****
In today’s fast-paced industrial landscape, the need for efficiency and precision has never been greater. One technological advancement that stands at the forefront of this revolution is industrial-grade induction heating equipment. This innovative technology is redefining how various industries approach heating processes, leading to increased productivity, enhanced quality of work, and significant cost savings. In this article, we will explore the various applications of industrial-grade induction heating equipment and its many benefits that contribute to its rapid adoption across different sectors.
**Understanding Induction Heating Technology**
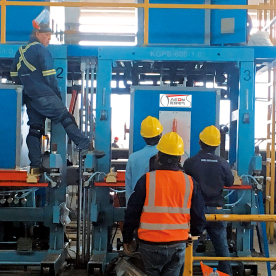
The Revolution in Manufacturing: How Industrial-Grade Induction Heating Equipment is Transforming Production Processes
Induction heating operates by using electromagnetic fields to generate heat within conductive materials, primarily metals. The process involves passing high-frequency currents through an induction coil, creating a magnetic field that induces electric currents—known as eddy currents—within the material. This results in rapid and localized heating, allowing for efficient thermal processing without any direct contact with the heating source.
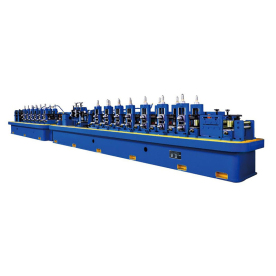
The Revolution in Manufacturing: How Industrial-Grade Induction Heating Equipment is Transforming Production Processes
**Applications Across Industries**
The versatility of industrial-grade induction heating equipment means that it can be applied in a multitude of industries, each benefiting uniquely from its capabilities. The following are some prominent applications:
1. **Metal Hardening and Annealing**: Many manufacturers utilize induction heating for hardening or annealing processes. The technology allows for precise control of temperature and heating times, ensuring that metals achieve the desired hardness without the risk of distortion, which can occur with traditional heating methods.
2. **Brazing and Soldering**: Induction heating is highly effective for brazing and soldering due to its ability to quickly achieve the necessary temperatures. It reduces heat-affected zones, minimizes oxide formation, and enhances the integrity of joints, making it a preferred choice in critical applications like aerospace and automotive manufacturing.
3. **Casting and Forging**: In casting and forging operations, maintaining temperature is crucial for the quality of the final product. Induction heaters can keep metals at optimal temperatures over extended periods, making them ideal for processes requiring long heating cycles.
4. **Plastic Welding and Joining**: Surprisingly, induction heating is also making waves in non-metal applications, such as plastic welding. The controlled heating allows for joining plastic components without the need for additional adhesives, ensuring a cleaner and more robust final product.
5. **Heating and Shrink Fitting**: Induction heating is used to heat metal components for shrink-fitting applications, such as fitting bearings onto shafts. The technology enables uniform heating, ensuring that components can be fitted together with precision, further enhancing the operational reliability of machinery.
**Advantages of Industrial-Grade Induction Heating Equipment**
The adoption of induction heating technology brings with it a host of advantages:
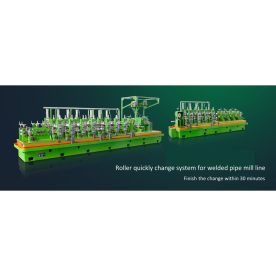
The Revolution in Manufacturing: How Industrial-Grade Induction Heating Equipment is Transforming Production Processes
1. **Energy Efficiency**: One of the most significant benefits of industrial-grade induction heating is its energy efficiency. Traditional heating methods often waste energy through radiation and convection. Induction heating, in contrast, heats only the target material, which greatly reduces energy consumption.
2. **Speed and Precision**: Induction heating systems can achieve desired temperatures in a fraction of the time compared to conventional heating methods. This rapidity not only improves production speeds but also allows for precise thermal control, ensuring consistent quality in manufacturing processes.
3. **Clean and Safe Operations**: Because induction heating does not produce an open flame, it inherently enhances workplace safety. The process is also cleaner, as there are fewer emissions and less risk of contamination, contributing to overall improved workplace conditions.
4. **Reduced Maintenance and Downtime**: Industrial-grade induction heating equipment typically requires less maintenance compared to traditional heating systems. This reduction in upkeep, combined with faster processing times, leads to decreased operational downtime.
5. **Scalability**: Whether for small batch production or large-scale manufacturing, induction heating equipment can easily be scaled to meet varying production needs, making it highly adaptable to different industrial environments.
**Conclusion**
As industries continue to evolve, the importance of efficiency, precision, and sustainability comes to the forefront. Industrial-grade induction heating equipment offers a transformative solution that enhances production processes across various sectors. Its exceptional capabilities not only improve operational efficiencies but also pave the way for innovations in processes that were previously limited by traditional heating methods. As technology advances and more manufacturers look to optimize their production, the adoption of induction heating is poised to become a standard practice in modern industrial operations.High-efficiency All-in-one Welding System