Solid-state high-frequency (HF) welders have revolutionized the welding industry with their efficiency and precision. These devices rely on advanced technology to deliver reliable results across various applications, making them indispensable in sectors ranging from automotive to electronics. However, like any sophisticated machinery, solid-state HF welders require regular maintenance and, occasionally, replacement of spare parts to ensure peak performance. In this article, we will explore the essential spare parts for solid-state HF welders, their importance, how to select the right components, and best practices for maintenance.
Importance of Spare Parts in Solid State HF Welders
The effectiveness of a solid-state HF welder hinges on the functionality of its components. Each part works in harmony with the others to ensure efficient energy transfer and heat generation necessary for welding. When a component malfunctions, it can lead to suboptimal welding quality, increased downtime, and additional repair costs. This makes it crucial to have easy access to quality spare parts.
Maintaining a stock of spare parts means you can minimize downtime when issues arise. For businesses, even an hour of non-operational machinery can result in significant financial losses. Immediate access to critical components such as capacitors, transformers, diodes, and other parts can help maintain workflow and productivity.
Key Spare Parts for Solid State HF Welders
1. **Capacitors**: These are essential for energy storage in the welder. They accumulate and release electrical energy rapidly, making them crucial for high-frequency operations. Regular inspections can prevent failure, which could lead to inconsistent welding and increased wear on other parts.
2. **Transformers**: The transformer in a solid-state HF welder converts and regulates voltage levels. A worn-out transformer can lead to voltage fluctuations and ineffective welding. When selecting transformers, ensure compatibility with your welder’s specifications.
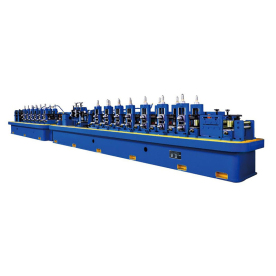
Essential Spare Parts for Solid State HF Welders: Importance, Selection, and Maintenance for Optimal Performance
3. **Diodes**: These semiconductor devices are vital for controlling the electrical flow. They rectify the alternating current from the power source into direct current. Monitor the diodes for signs of degradation, as a faulty diode can significantly impact the performance and safety of the welder.
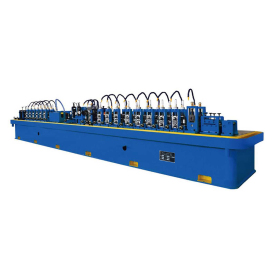
Essential Spare Parts for Solid State HF Welders: Importance, Selection, and Maintenance for Optimal Performance
4. **Inductors**: Used to store energy, inductors play a key role in maintaining the welding circuit’s stability. Over time, inductors can degrade, impacting the quality of the welds. Choosing a high-quality inductor will help ensure durability and reliability during operations.
5. **Cooling Fans**: As solid-state HF welders operate, they generate heat, which can lead to overheating if not managed properly. Quality cooling fans are integral in maintaining optimal operating temperatures and preventing equipment damage.
6. **Control Boards**: These are the brains of the welding machine, responsible for regulating the entire operation. Any malfunction with the control board can lead to complete system failure, making it essential to keep spare control boards available.
Selecting the Right Spare Parts
When selecting spare parts for solid-state HF welders, there are several factors you must consider:
1. **Compatibility**: Ensure that the spare part matches the specifications outlined in the welder’s manual. This includes checking voltage ratings, physical dimensions, and overall component design.
2. **Quality**: Opt for high-quality, genuine manufacturer parts whenever possible. When inferior quality components are used, they can result in further damage or reduced performance.
3. **Warranty and Support**: When buying spare parts, look for options that come with a warranty or customer support. This can provide peace of mind in the event of further issues down the line.
Best Practices for Maintenance
Additionally, implementing a strong maintenance program can prolong the lifespan of spare parts and the welder itself. Here are some best practices:
– **Regular Inspections**: Periodic checks on all major components can help identify potential issues before they escalate. Look for signs of wear, overheating, or unusual noises during operation.
– **Cleaning**: Dust and debris can accumulate in and around the welder, leading to performance issues. Regular cleaning can help maintain efficient operation and prolong the life of spare parts.
– **Documentation**: Keep records of any maintenance, repairs, and replacements. This will help track the welder’s history and can inform decisions regarding future upgrades or parts replacements.
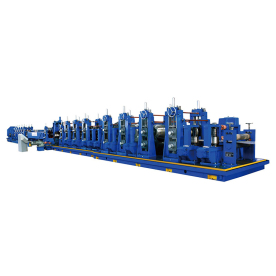
Essential Spare Parts for Solid State HF Welders: Importance, Selection, and Maintenance for Optimal Performance
In conclusion, understanding the essential spare parts for solid-state HF welders, along with proper selection and maintenance practices, is foundational for optimal performance. By prioritizing part integrity and regular maintenance, businesses can ensure high-quality welding results and minimize downtime, ultimately leading to greater productivity and reduced operational costs.Heat-Resistant HSS Blade