High-frequency welding technology has emerged as a robust solution for various manufacturing and fabrication processes across multiple industries. As industries continue to evolve, the need for efficient, precise, and reliable welding equipment has never been more critical. The high-frequency welder stands out in this regard, offering a profound impact on production quality, speed, and overall operational efficiency. This article delves into the advantages of high-frequency welding, its applications, and why businesses should consider integrating this technology into their processes.
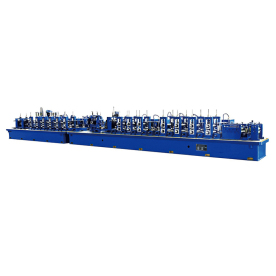
Exploring the Advantages and Applications of High Frequency Welders in Modern Manufacturing and Fabrication Processes
What is High-Frequency Welding?
High-frequency welding, also known as radio frequency (RF) welding, involves using high-frequency electromagnetic fields to join thermoplastic materials. The process generates heat within the material, effectively melting and fusing it together without the need for external heat sources. This technology is particularly advantageous for materials that are challenging to weld using traditional methods, such as PVC, polyethylene, and other thermoplastics.
Advantages of High-Frequency Welders
1. **Speed and Efficiency**: High-frequency welders are renowned for their speed and efficiency in manufacturing. The instantaneous nature of the process allows companies to increase their production rates significantly. Compared to traditional welding methods that may require extensive setup or cooling times, high-frequency welding achieves rapid joins.
2. **Superior Quality**: The resulting welds from high-frequency welders exhibit exceptional strength and durability. The consistent quality of welds minimizes defects and failures, ensuring products meet stringent quality standards. The precise control over the welding parameters provides manufacturers with the capability to achieve uniform results every time.
3. **Versatility**: High-frequency welding is highly versatile, suitable for a wide range of materials and applications. It can be applied in industries such as textiles, automotive, medical device manufacturing, and even packaging. This adaptability makes it an attractive option for manufacturers looking to diversify their product offerings.
4. **Reduced Material Waste**: The process is also known for its efficiency in material usage. High-frequency welding generates minimal thermal distortion, which reduces the risk of material waste during the welding process. This efficiency is particularly crucial in industries that deal with expensive materials, allowing businesses to optimize their raw material usage.
5. **Environmental Impact**: In an age where sustainability is paramount, high-frequency welding stands out for its minimal environmental impact. The method does not require additional solvents or adhesives, which are often detrimental to the environment. Furthermore, the reduction in material waste contributes to a more sustainable manufacturing process.
6. **Minimal Operator Skill Required**: Operating a high-frequency welder typically requires less specialized skill compared to traditional welding methods. This can facilitate training and enable a broader range of personnel to operate the equipment, further enhancing production capabilities.
Applications of High-Frequency Welders
The applications of high-frequency welders are broad and diverse, significantly impacting multiple sectors:
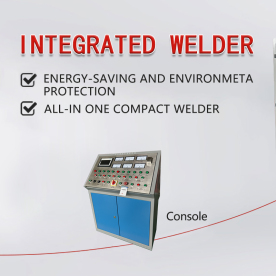
Exploring the Advantages and Applications of High Frequency Welders in Modern Manufacturing and Fabrication Processes
1. **Textile Industry**: Used extensively in creating seamless garments and technical textiles, high-frequency welding is a preferred method for joining fabric, especially for waterproof and airtight applications.
2. **Packaging**: High-frequency welded packaging solutions are prevalent in industries needing to ensure product integrity. This includes the production of vacuum-sealed bags and containers that require sturdy and reliable seals.
3. **Automotive Manufacturing**: The automotive industry utilizes high-frequency welding for fusing various components, including bumpers, interior upholstery, and even some electronic parts. The high strength and stability of these welds are critical for safety and performance.
4. **Medical Devices**: High-frequency welders play a pivotal role in manufacturing medical devices where precision and sterility are paramount. The ability to create hermetic seals is particularly beneficial in producing sterile packaging and components.
5. **Construction and Architecture**: In the construction sector, high-frequency welding is applied in creating durable and weather-resistant membranes for roofing and other applications.
Conclusion
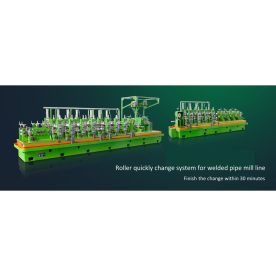
Exploring the Advantages and Applications of High Frequency Welders in Modern Manufacturing and Fabrication Processes
As manufacturing and fabrication processes continue to evolve, adopting innovative technologies like high-frequency welders is becoming increasingly important for achieving competitive advantages. The numerous benefits, including speed, efficiency, reduced waste, and superior quality, position high-frequency welding as a vital component in modern manufacturing. By understanding and leveraging these advantages, companies can enhance their operational efficiencies, meet consumer demands more effectively, and pave the way for a sustainable future in production practices. The high-frequency welder is not just a tool; it is an investment in a company’s future productivity and performance.Automatic Cold Cutting Saw Machine