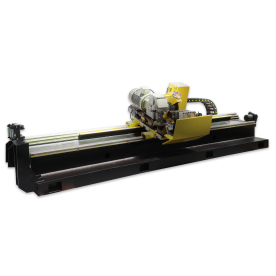
Innovative Customized Pipe Mill Production Line Solutions: A Comprehensive Guide to Optimize Manufacturing Efficiency and Product Quality
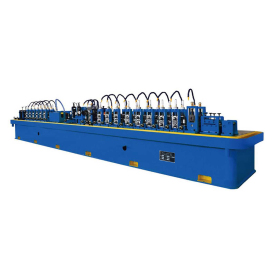
Innovative Customized Pipe Mill Production Line Solutions: A Comprehensive Guide to Optimize Manufacturing Efficiency and Product Quality
4. **Cost-Effectiveness**: While the initial investment in a customized pipe mill production line may be higher than that of standard systems, the long-term savings often outweigh these initial costs. Efficient operations lead to lower production costs, reduced scrap rates, and optimal resource utilization. Furthermore, the ability to produce pipe products that fully meet market specifications often results in higher sales margins.
5. **Integration of Advanced Technologies**: Customized solutions are not just about the machines; they often incorporate the latest technology, including digital controls, IoT integration, and real-time monitoring systems. These advancements allow manufacturers to collect valuable data, enabling continual optimization of the production process.
Components of Customized Pipe Mill Production Line Solutions
When designing a customized pipe mill production line, several critical components must be considered to ensure a seamless operation. These include:
1. **Material Handling Systems**: Efficient handling and movement of raw materials are essential in any production line. Customized systems can significantly reduce downtime and improve the ergonomics of material handling.
2. **Forming and Welding Machines**: The core of any pipe mill production line, these machines should be tailored to the specific types of pipes being produced, whether they are welded, seamless, or otherwise.
3. **Heat Treatment Chambers**: Depending on the required properties of the final product, heat treatment processes can be customized for precision and efficiency.
4. **Finishing Equipment**: Customizing tools and machines that handle the finishing of pipes ensures that each piece meets the stringent quality and aesthetic standards.
5. **Quality Assurance Instruments**: Incorporating advanced quality control metrics ensures that the pipes produced consistently meet specifications.
Conclusion
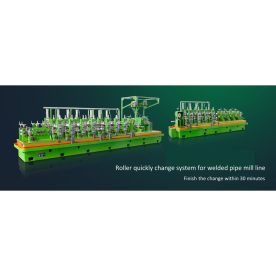
Innovative Customized Pipe Mill Production Line Solutions: A Comprehensive Guide to Optimize Manufacturing Efficiency and Product Quality
Customized pipe mill production line solutions represent a significant advancement in the manufacturing sector, allowing businesses to align their production capabilities with market demands. Through enhancing flexibility, improving efficiency, and ensuring top-notch quality control, these tailored systems not only meet the needs of diverse industries but also empower manufacturers to excel in competitive markets. As technological advancements continue to evolve, investing in customized solutions will remain a key strategy for companies aiming to improve their operational efficiency and product standards.Tube making machine with cutting function