****
In today’s fast-paced manufacturing environment, precision and efficiency are paramount. As industries continuously seek to enhance production processes, high-precision tube making machines have emerged as pivotal technologies. These machines not only streamline production but also ensure that the final products meet stringent quality standards. This article delves into the features, benefits, and the evolving landscape of high-precision tube making machines, highlighting their significance in various industrial applications.
High-precision tube making machines are designed to produce tubes with exact dimensions and tolerances. These machines utilize advanced technologies, such as numerically controlled machinery, laser cutting, and automatic feeding systems, to ensure that every length and diameter of the tube is consistent. The result is a product that not only fits seamlessly into its intended application but also performs reliably under various conditions.
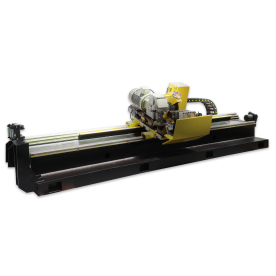
Exploring the Innovations and Advantages of High-Precision Tube Making Machines in Modern Manufacturing
One of the primary benefits of high-precision tube making machines is their ability to significantly reduce waste. Traditional tube-making processes often involve a substantial amount of leftover material due to inaccuracies in cutting and shaping. However, with high-precision technology, manufacturers can optimize material usage, reducing scrap and saving costs. This efficiency not only translates to financial savings but also contributes to more sustainable manufacturing practices, making it an attractive option for environmentally conscious companies.
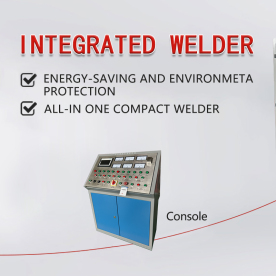
Exploring the Innovations and Advantages of High-Precision Tube Making Machines in Modern Manufacturing
The versatility of high-precision tube making machines further enhances their appeal. They are capable of producing a wide range of tube sizes and shapes, allowing manufacturers to cater to various markets, from automotive components to medical devices. With the increasing demand for customized products, these machines can be easily programmed to accommodate specific requirements, thus enabling rapid response to market changes.
Moreover, the integration of advanced automation and smart technology into high-precision tube making machines has revolutionized the manufacturing process. Owners of modern machinery can now benefit from real-time monitoring and control, which ensures consistent quality throughout production runs. This advantage is especially crucial in industries like aerospace and pharmaceuticals, where compliance with strict regulatory standards is mandatory.
The durability and reliability of high-precision tube making machines also deserve attention. Built with robust materials and cutting-edge engineering, these machines are designed to operate efficiently for extensive periods. Less machine downtime means increased productivity and enhanced return on investment. Additionally, many manufacturers now offer remote support services, allowing for quick troubleshooting and maintenance, thus further reducing the strain on operational efficiency.
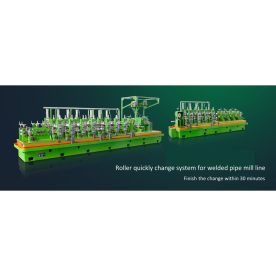
Exploring the Innovations and Advantages of High-Precision Tube Making Machines in Modern Manufacturing
As the market continues to evolve, it’s essential for businesses to keep up with the latest advancements in high-precision tube making machines. Innovations such as artificial intelligence and machine learning are gradually becoming integral components in enhancing machine performance. For instance, predictive maintenance powered by AI can assess machine conditions and anticipate potential failures before they occur, minimizing downtime and repair costs.
Furthermore, the collaboration of high-precision tube making machines with additive manufacturing techniques highlights a transformative trend in production capabilities. This hybrid approach allows manufacturers to create complex geometries that were traditionally challenging to produce. This not only opens the door to new design possibilities but also enables the production of lightweight parts that enhance overall product performance.
In conclusion, high-precision tube making machines have become essential in modern manufacturing, offering numerous benefits such as reduced waste, versatility, and enhanced productivity. As the demand for high-quality, customized products continues to rise, these machines will play a crucial role in meeting both industry and consumer expectations. Embracing these innovations not only positions companies to compete effectively in the market but also sets the stage for a more sustainable and efficient manufacturing future. Thus, investing in high-precision tube making machines is not just a practical move—it’s also a forward-looking strategy in an ever-evolving industrial landscape.Custom-Made Spare Parts for Solid State HF Welders