****
In today’s fast-paced manufacturing environment, the need for enhanced production capabilities cannot be overstated. Industries ranging from construction to automotive manufacturers increasingly rely on advanced machinery to meet their operational demands. Among these technologies, industrial tube making machinery has emerged as a key player, revolutionizing how businesses produce tubular products. This article delves into the intricacies of industrial tube making machinery, its applications, advantages, and the future potential it holds for various industries.
Understanding Industrial Tube Making Machinery
Industrial tube making machinery encompasses a diverse range of equipment designed to produce tubes of various materials, including metal, plastic, and composites. These machines utilize advanced techniques such as welding, extrusion, and bending to create tubes that meet precise specifications for different applications. The machinery can range from simple tube benders to complex systems that integrate multiple processes in a single production line.
Applications Across Multiple Sectors
The versatility of industrial tube making machinery makes it indispensable in various sectors. For instance, in the automotive industry, tubes are used in fuel lines, exhaust systems, and structural frameworks. The construction industry relies on these machines to produce structural steel tubes for buildings and infrastructure. Additionally, industries such as furniture manufacturing and electrical engineering utilize tube making machinery to create components for their products.
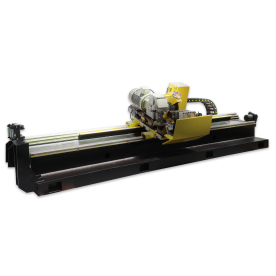
Revolutionizing Production Efficiency: The Role of Industrial Tube Making Machinery in the Modern Manufacturing Landscape
Moreover, with the rise of innovative materials, the application of industrial tube making machinery has expanded even further. Manufacturers can now produce lightweight yet durable tubes using advanced composites, catering to sectors such as aerospace, where weight reduction is crucial for efficiency.
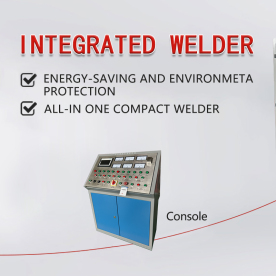
Revolutionizing Production Efficiency: The Role of Industrial Tube Making Machinery in the Modern Manufacturing Landscape
Advantages of Modern Tube Making Machinery
The adoption of industrial tube making machinery in manufacturing processes comes with numerous benefits. One of the most significant advantages is the increased efficiency it brings to production lines. Traditional methods of tube production can be labor-intensive and time-consuming. In contrast, modern machinery automates many of these processes, allowing manufacturers to produce higher volumes in less time.
Additionally, precision is a hallmark of industrial tube making machinery. Advanced technologies ensure that the final products meet exact specifications, which is critical in industries where tolerances are strict. This precision also reduces material waste, contributing to more sustainable manufacturing practices.
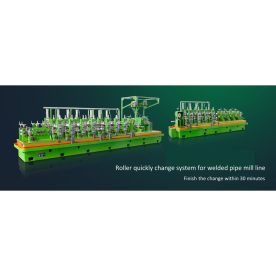
Revolutionizing Production Efficiency: The Role of Industrial Tube Making Machinery in the Modern Manufacturing Landscape
Cost-effectiveness is another critical advantage. While the initial investment in industrial tube making machinery may be substantial, the long-term savings in labor, production time, and material waste often outweigh those costs. Furthermore, the ability to quickly switch between different products and customize production runs makes this machinery adaptable to changing market demands.
Future Trends and Innovations
As technology advances, the future of industrial tube making machinery looks promising. Integrated smart technologies, such as the Internet of Things (IoT) and artificial intelligence (AI), are set to enhance machine capabilities. These innovations can lead to predictive maintenance, where machines can self-diagnose issues before they become significant problems, minimizing downtime and maximizing productivity.
Moreover, the trend toward automation is likely to continue, with more manufacturers adopting robotic systems to handle complex tasks alongside tube making machinery. This integration not only streamlines operations but also improves safety by reducing human exposure to potentially hazardous work environments.
Sustainability will also play a pivotal role in the evolution of industrial tube making machinery. As industries shift toward eco-friendly practices, machinery that minimizes energy consumption and waste production will become increasingly important. The development of equipment that can work with recycled materials will further enhance the sustainability profile of tube production.
Conclusion
Industrial tube making machinery stands as a cornerstone of modern manufacturing, offering significant advantages in efficiency, precision, and adaptability. With the continually evolving technology landscape, manufacturers are poised to leverage these advancements to meet ever-increasing production demands while also addressing sustainability challenges. As we look to the future, the role of industrial tube making machinery will likely expand, becoming even more integral to a myriad of industries and paving the way for innovative developments in product design and manufacturing processes. Embracing these technologies today positions companies for success in the increasingly competitive global market.Portable Solid state HF welder