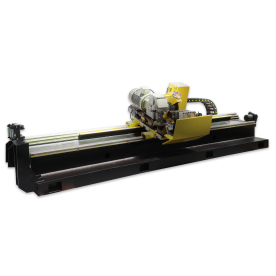
Exploring the Advantages of Solid State HF Welders with Temperature Control: A New Era in Precision Welding Technology
In the world of manufacturing and construction, precision is paramount, particularly when it involves joining materials. Solid state high-frequency (HF) welders with temperature control have emerged as a cutting-edge solution that not only enhances the integrity of welded joints but also improves the efficiency of production processes. This article delves into the functionality, advantages, and application areas of solid state HF welders that incorporate temperature control, highlighting why they are fast becoming the preferred choice for industries requiring reliable and high-quality welding.
Understanding Solid State HF Welding Technology
Solid state HF welding is a sophisticated welding process where high-frequency electrical energy is used to melt the edges of two components, enabling them to fuse together. This technology is particularly effective for joining thermoplastics, metals, and thin-wall materials. Unlike traditional welding methods, solid state HF welders utilize solid-state devices, such as transistors or diodes, to generate high-frequency current, which translates into greater efficiency, reliability, and flexibility.
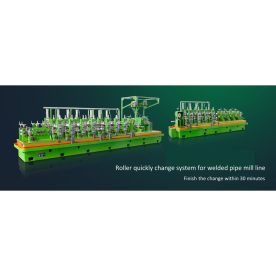
Exploring the Advantages of Solid State HF Welders with Temperature Control: A New Era in Precision Welding Technology
The Role of Temperature Control
One of the standout features of solid state HF welders is the integration of temperature control mechanisms. In welding, maintaining the correct temperature is crucial for achieving optimal results. Too much heat can lead to material distortion or even degradation, while insufficient heat may result in weak welds. Temperature control systems utilize real-time monitoring and feedback mechanisms to regulate the welding temperature precisely, ensuring that the materials being joined are subjected to the right amount of thermal energy. This results in stronger, more durable joints and minimizes the risk of defects.
Advantages of Solid State HF Welders with Temperature Control
1. **Enhanced Precision and Quality**: By controlling the temperature during the welding process, solid state HF welders produce high-quality welds with tighter tolerances. This precision is especially important in industries such as automotive manufacturing, aerospace, and electronics, where even a minor defect can lead to catastrophic failures.
2. **Increased Production Efficiency**: Temperature-controlled welding allows for faster cycles, as the machine can adapt to the specific requirements of each weld in real-time. This adaptability leads to reduced downtime and increases overall productivity.

Exploring the Advantages of Solid State HF Welders with Temperature Control: A New Era in Precision Welding Technology
3. **Energy Efficiency**: Solid state technologies use significantly less energy compared to traditional welding systems. The efficient generation of high-frequency currents results in less thermal waste, making these welders a more sustainable option for manufacturers focused on reducing their environmental footprint.
4. **Versatility in Applications**: Solid state HF welders with temperature control can be employed across various materials and thicknesses, from thin films to thicker substrates. This versatility makes them suitable for numerous applications, including medical device manufacturing, packaging, automotive parts, and more.
5. **Improved Safety**: Advanced temperature control mechanisms enhance operator safety by reducing the risk of overheating, which can lead to hazardous situations. Moreover, the solid state setup minimizes the need for high-voltage components, making these machines safer to operate.
Applications in Various Industries
The impact of solid state HF welders with temperature control is felt across multiple sectors. In the **packaging industry**, they facilitate quick and reliable sealing of plastic materials, ensuring that products remain safe during transport and storage. In **medical device manufacturing**, the precision offered by these welders is essential for creating sterilized and reliable components that meet stringent health standards.
The **automotive industry** benefits from such technology by utilizing these welders for assembling parts that require strong and durable joints, such as battery packs and body panels. Additionally, in **electronics**, the technology is leveraged for high-speed bonding of wires and components, enhancing the performance and reliability of complex devices.
Conclusion
Solid state HF welders with temperature control represent a revolutionary advancement in welding technology. Their ability to ensure precision, improve efficiency, and enhance safety makes them indispensable in today’s manufacturing landscape. As industries continue to demand higher standards of quality and sustainability, the adoption of solid state HF welding technology is poised to grow, leading to even more innovative applications. With these welders, manufacturers can not only meet their production targets but also contribute positively to their environmental goals, paving the way for a more efficient and sustainable future.Spare Parts Kit for Tube Mills