In the dynamic world of manufacturing, the reliability and efficiency of machinery play crucial roles in productivity and profit margins. Among the various machines that are pivotal to this industry, annealing machines are instrumental in refining materials’ properties, enhancing their strength, ductility, and other critical characteristics. However, like all machinery, annealing machines face wear and tear over time, leading to the need for effective maintenance. This is where Customized Annealing Machine Spare Parts come into play, offering solutions that not only keep machinery operational but also enhance their overall performance.
**Understanding the Role of Annealing Machines**
Annealing is a heat treatment process that alters the physical and sometimes chemical properties of a material. This process is particularly vital in metal and glass industries, where materials must meet specific strength and hardness criteria. Annealing machines are designed to heat materials to a particular temperature and then cool them at a controlled rate to achieve the desired properties. The efficiency and effectiveness of this process greatly depend on the prompt functioning of the machine, underscoring the need for quality spare parts.
**Importance of Customized Spare Parts**
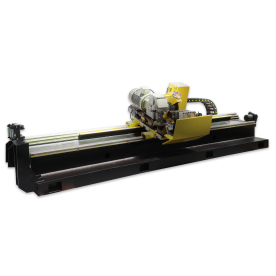
Maximizing Efficiency and Reducing Downtime with Customized Annealing Machine Spare Parts: A Comprehensive Guide for Modern Manufacturing
In a world where operations are increasingly automated and specialized, off-the-shelf spare parts often fall short of the specific requirements of different production scenarios. This is where Customized Annealing Machine Spare Parts offer significant advantages. Customized parts are designed and manufactured specifically to fit the unique configurations and operational demands of a given annealing machine.
1. **Precision Engineering**: Customized spare parts are fabricated to meet the exact specifications of existing equipment. This accuracy prevents the common issues that arise from misfits or incompatible components, which can lead to increased downtime and costly repair work.
2. **Increased Performance**: Tailoring components to specific operational needs results in better performance. For instance, the temperature control units, heating elements, or conveyor belts can be optimized, allowing for more efficient annealing cycles and improved energy consumption.
3. **Extended Machinery Life**: Regular wear can significantly reduce the overall life of annealing machines. However, using precisely engineered spare parts, which are resistant to the unique stresses and strains of the specific operating environment, can help prolong the life of the machine.
4. **Adaptability to Industry Changes**: Industries often need to adapt quickly to changing standards, materials, or processes. Customized spare parts provide the flexibility to make modifications that align with these shifts without the need to replace entire systems.
**Sourcing Customized Spare Parts**
Finding the right provider for Customized Annealing Machine Spare Parts is pivotal. Several factors should guide your choice:
– **Expertise**: Choose a supplier with a deep understanding of the annealing process and the specific requirements of your machinery. They should possess expertise in material science and engineering principles to produce high-quality parts.
– **Technological Integration**: Advanced manufacturing technologies such as 3D printing or CNC machining can enhance the customization process and accuracy. Opt for suppliers who utilize these technologies for superior outcomes.
– **Testing and Quality Assurance**: Your supplier should provide thorough testing and quality assurance for the customized parts to ensure they meet performance standards and comply with industry regulations.
– **Lead Time and Support**: Quick turnaround times and solid customer support are essential. An effective supplier should be able to deliver parts in a timely fashion and support you through installation and aftercare.
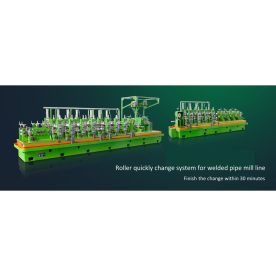
Maximizing Efficiency and Reducing Downtime with Customized Annealing Machine Spare Parts: A Comprehensive Guide for Modern Manufacturing
**Conclusion**

Maximizing Efficiency and Reducing Downtime with Customized Annealing Machine Spare Parts: A Comprehensive Guide for Modern Manufacturing
In conclusion, the use of Customized Annealing Machine Spare Parts is essential for manufacturers looking to enhance the operational efficiency, reliability, and longevity of their annealing processes. By investing in quality, tailored components, businesses can minimize downtime, improve production outcomes, and ultimately achieve better profitability. In a competitive market, prioritizing customized solutions will not only keep machines running smoothly but also provide a strategic advantage in adapting to the ever-evolving industrial landscape. The careful selection of suppliers and proactive maintenance practices will ensure that your annealing machinery remains at the forefront of performance standards, paving the way for sustained success.High-precision tube making machine